How to Become a Field Service Calibration Technician (Dial in on Details!)
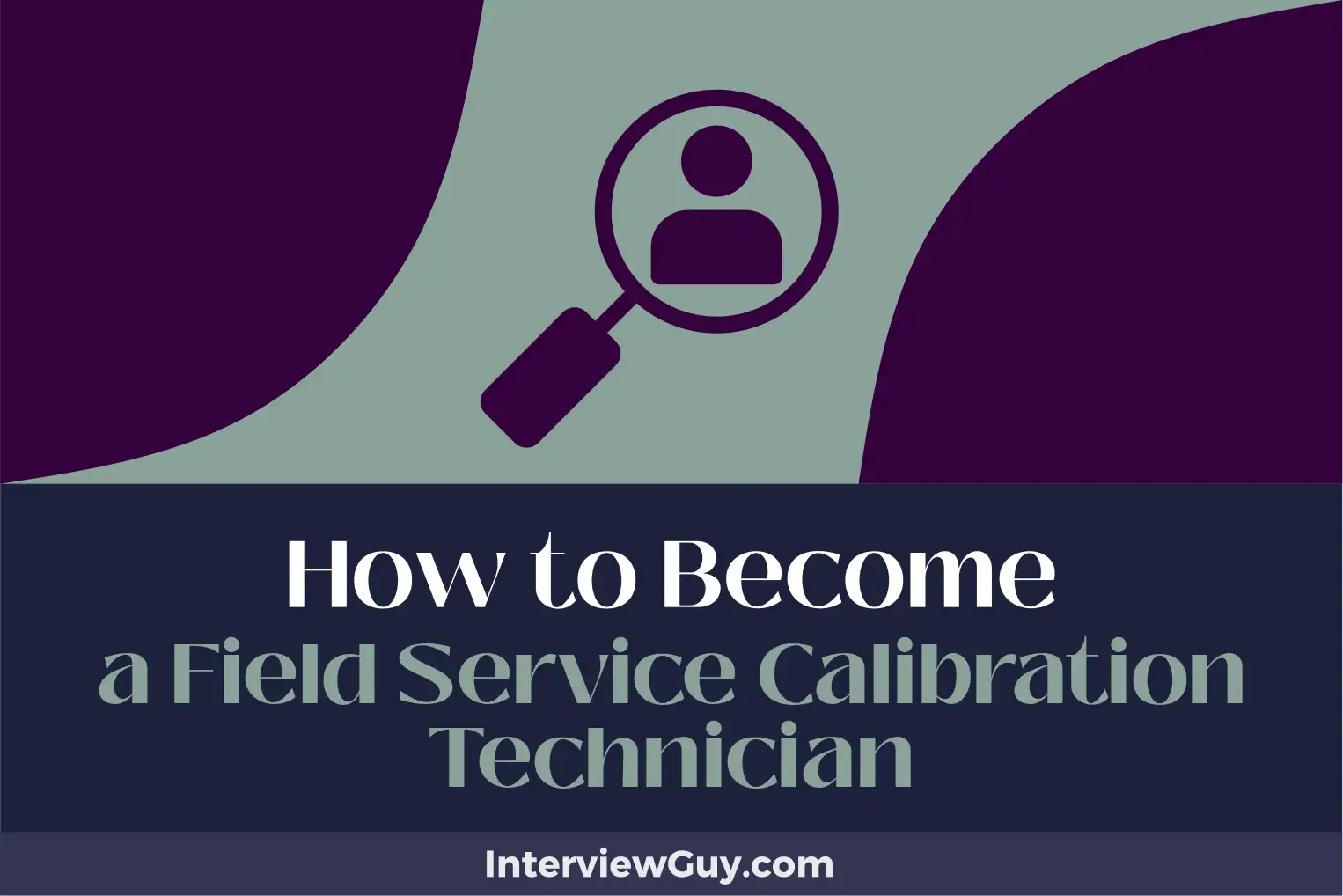
If you’ve ever envisioned yourself working in the dynamic field of calibration technology or wondered what it takes to become a Field Service Calibration Technician, you’re in the right place.
In this guide, we’ll outline the SPECIFIC steps you need to take to kick-start your career as a Field Service Calibration Technician. We’ll discuss:
- The technical and soft skills required.
- The education and certifications that can boost your employability.
- Tips for landing a job in this field.
So, whether you’re a novice looking to enter the technical field or an experienced professional aiming to diversify your skills, stay tuned.
We’re about to decode the path to becoming a Field Service Calibration Technician.
Let’s dive in!
Steps to Become a Field Service Calibration Technician
Step 1: Gain Basic Education
The first step to becoming a Field Service Calibration Technician is to gain a basic education, ideally a high school diploma or equivalent.
In high school, it is beneficial to focus on math and science courses, particularly physics, as these provide a solid foundation for understanding the principles of calibration.
Step 2: Obtain Technical Training
After your basic education, it is recommended to obtain technical training, which can be achieved through vocational schools or community colleges.
Look for programs that offer courses in electronics, instrumentation, or calibration technology.
These programs will provide a deeper understanding of measuring instruments and calibration techniques.
Step 3: Gain Hands-On Experience
On-the-job training is an essential part of becoming a Field Service Calibration Technician.
Hands-on experience allows you to apply what you’ve learned in a practical setting, and understand the intricacies of different calibration instruments.
Many start in entry-level positions that provide training under the supervision of experienced technicians.
Step 4: Obtain Certification
Although not always required, obtaining a certification can make you more attractive to potential employers.
Organizations such as the International Society of Automation offer certification programs for calibration technicians.
Before taking the certification exam, you may need a certain amount of work experience.
Step 5: Continue Professional Development
The field of calibration technology is constantly evolving, so it’s important to stay up-to-date with the latest techniques and technologies.
This can be achieved through continuous professional development, which can involve attending industry seminars, workshops, or additional courses.
Being up-to-date not only improves your skills but also makes you more attractive to potential employers.
Step 2: Understand the Role of a Field Service Calibration Technician
A Field Service Calibration Technician is responsible for the calibration, testing, and repair of various instruments and equipment.
This role typically involves traveling to different locations to perform maintenance and repair services on equipment, ensuring that all instruments are functioning within the specified parameters and standards.
As a Field Service Calibration Technician, you will need to have a strong understanding of measurement science, quality assurance, and the use of precision tools and equipment.
You also need to be familiar with industry-specific regulations and guidelines for equipment calibration.
Get to know the specific tasks involved in the job role, such as planning and coordinating calibration activities, interpreting blueprints and schematics, recording and evaluating data, and communicating with customers about equipment status and performance.
Understanding the role also entails getting to know the different environments you might work in as a Field Service Calibration Technician, including laboratories, manufacturing facilities, and field service environments.
Familiarize yourself with the safety procedures and protocols specific to each working environment.
This role requires good problem-solving skills, attention to detail, and the ability to work independently.
If you feel that this role aligns with your career aspirations and skill sets, you can move on to the next step which is obtaining the necessary qualifications and certifications.
Step 3: Attend Vocational Training or Obtain an Associate’s Degree in Calibration, Electronic Technology or Related Field
The journey to becoming a Field Service Calibration Technician often involves obtaining specific education in calibration or electronic technology.
One pathway is through vocational training programs which offer specialized courses focused on practical, job-specific skills.
These programs provide hands-on training and experience with calibration and electronic equipment, teaching you how to use, maintain, troubleshoot, and calibrate various instruments.
Alternatively, you may choose to pursue an Associate’s degree in calibration or electronic technology.
This course of study not only provides a deep understanding of the technical concepts and tools involved in calibration, but also includes general education subjects to broaden your knowledge base.
An Associate’s degree typically takes two years to complete and provides a more comprehensive education than a vocational program.
Whichever route you choose, ensure the program is accredited and recognized within the industry.
Once you have completed your education, you will have a solid foundation of theoretical knowledge and practical skills, preparing you for the next step in your career as a Field Service Calibration Technician.
Remember, this field is ever-evolving with new technology and standards.
Therefore, continuous learning and staying updated with the latest trends and advancements is crucial for your career growth and success.
Step 4: Gain Hands-On Experience Through Internship or Entry-Level Positions
Gaining practical experience is a crucial step in becoming a Field Service Calibration Technician.
This can be achieved through internships or entry-level positions in the field.
During this phase, you will have the opportunity to apply the theoretical knowledge you have gained from your studies into real-world scenarios.
Internships provide a platform for you to learn from experienced technicians, understand the daily responsibilities and workflows, and get exposed to different types of equipment and calibration procedures.
You can look for internship opportunities in companies that specialize in calibration services or in industries that heavily rely on calibrated equipment like manufacturing, aviation, and healthcare.
Another path is to start in an entry-level position, such as a calibration assistant or technician apprentice.
These roles often involve tasks such as assisting senior technicians, maintaining calibration records, and learning to use calibration software.
Regardless of the path you choose, the goal is to gain practical skills in calibrating, testing and repairing measurement and control instruments.
This hands-on experience is invaluable and will not only make you more attractive to future employers but also provide a solid foundation for your career as a Field Service Calibration Technician.
Make sure to use this time to also improve your problem-solving, communication, and technical skills.
Step 5: Obtain Certification from the National Institute for Certification in Engineering Technologies or a Similar Body
As a Field Service Calibration Technician, obtaining a certification from a recognized institution, such as the National Institute for Certification in Engineering Technologies (NICET), can greatly enhance your credibility and marketability in the field.
This certification will not only provide proof of your technical knowledge and skills, but also demonstrate your commitment to the profession and adherence to industry standards.
The certification process typically involves a combination of education, work experience, and passing an examination.
Depending on the organization, there may be various levels of certification, with each level requiring more experience and more advanced skill sets.
For instance, NICET offers four levels of certification in the field of engineering technology, with Level IV being the highest.
Before you can take the certification exam, you may need to meet certain prerequisites, such as a certain amount of work experience or a relevant degree.
When you feel ready, you can register for the exam, which typically covers topics like calibration standards, calibration procedures, measurement uncertainty, and instrumentation.
Once you pass the certification exam, you will need to maintain your certification by participating in continuing education and keeping up with changes in the field.
This might involve attending workshops, webinars, or conferences, or taking additional courses in calibration technology.
Remember, being a certified technician can make you more competitive in the job market and may lead to better job opportunities and higher salaries.
Therefore, this step is crucial in your journey to becoming a successful Field Service Calibration Technician.
Step 6: Develop Knowledge of Electronic, Mechanical, and Electromechanical Systems
To excel as a Field Service Calibration Technician, you need a strong understanding of electronic, mechanical, and electromechanical systems.
This knowledge is vital because you’ll be working on equipment and systems that involve these components.
In-depth knowledge of electronic systems involves understanding of circuit boards, processors, chips, electronic equipment, and computer hardware and software, including applications and programming.
Mechanical knowledge, on the other hand, involves understanding machines and tools, including their designs, uses, repair, and maintenance.
Knowledge of electromechanical systems combines these two, understanding how mechanical components and electronic systems interact and work together.
This can be crucial in troubleshooting and repairing complex devices and systems.
To gain this knowledge, you can take additional coursework or training in electronics, mechanics, and electromechanics.
Many technical colleges offer courses or programs in these fields.
You could also find on-the-job training opportunities that can help you develop practical experience and skills in these areas.
Additionally, staying updated with the latest technology trends and advancements in these fields can help you excel in your role.
You can do this by reading technical publications, attending seminars, workshops, or webinars, or joining professional organizations.
Remember, in this role, you will not only need to understand these systems but also be able to use this knowledge to calibrate, repair, and maintain equipment and devices.
Your ability to apply theoretical knowledge in practical situations will make you a successful Field Service Calibration Technician.
Step 7: Gain Familiarity with Calibration Standards and Equipment
In your pursuit to become a Field Service Calibration Technician, it’s crucial that you gain a solid understanding of various calibration standards and equipment.
These standards are set by regulatory bodies to ensure accuracy and consistency in the calibration process.
They dictate how equipment should be calibrated and provide procedures for performing calibrations.
As you dive into this field, spend time learning about different types of calibration equipment, including pressure calibrators, temperature calibrators, electrical calibrators, and RF calibrators.
Get to know their uses, how to operate them, and how to troubleshoot common issues.
You should also familiarize yourself with the guidelines set by the International Organization for Standardization (ISO), especially ISO 9000 and ISO 17025, which are specifically relevant to calibration laboratories.
Understanding these standards and devices will not only make you a more effective calibration technician but also increase your chances of landing a job as employers prefer candidates who can hit the ground running.
Many companies provide on-the-job training, but having prior knowledge will give you an edge and speed up your learning curve.
It’s also worth noting that advancements in calibration technology are constant, so maintaining a commitment to lifelong learning and staying updated with the latest technologies and standards will ensure your continued relevance in the field.
Step 8: Work on Problem-Solving and Communication Skills
As a Field Service Calibration Technician, you would be dealing with complex equipment and systems that need accurate calibration.
Hence, strong problem-solving skills are a necessity.
Start by improving your deductive reasoning and critical thinking capabilities.
You can do this by taking part in workshops, online courses, or problem-solving games that stimulate your mind to think logically and systematically.
Moreover, since this role often involves working with a team or communicating with clients, effective communication skills are crucial.
You might need to translate complex technical language into layman’s terms for clients or work in collaboration with a team where clear communication will help in performing the tasks more efficiently.
Consider joining public speaking clubs, or taking communication classes to boost your confidence and improve your ability to explain complex ideas simply.
Similarly, working on your written communication skills can also be beneficial, as you may need to write reports or guidelines about the calibrations you’ve performed.
As you progress in your career, continually enhancing these skills will make you a more effective and efficient Field Service Calibration Technician.
Step 9: Stay Updated with Technological Advancements and New Calibration Techniques
As a Field Service Calibration Technician, the importance of keeping up with the latest developments and techniques in the industry cannot be overemphasized.
Regularly updating your knowledge on the latest technologies, tools and calibration techniques helps you stay competitive and proficient in your role.
These updates can come in the form of new methods for calibrating equipment, new regulations related to calibration practices, or advancements in the technology used in calibration.
Such knowledge is crucial in enabling you to properly calibrate, maintain and troubleshoot the various devices that you may encounter in your line of work.
You can stay updated in several ways.
Attend workshops, seminars, and training programs that focus on the latest calibration techniques.
Subscribe to relevant journals, newsletters, or online platforms that provide updates on industry trends and advancements.
You can also join professional networks and forums where experts in the field share insights and discuss the latest developments in calibration.
Remember, the goal is not just to learn new things but to implement them in your work.
After all, the ultimate aim of staying updated is to improve the quality of your service, enhance your skills, and increase your value as a calibration technician.
Step 10: Apply for Positions as a Field Service Calibration Technician
After acquiring the necessary knowledge, skills, and certifications, you are ready to apply for positions as a Field Service Calibration Technician.
Start by researching job opportunities in various industries such as manufacturing, healthcare, automotive, and aerospace.
Look for positions that match your skill set and interest.
Prepare a resume and cover letter highlighting your skills, experiences, and certifications related to calibration and field service.
Make sure to tailor your application to match the requirements of each job posting.
Mention any practical experience you have had, including internships and apprenticeships.
Highlight your ability to troubleshoot, repair, and calibrate equipment, as well as any special knowledge or expertise you have in specific tools or methodologies.
Also, emphasize your ability to work independently, as field service roles often require technicians to work on their own in various locations.
Consider using online job search engines, industry job boards, and professional networks to find job openings.
Don’t forget to leverage your network – reach out to former classmates, instructors, or other professionals you have met in the field.
They may be aware of job opportunities or may be able to introduce you to potential employers.
Once you secure interviews, prepare by reviewing common interview questions for calibration technicians, and practice explaining complex technical concepts in a way that is easy for non-technical people to understand, as this is a skill often required in this role.
Also, be ready to discuss specific experiences where you successfully calibrated and repaired equipment.
Finally, remember that the job search can take time, so don’t get discouraged if you don’t land a job immediately.
Keep building your skills and gaining more experience, and keep applying.
With persistence, you can achieve your goal of becoming a Field Service Calibration Technician.
Step 11: Continuously Develop and Expand Your Skills and Knowledge.
As a Field Service Calibration Technician, your role will continually evolve as new technologies and processes are introduced to the industry.
Therefore, it’s essential to commit to lifelong learning and skill improvement to stay up-to-date with the latest trends and best practices.
Participate in ongoing training programs offered by your employer or through professional associations.
These may include workshops, seminars, webinars, or certification courses.
Also, consider attending industry conferences to network with other professionals and learn about new developments in the field.
Staying informed about the latest advancements in measurement and calibration technology is critical.
Subscribe to industry publications, join relevant online forums, and follow influential figures in the field on social media.
Moreover, consider mastering related skills like data analysis and report generation, which can make you a more versatile technician.
Also, improving your customer service and communication skills can provide a competitive edge as these are vital when interacting with clients.
In this ever-evolving field, the technicians who continuously learn and adapt are the ones who progress and succeed.
So, invest time in expanding your knowledge and skills to stay at the forefront of your profession.
Field Service Calibration Technician Roles and Responsibilities
Field Service Calibration Technicians are responsible for providing technical services related to the calibration of equipment and tools.
They work to ensure these instruments meet necessary standards for accuracy and reliability.
They have the following roles and responsibilities:
Calibration
- Perform calibration of various types of equipment and tools.
- Ensure calibration standards are strictly adhered to.
- Verify and validate procedures related to calibration.
Equipment Maintenance
- Maintain, repair, and troubleshoot calibration equipment and systems.
- Ensure equipment is in good working condition and safe to use.
Documentation
- Create and maintain accurate records of calibration checks, equipment conditions, and quality control measures.
- Prepare calibration certificates and reports for clients.
Customer Service
- Provide exceptional service to clients, ensuring their calibration needs are met.
- Explain technical details to clients in a clear and understandable manner.
Quality Assurance
- Perform quality control checks on calibrations.
- Ensure all calibration activities comply with regulatory standards and company policies.
Field Work
- Travel to client locations to perform on-site calibrations.
- Handle emergencies and urgent calibration needs at client sites.
Equipment Testing
- Conduct tests on new equipment to ensure it performs accurately.
- Perform safety tests on equipment.
Training
- Train other technicians and clients on proper calibration techniques and procedures.
- Stay updated with new calibration technology and techniques.
Inventory Management
- Manage the inventory of calibration tools and equipment.
- Order new equipment and tools as needed.
Continuous Learning
- Keep up-to-date with industry standards and trends related to calibration.
- Attend workshops, conferences, and training programs to improve skills and knowledge.
Communication
- Effectively communicate with clients and team members regarding calibration tasks.
- Report any issues or concerns to management promptly.
Health and Safety
- Follow all health and safety regulations when performing calibration tasks.
- Ensure safe handling of equipment and tools.
What Does a Field Service Calibration Technician Do?
Field Service Calibration Technicians typically work for manufacturing industries, laboratories or calibration service companies, and they may also work as self-employed individuals or contractors.
Their primary role is to ensure that the measuring instruments used in various industries are accurately calibrated.
They perform routine checks and calibration of instruments to ensure they are functioning correctly and providing accurate measurements.
These instruments can range from pressure gauges, thermometers, weight scales, to complex electronic measuring devices.
They are also responsible for diagnosing problems and performing necessary repairs on the instruments.
They use specialized calibration equipment and software for this purpose.
Once the calibration is done, they compare the results to the predefined standards to ensure the instrument’s accuracy.
Field Service Calibration Technicians often provide technical support to their customers.
They answer customer queries about the instruments, guide them on proper usage, and provide advice on maintenance and troubleshooting.
In some cases, they may also be involved in the design and development of new calibration procedures and protocols, ensuring they adhere to industry standards and regulations.
Their job requires them to meticulously document their work, including details of the calibration process, any issues detected, and the actions taken to rectify those issues.
This is crucial for quality assurance purposes and for maintaining a record of the instrument’s history.
Overall, they play a crucial role in ensuring the accuracy and reliability of measurements in various industries, which is essential for maintaining quality and safety standards.
Essential Field Service Calibration Technician Skills
- Technical Understanding: A strong grasp of calibration principles and the ability to understand technical specifications are crucial. This includes knowledge of electrical, mechanical, and dimensional measurement systems.
- Equipment Handling: Technicians need to be proficient in operating and maintaining a wide range of calibration equipment, tools, and software systems.
- Problem-Solving: Field Service Calibration Technicians regularly troubleshoot equipment issues and come up with solutions. The ability to think critically and solve problems is essential.
- Attention to Detail: Meticulous attention to detail is required in calibration to ensure the accuracy of measurements and functionality of equipment.
- Communication: Excellent communication skills are necessary to explain complex technical issues clearly to customers and provide comprehensive service reports.
- Documentation: Keeping accurate records of calibration checks, equipment faults, and customer information is a critical part of the job.
- Physical Stamina: The role often involves working in field conditions, which could require long hours standing, bending, lifting heavy equipment, and other physical tasks.
- Customer Service: Providing excellent customer service, including understanding customer needs, resolving issues, and ensuring satisfaction, is key to the role.
- Time Management: Field Service Calibration Technicians often have to manage multiple jobs in different locations. Excellent time management skills are essential to meet deadlines and manage tasks efficiently.
- Teamwork: Technicians often work as part of a team. Being able to collaborate effectively, share knowledge, and work towards a common goal is essential.
- Compliance: Knowledge and adherence to quality standards and safety regulations are necessary in this role, including ISO 17025 and ANSI/NCSL Z540.1.
- Computer Literacy: As many calibration tools are software-based, basic computer skills are required. This may include working with software for recording and analyzing data, reporting, and managing service schedules.
- Driver’s License: Technicians often travel to various job sites, so a valid driver’s license is typically required.
- Continuous Learning: The technology and standards in calibration are constantly evolving. The ability to learn and stay updated with the latest developments is crucial.
- Decision Making: Technicians need to make decisions on the spot, such as determining if equipment can be fixed or if it needs to be replaced. Good judgment and decision-making skills are therefore important.
Field Service Calibration Technician Career Path Progression
The Foundation: Calibration Technician Assistant
Starting as a Calibration Technician Assistant, you will be learning the ropes of calibration and testing.
Your main responsibilities will involve assisting senior technicians, performing basic calibration, and learning about different test equipment.
Here are some success tips for this role:
- Learning: Constantly learn about different calibration procedures, test equipment, and industry standards.
- Hands-on experience: Utilize every opportunity to gain hands-on experience with different types of equipment.
- Attention to Detail: Be meticulous in your work, as accuracy is essential in calibration tasks.
The Ascent: Field Service Calibration Technician
With experience and increased expertise, you will step into the role of a Field Service Calibration Technician.
Here, you will independently handle complex calibration tasks, provide customer support, and possibly travel to client sites.
To thrive in this stage:
- Problem-Solving: Develop your problem-solving skills to troubleshoot and fix issues during calibration.
- Customer Service: Improve your customer service skills as you’ll be directly interacting with clients.
- Quality Control: Ensure the accuracy of calibration tasks as it directly impacts the quality of client’s operations.
Reaching New Heights: Senior Field Service Calibration Technician
The Senior Field Service Calibration Technician is the next step in your career path.
In this role, you’ll be a leader within the team, responsible for complex calibrations, training junior technicians, and ensuring service quality.
To excel in this role:
- Mentorship: Share your knowledge and help junior technicians to grow.
- Leadership: Lead by example and inspire others with your dedication and technical skills.
- Process Improvement: Work on improving calibration processes to increase efficiency and quality.
Beyond the Horizon: Calibration Supervisor
As your career progresses, you may transition into the role of a Calibration Supervisor.
In this position, you’ll manage a team of technicians, oversee calibration operations, and ensure compliance with regulations.
Here’s what to focus on:
- Management Skills: Develop leadership and communication skills to guide your team effectively.
- Regulatory Compliance: Stay updated with industry regulations and ensure your team’s compliance.
- Client Relations: Maintain good relationships with clients, understand their needs, and ensure their satisfaction.
Pinnacle of Success: Calibration Manager or Director
At the highest level of this career path, you might become a Calibration Manager or Director.
Here, you’ll be responsible for the overall calibration strategy of your organization, ensuring accuracy across all operations, managing client relations, and leading larger teams.
Field Service Calibration Technician Salary
Entry-Level Field Service Calibration Technician
- Median Salary: $40,000 – $50,000 per year
- Entry-level calibration technicians typically have 0-2 years of experience and often hold a degree or diploma in an engineering or technical field. They start by assisting senior technicians, calibrating less complex equipment and learning standard procedures.
Mid-Level Field Service Calibration Technician
- Median Salary: $50,000 – $65,000 per year
- With 2-5 years of experience, mid-level technicians have developed the skills needed to calibrate a broader range of equipment and may begin to specialize in certain types of calibration. They typically work independently and may start training junior technicians.
Senior Field Service Calibration Technician
- Median Salary: $65,000 – $85,000 per year
- Senior calibration technicians possess 5+ years of experience. They are responsible for calibrating the most complex equipment, troubleshooting and resolving problems, and often play a lead role in training and mentoring less experienced technicians.
Calibration Supervisor / Manager
- Median Salary: $75,000 – $100,000+ per year
- These roles require extensive calibration experience and strong management skills. Calibration supervisors or managers oversee teams of technicians, manage schedules, ensure quality standards are met, and liaise with customers.
Director of Calibration Services
- Median Salary: $100,000 – $150,000+ per year
- At the highest level, the Director of Calibration Services is responsible for the overall strategy and operations of the calibration department, including budgeting, policy development, personnel management, and customer relations.
Field Service Calibration Technician Work Environment
Field Service Calibration Technicians usually work in a variety of settings depending on the industry they are employed in.
This could include manufacturing plants, laboratories, aerospace industries, or the military, among others.
They are often required to travel to different job sites to calibrate and troubleshoot various equipment and instruments.
These technicians frequently work a standard work week, but they might be on call or work overtime, especially when equipment malfunctions or calibration deadlines are imminent.
After gaining extensive experience and expertise, a Field Service Calibration Technician may choose to progress their career by specializing in a specific industry or by taking on a supervisory role.
Safety is a crucial aspect of their work environment as they often deal with sensitive and expensive equipment.
They are trained to adhere to strict safety protocols to ensure both their safety and the proper functioning of the equipment they handle.
FAQs About Becoming a Field Service Calibration Technician
What is needed to become a Field Service Calibration Technician?
To become a Field Service Calibration Technician, you typically need a background in electronics or a related field.
This can be achieved through a combination of formal education (such as an associate’s degree or certificate in electronics technology), vocational training, and practical experience.
Key skills include knowledge of electronic, mechanical, and instrumentation systems, troubleshooting abilities, and precision in handling tools.
Proficiency in using calibration software is also important.
In addition, soft skills like good communication, customer service, and problem-solving abilities are crucial in this role.
How long does it take to become a Field Service Calibration Technician?
The time it takes to become a Field Service Calibration Technician can vary depending on your educational path and level of practical experience.
If you pursue an associate’s degree or certificate program in electronics or a related field, it typically takes two years.
On-the-job training can take a few months to a year.
Therefore, you can potentially enter the field within two to three years.
Can I become a Field Service Calibration Technician without a degree?
Yes, it is possible to become a Field Service Calibration Technician without a traditional degree.
Many employers value practical experience and skills over formal education.
You can gain the required skills through vocational training, online courses, or on-the-job training.
However, having a degree or certificate may provide a competitive edge and open up more opportunities, particularly in industries that require specialized or advanced knowledge.
Is being a Field Service Calibration Technician a stressful job?
Being a Field Service Calibration Technician can be demanding at times, as it involves field work, dealing with complicated instruments, and meeting customer expectations.
The level of stress can vary depending on the work environment, the complexity of the tasks, and the individual’s time management and problem-solving skills.
Despite the challenges, many technicians find the job rewarding as it provides opportunities to work on diverse projects and continuously learn about new technologies.
What are the prospects for Field Service Calibration Technicians in the next decade?
The prospects for Field Service Calibration Technicians are expected to grow in the next decade due to the increasing reliance on sophisticated instrumentation in various industries such as healthcare, manufacturing, and telecommunications.
Technicians with advanced skills, experience in specific industries, and knowledge of the latest technologies will have the best job opportunities.
Conclusion
And there you have it.
Committing to the journey to become a Field Service Calibration Technician is no easy task, but it’s undoubtedly fulfilling.
Equipped with the proper skills, training, and determination, you’re on the brink of making a substantial impact in the industrial and scientific sectors.
Remember, the path may be demanding, but the rewards are endless. Your expertise could contribute significantly to ensuring the accuracy and quality of industrial and scientific processes and equipment.
So, take that initial leap. Immerse yourself in learning. Connect with industry professionals. And above all, never cease to refine your technical skills.
Because the world is waiting for your precision and skill.
And if you’re looking for personalized guidance on starting or advancing your career as a Field Service Calibration Technician, check out our AI Career Path Advisor.
This complimentary tool is designed to provide tailored advice and resources to help you navigate your career path effectively.
The Unusual Workday: Jobs That Break Every Stereotype
The Goldmine List: Top Highest Paying Jobs and How to Qualify for Them!
Flex and Achieve: The Most Flexible Jobs for Goal Setters