26 Disadvantages of Being an Industrial Maintenance Mechanic (Behind the Grease)
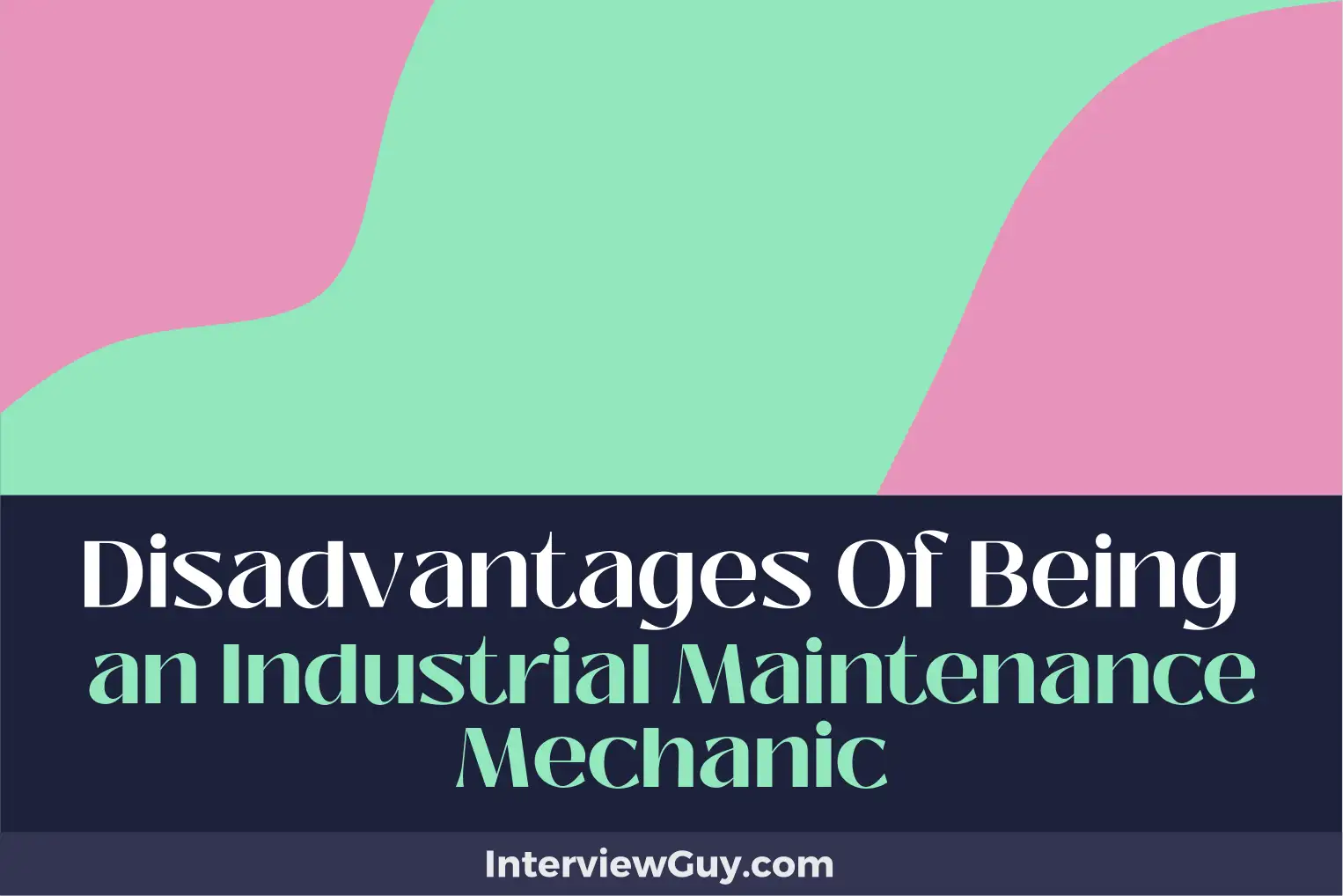
Considering a career as an industrial maintenance mechanic?
It’s easy to fall for the appeal:
- Stable job market.
- Competitive salaries.
- The satisfaction of keeping a production line running smoothly.
But there’s more beneath the surface.
Today, we’re going deep. Real deep.
Into the intricate, the strenuous, and the downright tough aspects of being an industrial maintenance mechanic.
Complex technical knowledge? Check.
Investment in continuous training and certification? You bet.
Physical strain from heavy-duty work? Absolutely.
And let’s not forget the responsibility of preventing costly downtimes.
So, if you’re contemplating a career in industrial maintenance, or just curious about what’s beyond those nuts, bolts and gears…
Stay tuned.
You’re about to receive a comprehensive look at the disadvantages of being an industrial maintenance mechanic.
Physically Demanding Work Environment
Industrial Maintenance Mechanics often work in physically demanding conditions.
The job usually involves heavy lifting, bending, kneeling, and climbing ladders to maintain and repair industrial equipment.
Moreover, these mechanics may have to work in confined spaces or at heights, which can be hazardous if not properly trained and equipped.
This physical strain might not only lead to fatigue but also increases the risk of on-the-job injuries.
Dealing with heavy machinery can be strenuous, and it often requires a high level of physical fitness and stamina.
Over time, the physical demands of the job could potentially lead to chronic health issues such as back pain or hearing loss.
The work environment is typically noisy, and despite using protective equipment, long-term exposure to such conditions could have an impact on health.
Exposure to Potentially Hazardous Machinery and Materials
Industrial Maintenance Mechanics often work directly with heavy machinery and equipment that can be potentially hazardous if not handled correctly.
These machines can have moving parts, sharp edges, extreme temperatures, or high voltage electrical components that can pose a risk of injury.
Additionally, these professionals might encounter harmful materials such as lubricants, cutting fluids, or asbestos.
Therefore, they need to always be alert and follow strict safety protocols to minimize the risk of accidents and injuries.
Moreover, constant exposure to these hazards may also have long-term health implications.
Protective equipment is often required to be worn at all times, which can be uncomfortable and restrictive.
Risk of Injury From Equipment or On-Site Accidents
Industrial Maintenance Mechanics often work in hazardous environments and with heavy machinery.
This line of work comes with a certain degree of risk, as they are exposed to potentially dangerous situations on a daily basis.
They may be tasked with repairing or maintaining machinery that can cause injuries if not handled properly.
Additionally, they may have to work in high places or cramped spaces, increasing the chances of on-site accidents.
While safety measures and equipment are provided, there’s always a risk of injury due to unforeseen events or mishaps.
This constant exposure to potential harm can also lead to stress and anxiety.
Therefore, it’s essential for these professionals to stay vigilant, comply with safety protocols, and wear appropriate protective gear at all times.
Unscheduled Overtime to Address Urgent Repairs or Breakdowns
Just like many other roles that demand immediate attention to emergencies, industrial maintenance mechanics may frequently encounter unscheduled overtime.
This could be a result of unexpected equipment failures, breakdowns, or urgent repair needs that cannot wait until the next business day.
The nature of this job requires them to be available round the clock, often leading to long, unpredictable hours.
These unscheduled overtime hours can interfere with personal time and plans, creating a work-life imbalance.
This irregularity in schedule might also lead to stress and exhaustion, affecting the overall health and well-being of the mechanic.
Requirement to Work in Uncomfortable Positions or Confined Spaces
Industrial Maintenance Mechanics are often required to work in uncomfortable positions or confined spaces.
This is because machinery and equipment can break down or require maintenance in hard-to-reach places.
Mechanics may need to crawl under machines, reach into tight spaces, or spend long periods in awkward postures to properly repair or maintain equipment.
This can lead to physical strain and discomfort, and over time, potentially cause injury or health issues.
Additionally, working in confined spaces may also increase the risk of accidents or injuries.
Therefore, it requires significant physical fitness, flexibility, and carefulness to perform this job role effectively.
Work Environment That May Be Noisy, Dirty, or Greasy
Industrial Maintenance Mechanics often work in environments that can be noisy, dirty, or greasy.
This is due to the nature of the machinery and equipment they are required to maintain and repair.
Working in such conditions can be physically demanding and uncomfortable.
Noise levels can be high which may require the use of protective gear such as earplugs.
The work may also involve exposure to oil, grease, and grime which can make the work environment slippery and dirty.
This not only requires regular cleaning of tools and equipment, but also may necessitate frequent changes of work clothes or uniforms.
While these conditions can be mitigated with the correct safety procedures and equipment, they can still present a significant challenge for some individuals.
Need for Continuous Education to Keep Up with Technological Advances
As technology continues to advance at a rapid pace, industrial maintenance mechanics must stay updated with the latest technological changes.
This means that there is a constant need for continuous education and training.
These individuals may have to attend regular training sessions, workshops, or take additional courses to keep their skills current.
In addition to their regular working hours, they may need to dedicate extra time for learning, which may be unpaid.
This can be both time-consuming and financially challenging, especially if the employer doesn’t offer compensation for this ongoing education.
Moreover, failure to keep up with the latest developments may result in outdated skills, potentially affecting job performance and security.
On-Call Responsibilities for Emergency Maintenance Issues
Industrial Maintenance Mechanics often have to be on-call for emergency maintenance issues.
This can mean that they are expected to be available outside of traditional working hours, including nights, weekends, and even holidays.
These professionals are often the first line of defense when a piece of machinery breaks down unexpectedly, and they must be ready to respond quickly to prevent further damage or downtime.
This can lead to unpredictability in their schedules and potentially extended hours of work.
These on-call responsibilities can also lead to increased stress, as these emergencies often need to be resolved as quickly as possible to minimize the impact on the company’s operations.
Stress from Ensuring Minimal Downtime of Machinery
Industrial Maintenance Mechanics are tasked with the job of making sure that factory machines and equipment are working efficiently with minimal downtime.
This is crucial in industries where production cannot afford to be halted for extended periods.
Due to this, the mechanic may face immense pressure to quickly identify problems, rectify them, and ensure the machinery is back up and running in the shortest possible time.
The stress from this responsibility can be compounded during peak production periods or when dealing with complex machinery.
The constant pressure to prevent and handle mechanical faults promptly can lead to high stress levels, which can have a negative impact on the mechanic’s well-being over time.
Limited Career Advancement Opportunities Without Additional Education
Industrial Maintenance Mechanics often face a ceiling in their career progression after a certain point, with very limited opportunities for advancement without further education or specialized training.
While entry-level positions may only require a high school diploma and on-the-job training, advancing to higher level or managerial positions often require additional qualifications such as a relevant associate’s or bachelor’s degree or a professional certification.
Without these additional qualifications, an Industrial Maintenance Mechanic may find themselves stuck in the same role for many years.
This can lead to stagnation and a lack of motivation, as the role may become monotonous and offer little challenge or opportunity for growth.
Wear and Tear on the Body Over Time, Leading to Potential Chronic Injuries
Industrial maintenance mechanics often perform physically demanding tasks that can take a toll on their bodies over time.
This job role often requires heavy lifting, bending, kneeling, and spending long hours on your feet.
Over time, this can lead to chronic injuries such as back problems, joint pain, and muscle strains.
These professionals are also at a higher risk of work-related accidents due to handling heavy machinery and equipment.
Although safety measures are taken, the risk cannot be entirely eliminated.
Therefore, the physical demands and potential for injury are significant disadvantages of this role.
Irregular Hours Including Weekends, Holidays, or Night Shifts
Industrial Maintenance Mechanics often do not have the luxury of a regular 9 to 5 job.
They may be required to work irregular hours including weekends, holidays, and night shifts.
This is because many industries operate around the clock and equipment may break down or require maintenance at any time.
As a result, mechanics might be on call or work in shifts to ensure that production is not halted due to equipment failure.
This can be challenging, as it can disrupt regular sleep patterns, interfere with social or family time, and lead to work-life imbalance.
Additionally, working at odd hours or during nights might require the mechanic to work under less optimal conditions, adding to the stress and difficulty of the job.
Balancing Multiple Tasks and Prioritizing Repairs Under Tight Deadlines
Industrial Maintenance Mechanics often have to juggle a variety of tasks at the same time.
From routine maintenance checks to sudden machinery breakdowns, they are expected to handle everything with equal efficiency.
The nature of this role often involves working under tight deadlines, which can be stressful.
They need to prioritize their tasks carefully and make quick decisions about which repairs or maintenance tasks are the most urgent.
This can be a challenging aspect of the job, particularly in larger industrial setups where there is a constant demand for their attention.
This continuous pressure to prioritize and complete tasks quickly can lead to longer working hours and can be mentally and physically taxing.
Occasional Lack of Recognition for Behind-the-Scenes Work
Industrial Maintenance Mechanics often work behind the scenes to ensure that machinery and equipment in an industrial setting are functioning properly.
This job role requires vast technical knowledge, problem-solving skills, and physical effort.
However, their work often goes unnoticed unless a machine breaks down.
Recognition for their preventative and routine maintenance, which keeps the machines running smoothly, is often overlooked.
This lack of recognition can lead to job dissatisfaction and a feeling of underappreciation, despite the crucial role they play in maintaining the productivity of the industry.
Need to Adhere to Strict Safety Regulations and Protocols
As an Industrial Maintenance Mechanic, one of the major disadvantages is the need to adhere to strict safety regulations and protocols at all times.
These procedures are designed to ensure the safety of workers and prevent accidents, however, they can be cumbersome and time-consuming.
The regulations may involve wearing protective gear, following specific procedures when using equipment, and complying with regular safety checks and inspections.
The slightest deviation from these protocols can lead to serious consequences, including accidents, injuries, and legal ramifications.
Hence, the role demands constant vigilance and adherence to safety protocols, adding stress and pressure to the job role.
Dealing With Older Equipment and Outdated Systems
Industrial Maintenance Mechanics often have to work with older equipment and outdated systems.
This can pose various challenges, including a higher chance of equipment failure and difficulty sourcing parts for repairs.
Older machines also tend to be less efficient and more difficult to operate, which can slow down production.
Additionally, these machines may not have modern safety features, which can put mechanics at a higher risk of injury.
Lastly, working with outdated systems can be frustrating for mechanics who are trained on more modern equipment and systems.
They may need to spend additional time learning how to operate and maintain these older systems, which can be a drain on their productivity.
Job Stability Affected by Changes in Industry and Economy
Industrial Maintenance Mechanics work in a field that is heavily influenced by fluctuations in the manufacturing industry and the broader economy.
This means that when the manufacturing sector is not performing well or when the economy is in a downturn, there may be layoffs or cuts in hours.
Even in times of economic stability, the rise of automation and other technological advancements in the industry could potentially lead to job losses or changes in job roles for Industrial Maintenance Mechanics.
Additionally, outsourcing of maintenance work to third-party companies or overseas can also impact job stability.
Despite these challenges, the need for maintenance in industrial settings will always exist, providing some level of job security.
Potential for Stressful Working Conditions During Plant Shutdowns
Industrial Maintenance Mechanics often have to work under high-stress conditions, especially during plant shutdowns.
These shutdowns may occur due to breakdowns, maintenance requirements, or safety inspections, and the mechanics are responsible for getting the plant up and running as quickly as possible.
This often means working under strict time constraints, which can result in long hours and high-pressure situations.
Mechanics may also have to work in challenging physical conditions, such as in tight spaces or in extreme temperatures.
The stress of these situations can be taxing, both physically and mentally, and can also increase the risk of accidents or mistakes if safety precautions are not rigorously followed.
Requirement to Maintain Certification and Licenses Relevant to the Role
Industrial maintenance mechanics are required to maintain and regularly update their certifications and licenses to stay relevant and legally operational in the field.
This often involves ongoing training and education, which can be time-consuming and potentially expensive.
They must stay updated with the latest machinery, safety protocols, and industry standards.
This continuous learning may mean dedicating time outside of work hours for training and studying for certification exams.
While this commitment to staying current in the industry can enhance their skills and job performance, it can also create additional pressure and demands on their time.
Necessity to Purchase Personal Tools for the Job
Industrial maintenance mechanics are often required to purchase their own personal tools for their job.
While some employers may provide basic tools, it is not uncommon for mechanics to invest in their own set of high-quality tools.
This can be a significant upfront cost, with many mechanics spending hundreds or even thousands of dollars on tools.
Additionally, these tools require ongoing maintenance and eventual replacement, adding to the overall expense.
While owning personal tools can provide a sense of autonomy and preparedness, the financial burden can be a significant disadvantage for many individuals in this role.
Reduced Job Options in Geographically Limited or Declining Industries
Industrial Maintenance Mechanics may face limited job opportunities in areas where industries are declining or geographically limited.
These professionals often work in manufacturing plants or factories, which can be concentrated in specific regions or cities.
If those industries begin to decline or relocate, it can significantly reduce the number of job openings for mechanics in those areas.
This can force these professionals to either relocate to areas with more job opportunities or switch careers.
Moreover, the ongoing automation in various industries could also contribute to fewer job opportunities for mechanics in the future.
Dependence on Physical Health and Stamina for Job Performance
Industrial Maintenance Mechanics are required to be physically fit and possess a high level of stamina to perform their daily tasks efficiently.
The job often involves heavy lifting, standing for long periods, bending, stretching and sometimes working in uncomfortable positions.
The work can be physically demanding and tiring, which could lead to physical strain and injuries if not careful.
As a result, they are heavily dependent on their physical health and stamina to maintain their job performance.
Moreover, a decline in physical health or an injury could negatively impact their ability to work, which may lead to job insecurity.
Therefore, regular exercise and maintaining a healthy lifestyle are crucial for an industrial maintenance mechanic.
Seasonal Fluctuations Leading to Periods of Overwork or Underemployment
Industrial Maintenance Mechanics often face seasonal fluctuations in demand for their services, which can lead to periods of intense overwork or underemployment.
During periods of high production or when machinery is more likely to break down, such as in the peak manufacturing seasons, maintenance mechanics might be required to work long hours, often in stressful and physically demanding conditions.
Conversely, during periods of low production or off-seasons, there may be less work available which can lead to periods of underemployment.
This inconsistent work schedule can make it hard for mechanics to plan their personal lives and finances.
The cyclical nature of the job can also lead to job insecurity during quieter periods.
Difficulty in Keeping Skills Relevant in an Increasingly Automated Industry
As the manufacturing industry becomes more automated, industrial maintenance mechanics may find it challenging to keep their skills relevant.
The rise of automation, robotics, and artificial intelligence means that many traditional mechanical tasks are now handled by machines.
This requires mechanics to continually update their skills to understand these advanced technologies.
They must undertake continuous training and development, which may be time-consuming and costly.
Additionally, the rapid pace of technological advancement can make it difficult to stay abreast of the latest techniques and tools.
This may lead to job insecurity if the mechanic is unable to adapt to new technologies.
The Psychological Impact of Maintaining High Levels of Alertness and Accuracy
Industrial maintenance mechanics are responsible for the upkeep and repair of complex machinery in a variety of industrial settings.
This role demands constant attention to detail and high levels of alertness, which can be psychologically exhausting over time.
They must be capable of detecting and addressing minor issues before they become major problems, which often requires a high degree of precision and accuracy.
The constant need for vigilance can lead to stress and burnout, particularly if the mechanic works in an environment with high production demands.
There is also the pressure of maintaining safety standards and minimizing downtime, which can further contribute to the psychological stress associated with this role.
Furthermore, any mistake or oversight could potentially lead to machine failure, affecting productivity and possibly posing safety risks.
This constant need for accuracy and focus can lead to mental fatigue and stress.
Financial Implications of Continuous Learning and Skill Enhancement
Industrial Maintenance Mechanics are required to continually update their knowledge and skills to keep up with technological advancements and changes in equipment.
This can lead to significant financial implications as they may need to pay for additional courses, certifications, or training programs.
Furthermore, the need for continuous learning often means spending personal time to study or attend courses.
This can also lead to fatigue and burnout.
Additionally, the rapid pace of technological change can also put pressure on mechanics to constantly adapt, leading to stress and job insecurity.
However, on the positive side, continuous learning can increase job security and opportunities for advancement.
Conclusion
And there you have it.
An unfiltered glimpse into the disadvantages of being an industrial maintenance mechanic.
It’s not just about wielding tools and greasy overalls.
It’s arduous labour. It’s dedication. It’s steering through a labyrinth of technical and mechanical challenges.
But it’s also about the satisfaction of fixing a malfunctioning machine.
The gratification of maintaining the pulse of an industry.
The exhilaration of knowing you played a part in keeping the wheels of production turning.
Yes, the path is demanding. But the rewards? They can be remarkable.
If you’re nodding along, thinking, “Yes, this is the challenge I’ve been yearning for,” we’ve got more insights for you.
Dive into our insider guide on the reasons to become an industrial maintenance mechanic.
If you’re ready to embrace both the victories and the hurdles…
To learn, to grow, and to prosper in this dynamic trade…
Then perhaps, just perhaps, a career as an industrial maintenance mechanic is calling you.
So, take the leap.
Explore, engage, and excel.
The world of industrial maintenance awaits.
Sick of the Rat Race? Try These Easy Jobs for a Change!
Extreme Stress Alert: The Most Overwhelming Jobs Out There!
Chasing Happiness: Enjoyable Careers That Keep You Excited