Concrete Plant Manager Job Description [Updated for 2025]
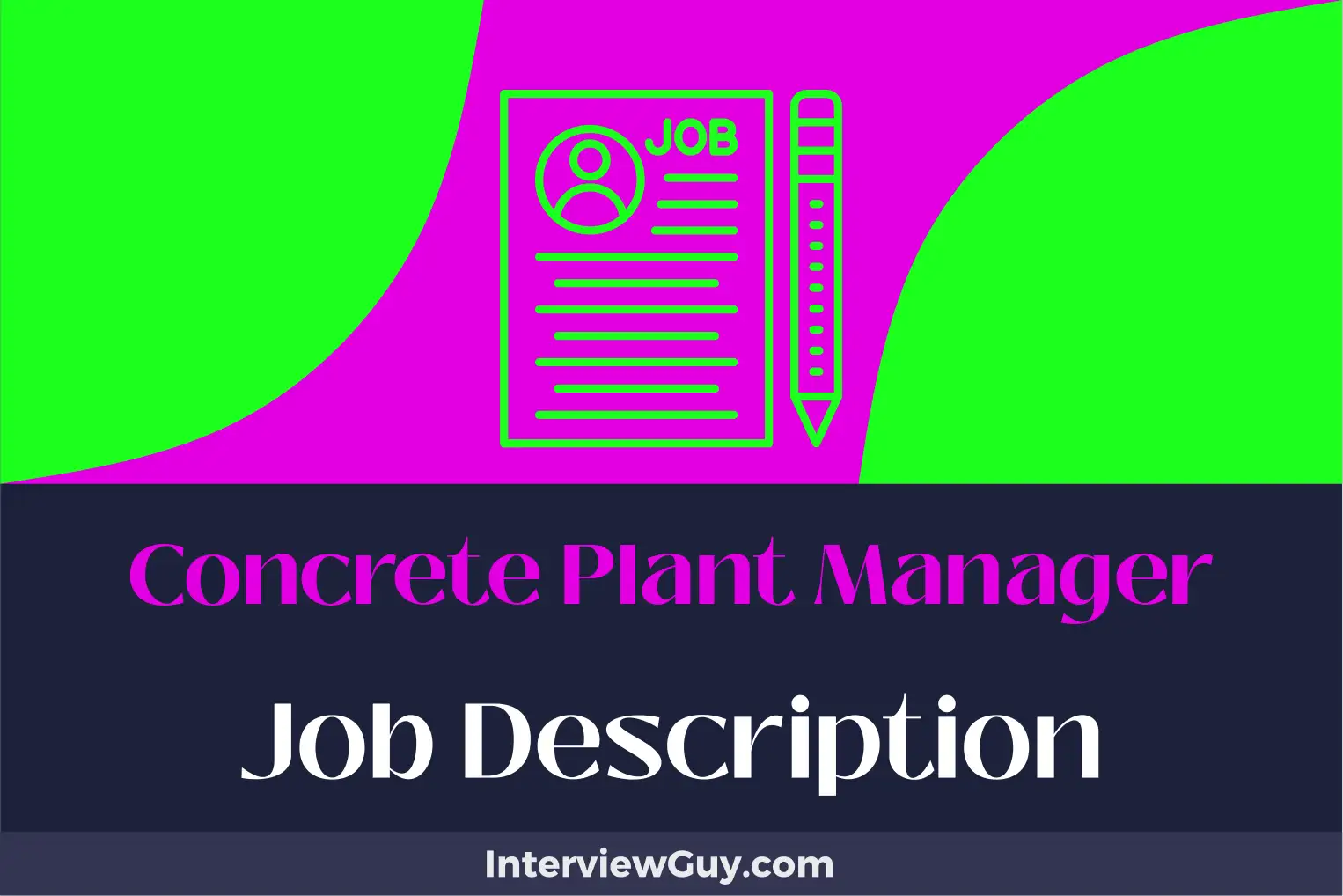
In the era of modern construction, the role of a Concrete Plant Manager is more crucial than ever.
As infrastructural developments proceed at a rapid pace, the demand for skilled individuals who can oversee, manage, and safeguard our concrete production processes intensifies.
But let’s delve deeper: What’s truly expected from a Concrete Plant Manager?
Whether you are:
- A job seeker trying to understand the core of this role,
- A hiring manager outlining the perfect candidate,
- Or simply interested in the nitty-gritty of concrete plant management,
You’ve come to the right place.
Today, we are presenting a customizable Concrete Plant Manager job description template, designed for effortless posting on job boards or career sites.
Let’s dive right in.
Concrete Plant Manager Duties and Responsibilities
Concrete Plant Managers oversee the operational and administrative functions of concrete production plants.
They ensure the efficient and cost-effective production of concrete materials while adhering to safety standards and regulations.
Their duties and responsibilities include:
- Direct and coordinate daily operations of the concrete plant
- Inspect and monitor plant equipment and machinery, arranging for necessary maintenance and repairs
- Ensure the plant complies with safety and environmental regulations
- Oversee the loading and dispatching of concrete deliveries
- Manage inventory of raw materials and ensure consistent supply
- Coordinate with other departments to maintain production schedules
- Assist in the development and implementation of plant policies and procedures
- Lead team of plant employees and conduct performance evaluations
- Prepare and manage the plant budget
- Manage quality control of the concrete product
- Train new staff and ensure all employees understand safety procedures
- Deal with customer queries and complaints
Concrete Plant Manager Job Description Template
Job Brief
We are seeking a dedicated Concrete Plant Manager to oversee all aspects of our concrete manufacturing operations.
The Concrete Plant Manager will be responsible for managing production activities, ensuring quality control, implementing safety measures, and coordinating maintenance and repairs.
The ideal candidate should be highly knowledgeable about the concrete industry, exhibit strong leadership qualities, and have excellent problem-solving skills.
Ultimately, the Concrete Plant Manager will ensure that our plant operations run efficiently, while meeting and exceeding our production, safety, and quality standards.
Responsibilities
- Oversee daily operations of the concrete plant
- Ensure safety and health regulations are complied with
- Monitor all production processes
- Plan and direct the maintenance and repair of plant equipment
- Ensure optimal utilization of resources (material and personnel)
- Ensure quality control standards are met
- Coordinate with other departments to align production and delivery schedules
- Train, supervise, and mentor plant staff
- Prepare and maintain production reports
- Manage inventory and order necessary supplies
Qualifications
- Proven experience as a Plant Manager or similar role in the concrete industry
- Knowledge of industry safety standards and regulations
- Understanding of quality control procedures and relevant legal standards
- Excellent problem-solving and team management abilities
- Good knowledge of performance evaluation metrics
- Proficient in MS Office and knowledge of relevant software (e.g. ERP)
- BSc/Ba in Business Administration, Engineering or relevant field
Benefits
- 401(k)
- Health insurance
- Dental insurance
- Retirement plan
- Paid time off
- Opportunities for professional growth
Additional Information
- Job Title: Concrete Plant Manager
- Work Environment: This role requires working in a plant environment with extended periods of standing and moving around heavy machinery. Protective gear may be required.
- Reporting Structure: Reports to the Operations Manager or General Manager.
- Salary: Salary is based upon candidate experience and qualifications, as well as market and business considerations.
- Pay Range: $65,000 minimum to $105,000 maximum
- Location: [City, State] (specify the location)
- Employment Type: Full-time
- Equal Opportunity Statement: We are an equal opportunity employer and value diversity at our company. We do not discriminate on the basis of race, religion, color, national origin, gender, sexual orientation, age, marital status, veteran status, or disability status.
- Application Instructions: Please submit your resume and a cover letter outlining your qualifications and experience to [email address or application portal].
What Does a Concrete Plant Manager Do?
A Concrete Plant Manager oversees the operations of a concrete production facility.
They are responsible for ensuring that the plant operates efficiently, safely, and produces high-quality concrete according to specifications.
Their job entails coordinating and supervising all aspects of the concrete production process, including raw material intake, batching, and concrete mixing procedures.
They ensure that the production process is compliant with industry standards and regulations.
Concrete Plant Managers also oversee the maintenance of the plant and its machinery, scheduling regular checks and repairs to avoid downtime and ensure the facility’s optimal operation.
They work closely with quality control teams to ensure that the produced concrete meets the necessary quality standards.
They may also be involved in the testing and analysis of concrete samples.
Moreover, they are responsible for managing the plant’s workforce, including hiring, training, and performance evaluation of staff.
They ensure that all employees adhere to safety protocols and regulations.
They often also manage the plant’s budget, controlling costs, and ensuring efficiency in operations.
They are also responsible for maintaining inventory levels of raw materials and other supplies.
Concrete Plant Managers are also typically in charge of customer service, handling client queries and complaints, and ensuring customer satisfaction.
They work to build strong relationships with clients and ensure that their needs and expectations are met.
They are also responsible for ensuring that the plant operates in an environmentally responsible manner, adhering to all relevant environmental regulations and sustainable practices.
Concrete Plant Manager Qualifications and Skills
A Concrete Plant Manager should possess a range of technical and leadership skills, as well as industry knowledge to successfully manage and oversee the operations of a concrete production plant, such as:
- Comprehensive understanding of concrete production and associated machinery to ensure efficient and safe operation.
- Exceptional leadership and management skills to direct and oversee staff, ensuring they adhere to safety protocols and meet performance standards.
- Problem-solving skills to swiftly identify and rectify any issues that may arise in the production process or with machinery.
- Strong communication skills to liaise with suppliers, staff and clients, and to ensure clear instructions and expectations are delivered.
- Knowledge of industry safety regulations and procedures to maintain a safe working environment.
- Customer service skills to establish and maintain positive relationships with clients and manage their orders and queries effectively.
- Organizational skills to manage inventory, schedule maintenance, oversee deliveries and ensure production deadlines are met.
- Ability to physically inspect machinery and the production process, ensuring quality control and adherence to standards.
Concrete Plant Manager Experience Requirements
Concrete Plant Managers typically have at least 5-7 years of experience in the concrete industry.
This experience often begins with a hands-on role in concrete production, such as a Concrete Batch Plant Operator or a Quality Control Technician.
This offers the individual a solid understanding of concrete manufacturing processes, quality control measures, and safety regulations.
Some concrete plant managers may also have a background in civil engineering or a related field.
This provides them with a scientific understanding of concrete and its applications, which can be extremely useful for managing a concrete plant effectively.
In addition, many concrete plant managers have experience in a supervisory or managerial role.
This could be within the concrete industry, or in another industry with similar manufacturing processes.
This experience should typically include personnel management, production scheduling, inventory management, and compliance with safety regulations.
Finally, many employers prefer concrete plant managers to have some experience with industry-specific software, such as concrete batching software or construction management software.
This helps to ensure that the plant manager can effectively oversee the plant’s operations.
Those with over 10 years of experience in the industry, including multiple years in a managerial role, are often considered for senior management positions within the company.
Concrete Plant Manager Education and Training Requirements
To become a Concrete Plant Manager, a bachelor’s degree in construction management, civil engineering, or a related field is typically required.
This education provides a strong foundation in project management, cost estimation, construction methods, and principles of design, which are critical to this role.
Some positions may prefer candidates with a master’s degree in business administration or a related field, particularly for larger projects or more senior management roles.
In terms of professional training, familiarity with concrete production processes, plant equipment, and industry safety standards is important.
This could be obtained through on-the-job training, internships or apprenticeships in construction or manufacturing settings.
Additionally, concrete plant managers may need to have certifications such as the Certified Construction Manager (CCM) or similar.
Practical experience in the construction industry, including roles in project management, supervision or concrete production, is usually essential.
Many plant managers advance to their positions after years of experience in various roles within the industry.
Continued professional development is crucial in this role due to ongoing changes in construction materials, techniques, and regulations.
Therefore, a commitment to lifelong learning and keeping up-to-date with industry advancements is important for a concrete plant manager.
Concrete Plant Manager Salary Expectations
The average salary for a Concrete Plant Manager is $78,500 (USD) per year.
Actual earnings can fluctuate based on the level of experience, the location of the plant, the size of the plant, and the employing company.
Concrete Plant Manager Job Description FAQs
What skills does a Concrete Plant Manager need?
A Concrete Plant Manager must possess strong leadership and managerial skills to manage an entire plant operation effectively.
They need to have a comprehensive understanding of concrete production, quality control methods, and safety protocols.
A deep knowledge of industry regulations and standards is also essential.
Additionally, they must possess excellent communication and problem-solving skills to address issues promptly and maintain efficient production.
Do Concrete Plant Managers need a degree?
While it is not strictly necessary for a Concrete Plant Manager to have a degree, most employers prefer candidates with a degree in Civil Engineering, Construction Management, or a related field.
Extensive experience in concrete plant operations, including supervisory or managerial roles, can sometimes substitute for formal education.
Also, certain certifications related to concrete production and quality control may be beneficial.
What should you look for in a Concrete Plant Manager resume?
A strong Concrete Plant Manager resume should demonstrate a candidate’s experience in managing concrete plant operations, including overseeing production, quality control, and safety compliance.
Look for knowledge of relevant industry regulations and standards.
Evidence of strong leadership, communication skills, and problem-solving abilities are also desirable.
Certifications related to concrete production or plant management can also be a plus.
What qualities make a good Concrete Plant Manager?
A good Concrete Plant Manager is a strong leader who can oversee and coordinate all aspects of plant operations effectively.
They must be problem-solvers who can quickly address issues and maintain efficient production.
They must be detail-oriented to ensure product quality and compliance with safety and industry standards.
Good communication skills are also important for coordinating with staff and addressing any issues that arise.
Is it difficult to hire Concrete Plant Managers?
The difficulty in hiring a Concrete Plant Manager can depend on the specific requirements of the job and the local job market.
These roles often require a combination of education and extensive industry experience, which can limit the pool of qualified candidates.
Offering competitive salary and benefits can help attract top talent.
It may also be beneficial to work with recruitment agencies specializing in construction and engineering roles.
Conclusion
And there you have it.
Today, we’ve taken a closer look at what it truly means to be a Concrete Plant Manager.
And guess what?
It’s not just about mixing and pouring concrete.
It’s about constructing the future, one batch of concrete at a time.
With our comprehensive concrete plant manager job description template and practical examples, you’re fully equipped to make your next move.
But why draw the line here?
Delve deeper with our job description generator. It’s your subsequent step to meticulously-crafted job listings or refining your resume to perfection.
Remember:
Every batch of concrete is a part of a larger structure.
Let’s build that future. Together.
How to Become a Concrete Plant Manager (Complete Guide)
The Unusual Career Spectrum: Jobs That Are Out of the Ordinary
AI’s Human Challenge: Jobs That Machines Can’t Master
Steady as She Goes: Recession-Proof Jobs for a Secure Future
Elite of the Elite: The Most Prestigious Careers You Can Dream Of