25 Disadvantages of Being an Installer (Ladder Leaning Lows!)
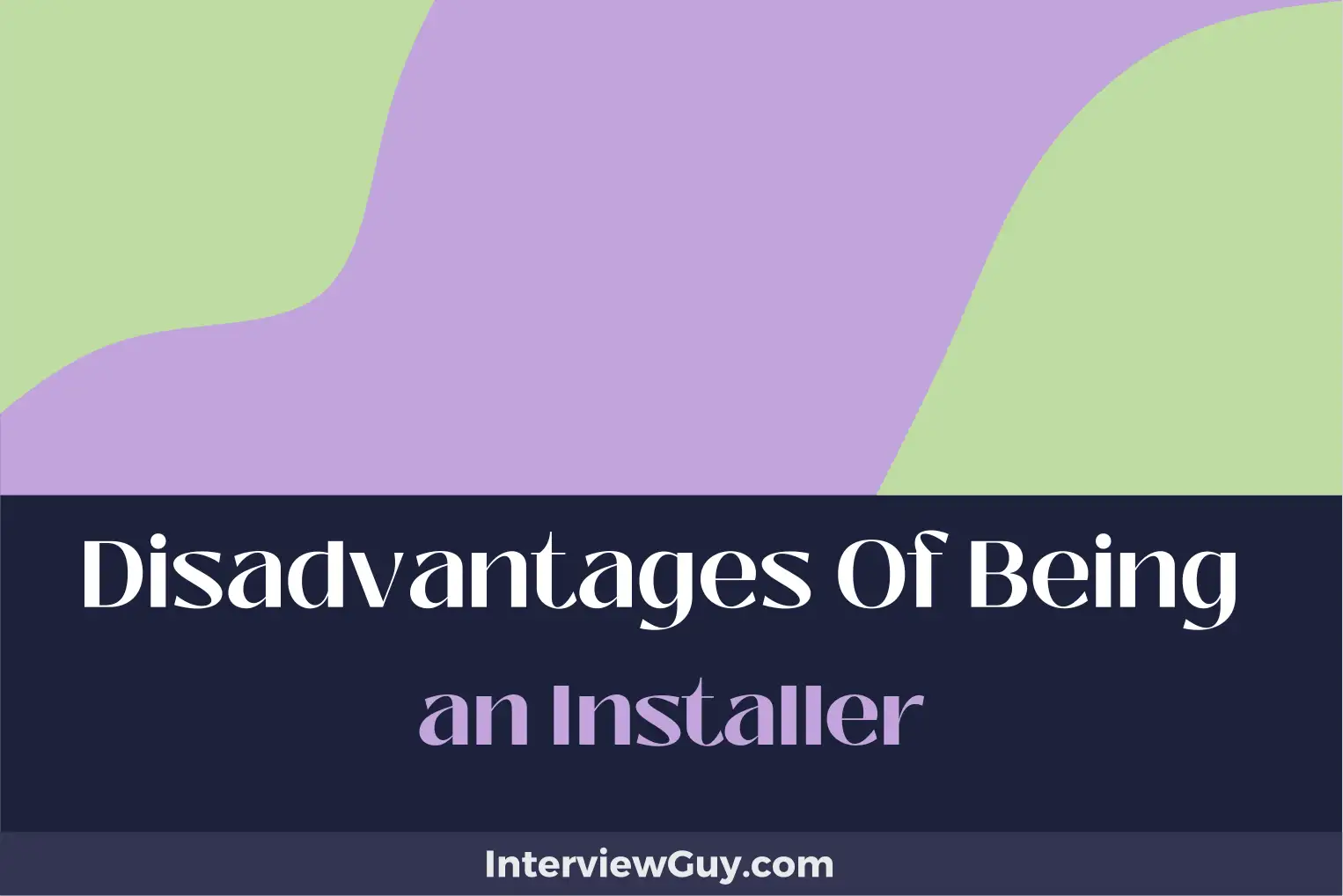
Considering a career as an installer?
It’s easy to get swept up in the appeal:
- Hands-on work.
- Potential for independent contracting.
- The satisfaction of seeing a project come to life.
But there’s more to the picture.
Today, we’re delving deep. Real deep.
Into the cumbersome, the disagreeable, and the downright challenging parts of being an installer.
Complex skill set required? Check.
Initial investment in tools and equipment? You bet.
Physical demands and long hours? Absolutely.
And let’s not overlook the unpredictability of project timelines and client expectations.
So, if you’re contemplating stepping into the world of installation, or just intrigued about the realities beyond the completed projects and satisfied customers…
Continue reading.
You’re about to get a comprehensive look at the disadvantages of being an installer.
Physical Strain From Manual Labor and Equipment Handling
Installers often work in a physically demanding environment.
The job involves a lot of manual labor such as lifting heavy equipment, climbing ladders, kneeling, bending, and working in tight spaces.
This constant physical strain can lead to fatigue, chronic pain, and potential injuries.
In addition, the handling of technical equipment requires precision and care, adding to the physical strain and stress of the role.
The conditions can be further exacerbated if the installer has to work in harsh weather conditions or in confined spaces.
Therefore, it’s crucial for installers to maintain a high level of physical fitness and take care of their health to prevent long-term damage.
Risk of Injuries Due to Work With Power Tools and Ladders
Installers work with a variety of tools and equipment, including power tools and ladders, which can be hazardous if not used properly.
They may be required to climb ladders or work in high, precarious places, which increases the risk of falls.
Moreover, power tools can be dangerous as well, as they can cause injuries if mishandled or if a malfunction occurs.
This means that installers need to be very cautious and observant while working to avoid any accidents.
Furthermore, this risk also necessitates that installers be physically fit and have good balance to safely handle the demands of their work.
Despite safety measures in place, the risk of injury is a significant disadvantage in the role of an installer.
Exposure to Outdoor Conditions and Adverse Weather
As an installer, you may often work outside or in locations that are not climate controlled.
This means that you may be exposed to a variety of outdoor conditions and adverse weather.
You could be working in extreme heat, cold, rain, snow, or even in stormy conditions.
This may not only be uncomfortable but can also be potentially dangerous.
Furthermore, working in such conditions could also slow down the work pace, causing delays in project completion.
It also means you need to be adequately prepared and equipped with the right clothing and safety gear to handle these situations.
Long and Irregular Working Hours to Meet Project Deadlines
Installers often face the challenge of long and irregular working hours, especially when there are tight project deadlines to meet.
This job role does not follow a standard 9 to 5 schedule, and often requires working extra hours, late into the night, or even during the weekends to ensure the project is completed on time.
This can interfere with personal life and social activities, as it may be difficult to plan around such an unpredictable schedule.
In some cases, installers may also have to work in difficult weather conditions or in remote locations, which could add to the challenges of the job.
Despite these challenges, the satisfaction of successfully installing and completing a project can be rewarding.
Need to Frequently Travel to Different Job Sites
Installers are often required to travel frequently to different job sites.
This could involve local travel within a city or region, or sometimes even longer distances, depending on the scope of the work.
While this can provide a change of scenery and keep the job interesting, it can also be tiring and time-consuming.
The need to travel frequently can also make it more difficult to maintain a regular schedule or work-life balance.
In addition, the wear and tear on personal vehicles or the requirement to operate company vehicles can add additional stress.
Lastly, frequent travel may limit personal time and can lead to increased expenses such as fuel and vehicle maintenance costs.
Requirement to Keep Skills Updated With New Installation Technologies
Installers are expected to stay up-to-date with the latest installation technologies and techniques.
This means that they must constantly learn and adapt to new methodologies, which can be time-consuming and requires a commitment to continuous learning.
It can also add to the pressure of the job role as failing to keep up with the latest trends and technologies might put them at a competitive disadvantage.
This often requires additional training and certification courses, which may not always be paid for by the employer.
It also means that installers need to be proactive in their professional development, which could be challenging if they have other commitments or a heavy workload.
Adhering to Stringent Safety Regulations and Standards
Installers are required to strictly follow safety regulations and standards set by different governing bodies.
These can include rules related to work procedures, use of tools and equipment, and preventive measures.
The constant need to adhere to these regulations can be challenging, especially when they are frequently updated or changed.
Additionally, some of these safety regulations can slow down work processes or increase the complexity of tasks.
Non-compliance can lead to serious consequences such as hefty fines, loss of license, or even closure of business.
Hence, it is essential for installers to keep themselves updated with the latest safety standards and regulations.
This constant need to stay updated and adhere to safety regulations can add stress and pressure to the role.
Potential for Re-work Due to Client Satisfaction Issues
As an installer, you are often the final touchpoint for the client in the service or product delivery process.
Hence, there is a high probability that you will have to revisit installations due to client satisfaction issues.
This could arise from a variety of factors such as miscommunication about the installation, faulty products, or the client simply being unhappy with the final result.
This means you may have to redo the work, sometimes at no additional cost, which can be time-consuming and also affect your productivity.
It can also lead to increased travel, longer hours, and frustration if the client’s expectations are not clearly defined or met.
Varying Pay Based on Contracts and Seasonal Work Demand
Installers often face a fluctuating income as their pay is generally based on the number and type of contracts they secure.
This means that an installer’s income may vary greatly from month to month, depending on the demand for their services.
In addition, many installers are subject to the seasonal nature of their work.
For example, those who install heating systems may find that their services are in high demand during the colder months, but less so during the warmer months.
This fluctuation in work demand can make it difficult for installers to manage their finances and ensure a steady income throughout the year.
Managing Customer Expectations and On-Site Changes
Installers are often faced with the challenge of managing customer expectations.
Customers may have a vision of how they want an installation to appear or function, but these expectations may not always be realistic or feasible.
Additionally, installers may encounter unexpected on-site changes that are beyond their control.
For example, they might arrive at a site to find that the space where an installation is to occur is not as it was described, or that there are unexpected obstacles that weren’t accounted for.
Such changes can lead to delays, increased costs, and customer dissatisfaction.
Therefore, installers need to be adept at communication and problem-solving to manage these situations effectively.
Pressure to Complete Installations Quickly and Efficiently
Installers often face the challenge of having to complete their work within a strict timeframe.
This is due to the fact that any delays can affect the operation of the business or household where they are installing equipment or systems.
This pressure to finish the job quickly can lead to stress, especially when working on complex installations.
Additionally, installers are expected to maintain high standards of work even under time constraints, as improper installations can lead to malfunctions and the need for re-installation.
Consequently, this can lead to long work hours, and in some cases, working during holidays or weekends to meet deadlines.
Dealing With Unforeseen Installation Challenges and Delays
Installers, whether they’re working on electronics, home appliances, or other types of machinery, often encounter unexpected issues during the installation process.
These problems can range from incorrect measurements, missing or faulty equipment, and unforeseen structural obstacles, to unexpected technical issues.
These challenges not only slow down the installation process, but they may also require the installer to acquire new skills or knowledge on the spot.
Furthermore, delays and unexpected problems can lead to longer work hours, customer dissatisfaction, and increased stress.
The unpredictability of the job can make it difficult to balance work and personal life, as the installer may often need to work overtime to meet deadlines and keep projects on track.
Competition With Other Installation Companies and Contractors
Installers often face stiff competition from numerous other installation companies and independent contractors.
This can be particularly challenging for small businesses or independent installers who must compete against larger companies with more resources.
Larger companies are often able to offer lower prices due to their ability to buy materials in bulk and employ a larger workforce.
Additionally, these companies may have established client bases and strong reputations, making it difficult for newer or smaller competitors to break into the market.
This competition can lead to price wars, reduced profits, and stress to secure enough work to make a living.
Requirement for Continuous Education on Building Codes and Regulations
Installers, such as those in the fields of electricity, HVAC, plumbing, etc., are required to stay updated on changing building codes and regulations.
These codes and regulations can change frequently as new safety protocols or technologies are introduced.
Installers must consistently stay on top of these changes to ensure their work is compliant, which can mean attending training sessions, reading updated manuals, or completing additional certifications.
This continuous education can take up a significant amount of time and may sometimes come at a personal cost.
Furthermore, failing to stay updated can result in penalties, fines or even job loss.
Thus, the requirement for continuous learning and updating can be a major disadvantage for those seeking a straightforward job role.
Financial Responsibility for Tools and Work Equipment
Installers often bear the financial responsibility for their own tools and work equipment.
This means that the cost of buying, replacing, and maintaining tools, such as drills, measuring devices, and specialized equipment, comes out of their own pockets.
In addition to the initial investment in quality tools, there’s also the ongoing cost of repairs and replacements, which can quickly add up.
These costs can be especially burdensome for new installers who are just starting out in their careers.
While some employers may provide some tools, the bulk of the responsibility usually lies with the installer.
This financial burden can be a significant disadvantage, especially when compared to other jobs where the employer provides all necessary equipment and tools.
Risk of Damage or Mistakes During Installation Process
Installers are often tasked with setting up complex systems or equipment, whether it’s installing appliances, software, machinery, or other items.
This role comes with the inherent risk of damaging the product during the installation process.
Mistakes can happen for a variety of reasons, such as misunderstanding instructions, using incorrect tools, or encountering unexpected issues.
These errors can lead to costly repairs, delays, or even replacement of the product.
In worst-case scenarios, mistakes can also lead to injuries.
Hence, installers must always pay close attention to detail and follow safety guidelines to minimize these risks.
However, even with the utmost care, the risk of damage or mistakes is a constant pressure in this role.
Ensuring Quality Control and Compliance With Industry Standards
Installers are tasked with the responsibility of ensuring that the products they install meet industry standards and quality requirements.
This is a critical aspect of the job as any mistakes can lead to product malfunction or safety hazards.
Therefore, they must have an in-depth understanding of product specifications, installation guidelines, and safety protocols.
Additionally, they are often required to inspect their work to ensure that everything has been installed correctly, which can be time-consuming and stressful.
If a problem is discovered after the installation, the installer may be held accountable, which can lead to job dissatisfaction and stress.
Furthermore, installers may face challenges in managing their time effectively, as they must balance the need for speed with the need for accuracy and thoroughness.
Job Security Dependent on Construction and Housing Market Trends
Installers, like many in the construction industry, may find that their job security is highly dependent on the trends of the construction and housing markets.
During periods of economic growth or housing booms, there may be an increased demand for skilled installers which can lead to more job opportunities and higher wages.
However, during economic downturns or periods of stagnation in the housing market, the demand for installers can significantly decrease.
This can lead to layoffs, reduced hours, or wage decreases for installers.
While some installers may be able to pivot to related roles or industries, these economic fluctuations can result in periods of unemployment or financial instability.
Limited Career Progression Without Additional Certifications or Education
Installers often find their career progression limited unless they acquire additional certifications or continue their education in their specific field.
Many installation roles require specific technical skills and knowledge, but once these are mastered, there can be few opportunities for advancement without expanding one’s skillset.
Installers may need to pursue certifications, such as those offered by the National Institute for Certification in Engineering Technologies, to become a senior technician or supervisor.
This could mean investing in further training or education outside of work hours, which may require both time and financial commitment.
Without these additional qualifications, an installer may find themselves stuck in the same role for many years.
Installers often have to navigate through complex bidding processes to secure new contracts.
This may require thorough understanding of the specifications and requirements of the project, meticulous preparation of documents, and strategic pricing.
The competition in bidding can be fierce, and it’s not always the lowest bid that wins.
Other factors such as experience, reputation, and ability to deliver within the stipulated time frame are also considered.
Additionally, the bidding process can be time-consuming and there’s always a risk of not winning the contract, despite the considerable effort invested.
Losing a bid can mean financial loss and missed business opportunities.
This aspect of the job can be stressful and requires a lot of patience and resilience.
Balance Between Detail-Oriented Work and Productivity Targets
Installers often face the challenging balance between delivering meticulous, high-quality work and meeting productivity targets.
Each installation job requires a great deal of attention to detail to ensure that the installation is done correctly, safely, and meets the client’s expectations.
However, installers are also often under pressure to complete a certain number of installations within a specified timeframe.
This can lead to stress and burnout, as trying to maintain high-quality work while also trying to meet productivity targets can be challenging.
This aspect of the job can also potentially lead to rushed work or overlooked details, which can ultimately affect the quality of the installation.
Personal Liability for Accidents or Installation Failures
Installers are often personally responsible for any accidents or failures that occur during the installation process.
This could include anything from damaging a client’s property during installation, to a product not working properly after being installed.
This risk of liability means that installers need to be extremely careful and precise in their work, and also often necessitates the need for liability insurance.
Moreover, if an accident does happen, it could result in financial losses or even legal issues.
This pressure and personal responsibility could potentially lead to stress and anxiety in this job role.
Administrative Work Including Job Quoting and Invoicing
Despite being a hands-on role, being an Installer also requires a significant amount of administrative work.
This includes creating and sending out quotes for new jobs, managing invoices for completed projects, and keeping track of expenses.
This paperwork can be time-consuming and takes away from the time spent on actual installations.
Additionally, if not done accurately, it can lead to financial discrepancies, incorrect pricing, and potential disputes with clients.
Therefore, an installer must possess not only technical skills, but also administrative and financial management skills.
Keeping Up With Environmental Regulations for Sustainable Installations
Installers, particularly those working in sectors like HVAC or energy, often have to stay updated with ever-changing environmental regulations.
These could include local, state, or even federal guidelines intended to promote sustainable installations.
This requirement can be time-consuming and requires constant learning and adaptation.
Moreover, failure to comply with these regulations can result in significant penalties, legal issues, or reputational damage for the installer or their company.
It also adds an extra layer of complexity to the job, as installers must ensure that their work adheres to these standards while also meeting the specifications and expectations of their customers.
Dependence on Vendor Timelines for Supply of Installation Materials
Installers are often dependent on vendors for the supply of installation materials.
A delay in the supply chain can drastically affect the installer’s work schedule and overall project timeline.
They often have to adjust their work schedules to accommodate these delays, which can lead to increased work hours and stress.
There are also situations where the materials delivered may not meet the quality standards or specifications, requiring additional time for returns and replacements.
This dependence on vendors for materials can add an element of unpredictability to the installer’s job, making it challenging to adhere to project timelines and maintain client satisfaction.
Conclusion
And there you have it.
An unfiltered exploration of the disadvantages of being an installer.
It’s not just about knowing how to use a toolset and understanding blueprints.
It’s labour-intensive. It’s commitment. It’s navigating a labyrinth of practical and logistical challenges.
But it’s also about the gratification of completing an installation.
The satisfaction of seeing a client appreciate a well-done job.
The exhilaration of knowing you played a role in shaping someone’s space.
Yes, the path is strenuous. But the rewards? They can be remarkable.
If you’re nodding along, thinking, “Yes, this is the challenge I’ve been craving,” we’ve got something more for you.
Dive into our comprehensive guide on the reasons to become an installer.
If you’re ready to tackle both the peaks and the valleys…
To learn, to evolve, and to flourish in this hands-on field…
Then maybe, just maybe, a career as an installer is for you.
So, take the leap.
Investigate, involve, and improve.
The world of installation awaits.
The Mount Olympus of Careers: Most Prestigious Jobs to Conquer
Confronting Chaos: What the Most Stressful Jobs Teach Us About Resilience!
Stress-Free Success: Easy Jobs That Pay More Than You’d Guess!
Career Caution: These Jobs Might Not Meet Your Financial Expectations