Assembly Line Manager Job Description [Updated for 2025]
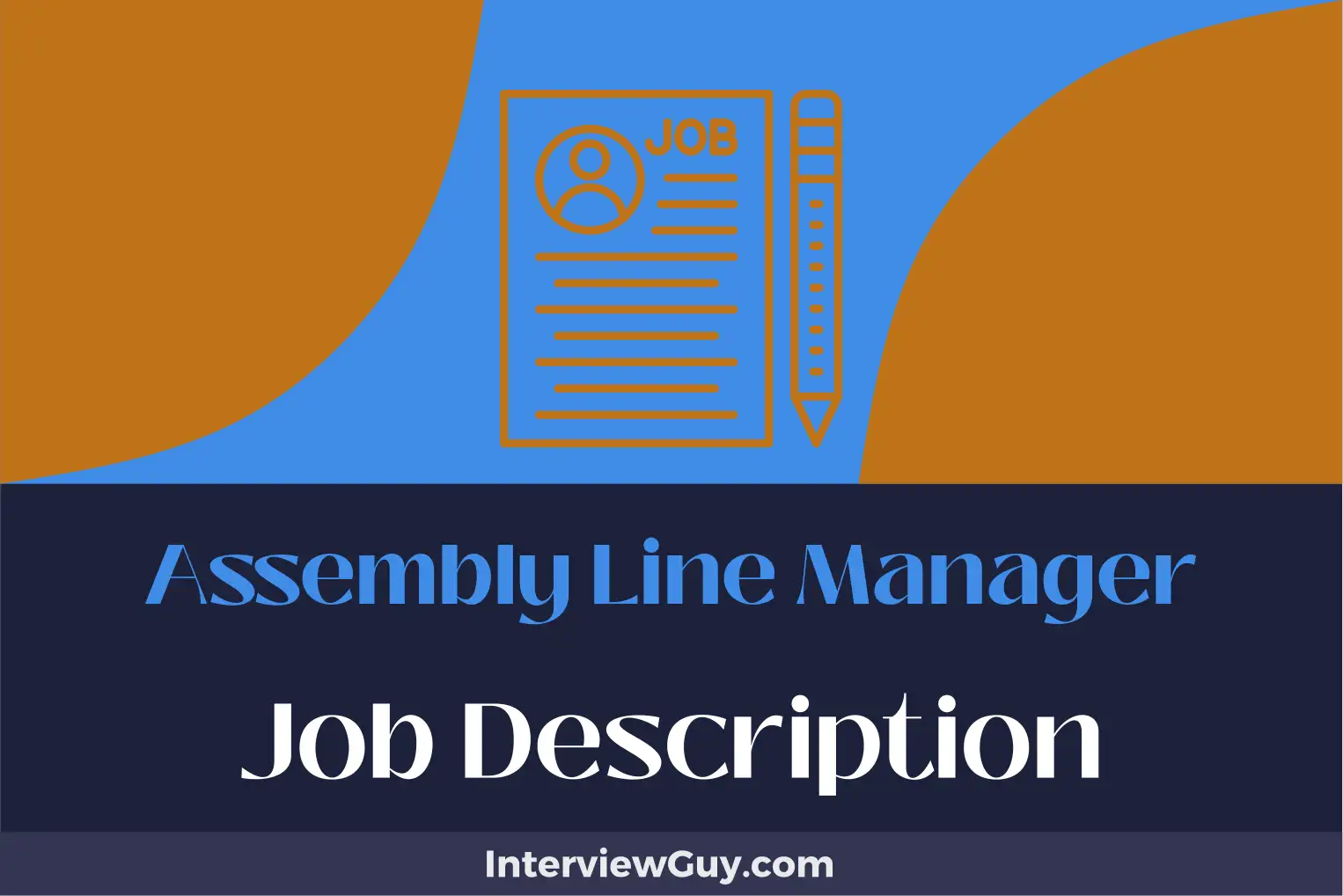
In the era of modern manufacturing, the role of assembly line managers has become more crucial than ever.
As production processes evolve and become more complex, the demand for skilled professionals who can manage, optimize, and ensure the smooth operation of assembly lines grows.
But let’s delve deeper: What’s really expected from an assembly line manager?
Whether you are:
- A job seeker trying to understand the core of this role,
- A hiring manager trying to outline the perfect candidate,
- Or simply fascinated by the ins and outs of assembly line management,
You’re in the right place.
Today, we present a customizable assembly line manager job description template, crafted for easy posting on job boards or career sites.
Let’s dive right in.
Assembly Line Manager Duties and Responsibilities
Assembly Line Managers oversee and manage the production line workers and operations to ensure efficiency and productivity.
They are responsible for ensuring that the assembly line runs smoothly and that the workers are performing their tasks correctly and efficiently.
The duties and responsibilities of an Assembly Line Manager include:
- Overseeing and coordinating the activities of assembly line workers
- Implementing and managing production schedules to ensure timely delivery of products
- Ensuring that all the machinery and equipment are in good working condition
- Training and supervising assembly line workers, and ensuring they comply with safety and quality standards
- Inspecting the assembled products to ensure that they meet the required specifications and quality standards
- Identifying and resolving production line problems in a timely manner
- Maintaining and updating records of daily production, machine malfunctions, and production process
- Communicating with other department managers to coordinate and plan production activities
- Implementing and enforcing safety rules and regulations on the assembly line to prevent accidents and injuries
- Conducting performance evaluation of assembly line workers and providing them with feedback
Assembly Line Manager Job Description Template
Job Brief
We are seeking a dedicated Assembly Line Manager to oversee our production operations.
The Assembly Line Manager will be responsible for ensuring that our production lines run smoothly and efficiently, meeting both quality and quantity goals.
The ideal candidate will have a strong background in production management, with a keen eye for detail and a results-driven approach.
They should be able to manage people and resources, analyze production data, and drive continuous improvement on the assembly line.
Responsibilities
- Manage and oversee the assembly line production process
- Develop and implement production schedules and procedures
- Identify issues in efficiency and suggest improvements
- Train new employees on how to safely use machinery and follow procedures
- Ensure that safety rules and regulations are adhered to
- Monitor production output and ensure all quality standards are met
- Provide regular updates to senior management on production progress and challenges
- Coordinate maintenance and repair of machinery to prevent production delays
- Manage budgets and production costs
Qualifications
- Proven work experience as an Assembly Line Manager or similar role in a manufacturing environment
- Knowledge of production procedures and machine operation
- Ability to read and understand technical manuals for equipment operations
- Strong team management and communication skills
- High level of organizational and problem-solving abilities
- BSc degree in Engineering, Business Administration or relevant field
Benefits
- 401(k)
- Health insurance
- Dental insurance
- Retirement plan
- Paid time off
- Professional development opportunities
Additional Information
- Job Title: Assembly Line Manager
- Work Environment: This position requires work in a manufacturing plant. Safety gear is required and will be provided.
- Reporting Structure: Reports to the Production Director or Operations Manager.
- Salary: Salary is based upon candidate experience and qualifications, as well as market and business considerations.
- Pay Range: $60,000 minimum to $85,000 maximum
- Location: [City, State] (specify the location or indicate if remote)
- Employment Type: Full-time
- Equal Opportunity Statement: We are an equal opportunity employer and value diversity at our company. We do not discriminate on the basis of race, religion, color, national origin, gender, sexual orientation, age, marital status, veteran status, or disability status.
- Application Instructions: Please submit your resume and a cover letter outlining your qualifications and experience to [email address or application portal].
What Does an Assembly Line Manager Do?
Assembly Line Managers usually work in manufacturing industries where they oversee the production process of a product.
They are responsible for managing employees, setting up assembly line schedules, and ensuring that products are manufactured on time and to the required quality standards.
Assembly Line Managers often work with other department managers to coordinate manufacturing processes, troubleshoot issues, and improve production efficiency.
They are tasked with monitoring the assembly line operations, addressing any mechanical problems, and ensuring the safety of workers on the line.
Assembly Line Managers are also accountable for training new employees, performing quality control checks, and implementing cost-effective strategies to enhance productivity and profitability.
They may also have the responsibility to maintain records of production, prepare reports, and ensure compliance with industry standards and regulations.
The role of an Assembly Line Manager is crucial in ensuring that the product meets the company’s expectations in terms of quality, cost, and timeline.
Assembly Line Manager Qualifications and Skills
An effective Assembly Line Manager should possess certain skills and qualifications to ensure smooth operation and efficient production, such as:
- Exceptional coordination skills to oversee the assembly line operations, ensuring all parts and processes come together at the right time.
- Technical knowledge about the product and production processes to understand and improve assembly line functioning.
- Leadership abilities to guide, manage, and motivate a team, fostering a productive and positive work environment.
- Effective communication skills to relay information to employees, superiors, and subordinates efficiently and clearly.
- Problem-solving skills to quickly identify and address issues that might disrupt the assembly line production.
- Decision-making abilities to make crucial judgments that can affect the production process, ensuring optimum productivity and quality.
- Time management skills to ensure that production schedules are met and deadlines are not overrun.
- Knowledge of safety regulations and the ability to enforce them, maintaining a safe and healthy work environment.
- Understanding of quality control processes to ensure the final product meets the required standards.
Assembly Line Manager Experience Requirements
Assembly Line Managers typically need to have at least 3 to 5 years of experience in a manufacturing environment, with a significant portion of that time spent on the assembly line itself.
This hands-on experience is critical in understanding the workflow, safety standards, and production challenges that are unique to this type of work.
Experience in a supervisory or leadership role is also a significant advantage, as the Assembly Line Manager will be responsible for coordinating the work of several employees, managing production targets, and ensuring that quality standards are met consistently.
Additional experience in areas like inventory management, equipment maintenance, and lean manufacturing processes can also be extremely beneficial.
These skills help to improve efficiency and reduce waste on the assembly line, which can significantly increase the profitability of the manufacturing operation.
Candidates with extensive experience in these areas may be eligible for senior or executive-level roles, where they will be responsible for overseeing multiple assembly lines and coordinating the overall production strategy.
Many employers prefer candidates with a bachelor’s degree in a related field, although substantial industry experience can sometimes be used as a substitute for formal education.
Continual professional development, such as staying up to date with the latest industry trends and advances in assembly line technology, can also be a valuable asset for Assembly Line Managers.
Assembly Line Manager Education and Training Requirements
Assembly Line Managers generally possess a bachelor’s degree in business administration, management, industrial engineering, or a related field.
They are typically expected to have a strong understanding of production processes, as well as knowledge of basic mechanics and computer systems.
They should also be well-versed with quality control, production planning, and other relevant industrial operations.
Many employers prefer candidates with previous experience in an assembly line setting, which may include roles such as assembly line worker, supervisor, or team lead.
This experience helps managers understand the day-to-day operations and challenges of the assembly line.
Some positions may require specialized training or certification in lean manufacturing or Six Sigma methodologies, which focus on eliminating waste and improving production efficiency.
While not always required, a master’s degree in business administration (MBA) or industrial management can make a candidate more competitive for higher-level managerial positions.
Continuing education and professional development opportunities, such as seminars or workshops on leadership, team building, or production management, can also be beneficial for Assembly Line Managers.
Assembly Line Manager Salary Expectations
The average salary for an Assembly Line Manager is $58,000 (USD) per year.
However, this can fluctuate based on factors such as level of experience, the industry in which they are employed, and the geographical location of the job.
Assembly Line Manager Job Description FAQs
What skills does an Assembly Line Manager need?
Assembly Line Managers should have excellent leadership and communication skills, as they are responsible for guiding and instructing their team members.
They should also have great problem-solving skills, as they will need to efficiently solve any issues that may arise on the assembly line.
A solid understanding of the production process and technical skills related to the product or equipment are also crucial.
Do Assembly Line Managers need a degree?
While not always required, many companies prefer Assembly Line Managers to have a bachelor’s degree in business management, industrial engineering, or a related field.
However, extensive experience in manufacturing or assembly line work can also be accepted in lieu of formal education.
Certification in production and inventory management can also be beneficial.
What should you look for in an Assembly Line Manager’s resume?
Look for evidence of leadership, problem-solving, and technical skills on an Assembly Line Manager’s resume.
This can include managing teams, coordinating production schedules, and implementing efficiency improvements.
Additionally, check for experience in the specific industry of your company as well as any relevant certifications or degrees.
What qualities make a good Assembly Line Manager?
A good Assembly Line Manager is a strong leader who can motivate and direct a team.
They are organized and detail-oriented, ensuring that all aspects of the assembly line run smoothly.
They are also problem solvers who can quickly address and resolve any issues that arise.
Additionally, they should have a strong understanding of safety regulations and ensure these are adhered to.
What are the daily duties of an Assembly Line Manager?
The daily duties of an Assembly Line Manager include overseeing the assembly line operations, managing assembly line workers, coordinating with other departments, and ensuring the production schedule is maintained.
They are also responsible for maintaining safety regulations, managing inventory, implementing efficiency improvements, and troubleshooting any issues that arise on the assembly line.
Conclusion
There you have it.
Today, we’ve unraveled the complexities of what it truly means to be an assembly line manager.
And guess what?
It’s not just about overseeing production.
It’s about orchestrating efficiency and accuracy, one assembly line at a time.
Armed with our comprehensive assembly line manager job description template and real-world examples, you’re ready to make your move.
But don’t just stop there.
Go beyond with our job description generator. It’s your next step towards creating precision-crafted job listings or fine-tuning your resume to perfection.
Remember:
Every assembly line is a cog in the vast machine of production.
Let’s construct that future. Together.
How to Become an Assembly Line Manager (Complete Guide)
Rich Rewards: Unearthing the Most Lucrative Careers of the Year!
Eccentrically Employed: The Most Unusual Jobs in the World
No Stress, More Cash: Easy Jobs That Are Unexpectedly Profitable!
Wage Warning: Jobs That May Not Support Your Financial Goals