24 Jobs For Beginner Welders (Molten Opportunities)
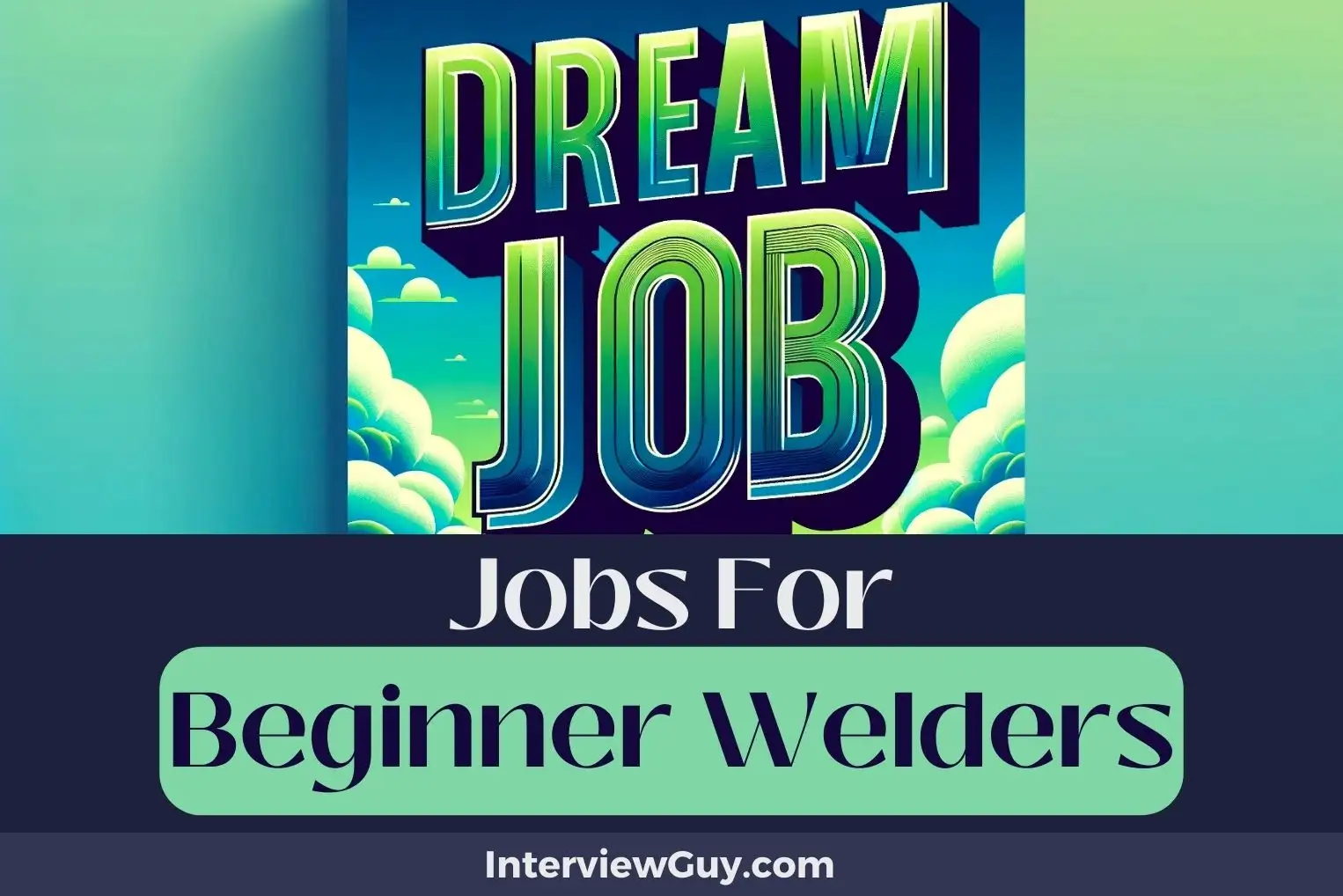
Are you new to the welding scene? Fascinated by the sparks flying and the creation of strong, enduring structures?
If so, you’re in for a rewarding ride!
Today, we’re exploring a range of job opportunities ideal for novice welders.
From construction site welding to precision aeronautical welding. Each one, is a fantastic fit for those who are passionate and patient about welding.
Imagine being engulfed in the beauty of the welding process. Day in, day out.
Captivating, isn’t it?
So, strap on your welding helmet,
And get ready to discover your dream welding profession!
Welding Apprentice
Average Salary: $30,000 – $40,000 per year
Welding Apprentices are entry-level workers who assist skilled welders in various tasks while gaining hands-on experience in welding, cutting, and fabricating metal.
This role is ideal for beginner welders who are eager to learn the trade through practical experience and mentorship.
Job Duties:
- Assisting Skilled Welders: Aid experienced welders by preparing materials, maintaining equipment, and performing basic welding tasks under supervision.
- Learning Welding Techniques: Acquire knowledge of different welding methods and practices, including MIG, TIG, Stick, and Flux-Cored welding.
- Understanding Blueprints: Learn to read and interpret blueprints and sketches to understand project specifications and requirements.
- Maintaining Safety Standards: Adhere to all safety protocols and regulations to ensure a safe working environment.
- Material Preparation: Cut or join metal parts as directed, and learn to inspect parts for defects and quality.
- Continuous Improvement: Participate in ongoing training and educational opportunities to enhance welding skills and knowledge.
Requirements:
- Educational Background: A high school diploma or equivalent; enrollment in a vocational training program or welding certification course is beneficial.
- Basic Welding Knowledge: Familiarity with welding tools, materials, and safety procedures.
- Physical Fitness: Ability to handle physically demanding tasks, including lifting heavy materials and working in various positions.
- Attention to Detail: Precision and attention to detail when working on welding tasks.
- Willingness to Learn: Eagerness to learn from experienced welders and continuously improve one’s own skills.
Career Path and Growth:
As a Welding Apprentice, you’ll have the opportunity to build a foundation of skills that are essential for a successful career in the welding industry.
With dedication and experience, apprentices can become certified welders and may specialize in areas such as underwater welding, pipeline welding, or aerospace welding.
Career advancement often includes positions such as Welding Technician, Welding Inspector, or even a Welding Instructor.
MIG Welder
Average Salary: $33,000 – $55,000 per year
MIG (Metal Inert Gas) Welders are skilled tradespeople who specialize in a specific type of welding process used in various industries, including construction, manufacturing, and automotive repair.
This role is ideal for beginner welders who are seeking a practical, hands-on career in a high-demand trade.
Job Duties:
- Welding Components: Utilize MIG welding techniques to join metal parts for a variety of applications and projects.
- Reading Blueprints: Interpret welding blueprints and plans to understand project specifications and requirements.
- Equipment Maintenance: Perform regular maintenance on welding equipment to ensure optimal performance and safety.
- Quality Control: Inspect finished welds to meet industry standards and project specifications for safety and durability.
- Material Preparation: Prepare metal surfaces by cleaning, cutting, or shaping them before welding.
- Staying Informed: Keep updated with new welding technologies, safety protocols, and industry best practices.
Requirements:
- Educational Background: A high school diploma or equivalent, with vocational training or a certificate in welding technology from a trade school.
- Technical Skills: Proficiency in MIG welding techniques and the ability to work with various tools and machinery.
- Attention to Detail: Keen attention to detail to produce clean and precise welds.
- Physical Stamina: Good physical condition to handle long hours of standing, bending, and lifting heavy materials.
- Safety Consciousness: Strict adherence to safety protocols to prevent workplace accidents and injuries.
Career Path and Growth:
As a MIG Welder, you can expect to build a career in a field where skilled labor is consistently in demand.
With experience, you may move up to supervisory roles, become a welding inspector, or specialize further in advanced welding technologies.
Continuous learning and certification can lead to increased job opportunities and higher pay.
TIG Welder
Average Salary: $40,000 – $55,000 per year
TIG (Tungsten Inert Gas) Welders perform precise and critical welding operations in a variety of industries, including aerospace, automotive, and manufacturing.
This role is perfect for beginner welders who have an eye for detail and are seeking to specialize in a welding technique known for its high quality and clean results.
Job Duties:
- Performing Precision Welding: Execute TIG welding operations on various metals, ensuring strong and precise welds that meet industry standards.
- Reading Blueprints: Interpret technical drawings and blueprints to understand the specific welding requirements for each project.
- Setting Up Equipment: Prepare welding equipment, adjust settings, and perform maintenance to ensure optimal performance during the welding process.
- Inspecting Welds: Examine completed welds for defects and ensure they pass specific strength and quality tests.
- Material Preparation: Clean and prepare surfaces before welding and choose appropriate filler materials for different metal types.
- Safety Compliance: Adhere to safety protocols and wear appropriate personal protective equipment to prevent accidents and injuries.
Requirements:
- Technical Training: A high school diploma or equivalent, with technical training or vocational schooling in welding techniques, specifically TIG welding.
- Attention to Detail: Precision and a steady hand are crucial for creating clean and accurate welds.
- Physical Stamina: The ability to work for long periods, often in challenging positions or environments.
- Mathematics and Measurement: Basic math skills and the ability to measure and align workpieces accurately.
- Certification: Welding certification, such as an AWS (American Welding Society) certification, is often preferred or required by employers.
Career Path and Growth:
Entry-level TIG Welders have the opportunity to become highly skilled in a specialized and in-demand welding process.
With experience and additional certifications, TIG Welders can advance to supervisory positions, quality control, or welding inspection roles.
They may also choose to specialize further in industries that require precision welding, such as custom fabrication or aerospace engineering.
Stick Welder
Average Salary: $35,000 – $45,000 per year
Stick Welders, also known as Shielded Metal Arc Welders, perform essential tasks in construction and manufacturing, using electric current to cut and join metal parts.
This role is ideal for beginners in welding who are seeking a foundational position in the industry, allowing them to develop their skills in a hands-on environment.
Job Duties:
- Operating Welding Equipment: Use stick welding machines to fuse metal parts together according to specifications.
- Reading Blueprints: Understand and follow detailed blueprints or plans for the welding project at hand.
- Inspecting Structures: Check the structural integrity of welds and the construction elements they are joining.
- Maintaining Equipment: Perform regular maintenance on welding equipment and ensure that all safety standards are met.
- Material Preparation: Prepare the materials to be welded, which may involve cutting, grinding, or shaping components before welding.
- Adhering to Safety Protocols: Follow strict safety procedures to prevent accidents and injuries while working with high-temperature equipment and hazardous materials.
Requirements:
- Technical Training: A high school diploma or equivalent, coupled with technical training in welding from a vocational school or community college.
- Hands-on Experience: On-the-job training or apprenticeship to gain practical experience in stick welding techniques.
- Attention to Detail: Ability to produce precise and clean welds that meet structural requirements.
- Physical Stamina: Strength and endurance to handle heavy equipment and work in various positions for extended periods.
- Understanding of Safety: Knowledge of safety practices and the use of protective gear to ensure a safe work environment.
Career Path and Growth:
Beginning as a Stick Welder offers a solid entry point into the welding industry.
With experience, welders can specialize in different types of welding, advance to supervisory roles, or obtain certifications that open doors to higher-paying positions and complex projects.
As proficiency grows, many welders opt to start their own welding businesses or move into related fields such as welding inspection or education.
Underwater Welder
Average Salary: $55,000 – $200,000 per year
Underwater welders play a critical role in the maintenance and repair of various underwater structures, from oil rigs to pipelines to naval vessels.
This role is perfect for beginner welders who are also drawn to the adventure of deep-sea exploration and have a passion for marine environments.
Job Duties:
- Performing Underwater Welding: Execute welding tasks below the water surface, adhering to strict safety and technical standards.
- Inspection and Repair: Assess the integrity of underwater structures and perform necessary repairs or maintenance.
- Operating Specialized Equipment: Utilize advanced diving and welding gear designed for high-pressure underwater environments.
- Collaborating with Dive Teams: Work as part of a skilled team that includes divers, engineers, and other specialists.
- Ensuring Safety Compliance: Follow all safety protocols to minimize risk in a hazardous work environment.
- Staying Certified: Maintain up-to-date certifications in diving and welding, including regular fitness and skills testing.
Requirements:
- Educational Background: A commercial diving certification, as well as a welding certification, from an accredited trade school or program.
- Physical Fitness: Excellent health and physical condition to handle the demands of underwater work and operate heavy equipment.
- Diving Skills: Proficient in commercial diving techniques and comfortable working in challenging underwater conditions.
- Technical Skills: Strong practical welding skills, with the ability to perform precise welds in an underwater setting.
- Problem-Solving: Ability to think critically and solve problems under pressure while submerged.
Career Path and Growth:
As an underwater welder, you can expect to engage in a variety of challenging projects that not only push the limits of your welding skills but also offer unique adventures.
With experience, underwater welders can move into supervisory or consultant roles, specialize in hyperbaric welding technology, or advance to international projects offering higher pay and greater challenges.
Fabrication Welder
Average Salary: $35,000 – $50,000 per year
Fabrication Welders are skilled tradespeople who specialize in joining metal parts together using various welding techniques for the construction of structures and machinery.
This role is ideal for beginner welders who have a keen interest in crafting and assembling metal components across diverse industries.
Job Duties:
- Reading Blueprints: Interpret technical drawings and plans to understand the specifications for welding projects.
- Welding and Fabrication: Use different welding methods (such as MIG, TIG, Stick, or Flux-Cored) to fabricate and assemble metal structures and equipment.
- Quality Control: Inspect completed welds to ensure that they meet design requirements, are free from defects, and are up to code specifications.
- Equipment Maintenance: Perform routine maintenance on welding equipment and machinery to ensure proper functionality.
- Material Preparation: Cut and prepare metal components for welding, using appropriate tools and techniques.
- Adhering to Safety Standards: Follow all occupational safety guidelines to minimize risk and ensure a safe working environment.
Requirements:
- Educational Background: A high school diploma is required, with technical training or certification in welding being highly advantageous.
- Technical Skills: Proficiency in various welding techniques and the ability to read and follow blueprints.
- Attention to Detail: Excellent precision and attention to detail to produce high-quality welds and fabrications.
- Physical Stamina: Good physical condition to handle long periods of standing, bending, and lifting heavy materials.
- Problem-Solving: Ability to troubleshoot and resolve issues that arise during the fabrication process.
Career Path and Growth:
As a Fabrication Welder, there are many opportunities for career advancement.
With experience and further certification, welders can become welding inspectors, supervisors, or move into specialized welding fields.
Ambitious welders may also pursue additional education to become welding engineers or project managers, overseeing larger fabrication projects and teams.
The need for skilled welders is consistent across various industries, including construction, manufacturing, and aerospace, providing a stable and rewarding career path.
Pipefitter
Average Salary: $40,000 – $75,000 per year
Pipefitters are skilled tradespeople who specialize in the layout, assembly, installation, and maintenance of piping systems.
This role is ideal for beginner welders who are interested in a hands-on career working with various types of pipes and systems used in industrial, commercial, and residential settings.
Job Duties:
- Reading Blueprints: Interpret blueprints and building specifications to map layout for pipes, drainage systems, and other plumbing materials.
- Installing Piping Systems: Assemble and secure pipes, tubes, fittings, and related equipment, according to specifications by welding, brazing, cementing, soldering, and threading joints.
- Maintenance and Repair: Troubleshoot and repair pipe systems and pipelines, including the replacement of worn components.
- Ensuring Compliance: Ensure all installations, repairs, and maintenance meet the code requirements, safety standards, and environmental regulations.
- Coordination with Other Trades: Collaborate with contractors, construction workers, electricians, pipefitters, and steamfitters on job sites.
- Equipment Operation: Operate heavy machinery, such as forklifts and pipe benders, to handle and shape piping materials.
Requirements:
- Educational Background: A high school diploma or equivalent; completion of an apprenticeship or vocational training in pipefitting is highly beneficial.
- Technical Skills: Proficiency in welding, brazing, and soldering, with a solid understanding of piping and plumbing systems.
- Physical Strength and Stamina: Ability to handle heavy materials and stand for long periods.
- Detail-Oriented: Precision in following blueprints and building codes.
- Safety Consciousness: Adherence to safety protocols and the ability to work safely with tools and machinery.
- Problem-Solving Skills: Aptitude for troubleshooting and resolving issues with piping systems.
Career Path and Growth:
Pipefitters have a clear pathway for career advancement.
With experience, they can become journeyman pipefitters, supervisors, project managers, or even start their own contracting business.
The demand for pipefitters is expected to remain strong due to ongoing construction projects, infrastructure upgrades, and the need for maintenance of existing systems, leading to a stable and potentially lucrative career for skilled tradespeople.
Boilermaker
Average Salary: $40,000 – $60,000 per year
Boilermakers are skilled tradespeople who fabricate, install, and repair boilers, tanks, and other large vessels that hold liquids and gases.
This role is ideal for beginner welders who are interested in a hands-on career involving heavy-duty equipment and intricate construction projects.
Job Duties:
- Fabricating Boiler Parts: Use welding techniques to create and assemble boiler components from blueprints and specifications.
- Installing Boilers and Vessels: Erect and secure boilers and other large containers, ensuring they meet safety and efficiency standards.
- Performing Repairs and Maintenance: Conduct regular inspections and perform necessary repairs to maintain the functionality and safety of boilers and related equipment.
- Reading Blueprints: Accurately interpret technical drawings and plans to guide the construction or repair of boiler systems.
- Ensuring Safety Compliance: Follow strict safety protocols to prevent accidents and injuries while working with potentially hazardous materials.
- Continual Learning: Stay informed about advancements in welding techniques, materials science, and safety regulations within the industry.
Requirements:
- Educational Background: A high school diploma or equivalent, with additional training in welding and fabrication from a vocational school or apprenticeship program.
- Technical Skills: Proficiency in various welding methods, knowledge of metallurgy, and familiarity with construction tools and machinery.
- Physical Stamina: Ability to handle physically demanding tasks, including lifting heavy objects and working in confined spaces.
- Attention to Detail: Keen eye for detail to ensure high-quality welds and adherence to specifications.
- Safety Consciousness: Commitment to following safety guidelines and wearing appropriate protective gear.
Career Path and Growth:
Boilermaking is a specialized career that offers a clear path for advancement.
Beginner welders can start as apprentices and eventually become journeypersons with the potential to lead projects or supervise teams.
With experience, Boilermakers can move into inspector roles, project management, or even start their own contracting businesses.
There is also a demand for skilled Boilermakers in various industries, such as construction, manufacturing, and energy, providing diverse opportunities for career growth.
Structural Welder
Average Salary: $40,000 – $65,000 per year
Structural Welders play a crucial role in the construction and maintenance of various structures, from buildings and bridges to ships and industrial facilities.
This role is ideal for beginner welders who take pride in the strength and stability of their work and have an interest in contributing to the backbone of infrastructure and industry.
Job Duties:
- Interpreting Blueprints: Read and understand complex blueprints and structural designs to determine the specific welding requirements.
- Performing Welds: Use various welding techniques to join metal parts according to specifications, ensuring structural integrity.
- Inspecting Welds: Examine welds to ensure they meet design standards, regulations, and safety requirements.
- Maintaining Equipment: Keep welding tools and machinery in good working condition, performing regular maintenance as necessary.
- Adhering to Safety Protocols: Follow strict safety guidelines to prevent accidents and ensure a safe working environment.
- Collaborating with Construction Teams: Work closely with other construction professionals to coordinate tasks and complete projects efficiently.
Requirements:
- Educational Background: A high school diploma or equivalent; formal training through a vocational school, technical college, or apprenticeship program is highly beneficial.
- Technical Skills: Proficiency in various welding techniques (such as SMAW, MIG, TIG, and FCAW) and the ability to work with different materials.
- Certifications: Possession of relevant welding certifications (such as AWS D1.1) is often required or preferred.
- Physical Fitness: Good physical condition to handle the demanding nature of the job, including lifting heavy materials and working in various positions.
- Attention to Detail: Strong focus on detail to ensure welds are completed accurately and meet structural specifications.
Career Path and Growth:
A career as a Structural Welder offers a solid foundation for growth within the welding and construction industries.
With experience, welders can specialize in more advanced techniques, pursue certifications for higher-level projects, or transition into supervisory roles such as a welding foreman or inspector.
The skills developed in structural welding are also transferable to other industries, such as aerospace or automotive manufacturing, providing diverse career opportunities.
Sheet Metal Worker
Average Salary: $40,000 – $60,000 per year
Sheet Metal Workers fabricate, install, and repair sheet metal products and equipment, such as ducts for heating and air conditioning systems, roofs, siding, and gutters.
This role is perfect for beginner welders who have a hands-on approach to crafting and constructing with metal.
Job Duties:
- Fabricating Sheet Metal: Use various tools and machinery to cut, shape, and assemble sheet metal products to precise specifications.
- Welding and Joining: Employ welding techniques to join or repair metal parts within various construction and installation projects.
- Installing HVAC Systems: Fit and install ductwork for heating, ventilation, and air conditioning systems, ensuring proper alignment and connection.
- Reading Blueprints: Interpret detailed blueprints and plans to accurately fabricate and install sheet metal components.
- Ensuring Safety: Adhere to strict safety protocols to prevent injuries and ensure the safe operation of tools and machinery.
- Maintenance and Repair: Conduct routine maintenance and repair of sheet metal products and structures, prolonging their lifespan and functionality.
Requirements:
- Technical Training: A high school diploma or equivalent, combined with technical training in sheet metal work or welding, is often required.
- Welding Skills: Proficiency in various welding techniques, with a focus on those relevant to sheet metal work.
- Physical Fitness: The ability to handle physical work, including lifting heavy materials and standing for long periods.
- Attention to Detail: A keen eye for detail to ensure precise measurements and cuts, leading to high-quality workmanship.
- Problem-Solving: The ability to troubleshoot and solve issues that may arise during the fabrication or installation process.
Career Path and Growth:
Sheet Metal Workers can start with basic tasks and, through experience and additional training, advance to more complex projects and leadership roles.
Opportunities for growth include becoming a journeyman, foreman, or project manager.
Some may choose to specialize in areas such as HVAC installation or custom metal fabrication or even start their own sheet metal business.
Robotics Welding Technician
Average Salary: $40,000 – $60,000 per year
Robotics Welding Technicians operate and maintain robotic welding systems used in manufacturing and construction.
This role is ideal for beginner welders who are interested in advanced manufacturing technology and robotics.
Job Duties:
- Operating Robotic Welding Machinery: Set up and control robotic welding machines to join metal parts as specified by blueprints and work orders.
- Performing Maintenance: Conduct routine maintenance and troubleshooting on welding robots to ensure optimal performance and minimal downtime.
- Quality Control: Inspect welded components to ensure they meet design requirements and quality standards.
- Programming and Adjustments: Input and adjust programming parameters for robotic welders to achieve desired welding results.
- Collaboration with Engineering Teams: Work closely with engineers to refine welding processes and implement new welding technology.
- Staying Current with Technology: Continuously learn about the latest advancements in robotic welding and related technologies.
Requirements:
- Technical Training: A certificate or associate degree in welding technology, robotics, or a related field is highly beneficial.
- Hands-On Experience: Practical experience with welding, especially in a robotic or automated environment.
- Technical Skills: Proficiency in reading blueprints, programming robotic machines, and understanding welding specifications.
- Attention to Detail: Ability to focus on precise welding tasks and adhere to strict quality standards.
- Problem-Solving: Aptitude for identifying and resolving issues with robotic equipment or welding processes.
Career Path and Growth:
As a Robotics Welding Technician, there is potential for career advancement within the field of industrial automation.
With experience, one may progress to supervisory roles, become a welding inspector, or specialize further in robotics programming and maintenance.
Continuous learning and certification in advanced robotic systems can lead to high-demand, well-compensated positions within the industry.
Iron Worker
Average Salary: $40,000 – $70,000 per year
Iron Workers are skilled tradespeople who fabricate, install, and repair the steel frameworks for buildings, bridges, and other structures.
This role is ideal for beginner welders who are eager to work in a physically demanding environment and have an interest in constructing the backbone of infrastructural projects.
Job Duties:
- Fabricating Steel Frameworks: Read and interpret blueprints to cut, weld, and assemble steel components for various construction projects.
- Erecting Structures: Install iron or steel beams, girders, and columns to form the structural framework for buildings and bridges.
- Reinforcing Concrete: Place and tie steel bars (rebar) in concrete forms to reinforce structures.
- Repairing and Maintenance: Conduct repair work on existing steel structures, including welding and replacing damaged sections.
- Following Safety Protocols: Comply with all safety regulations and practices, including the proper use of harnesses, hard hats, and other safety gear.
- Collaboration: Work closely with other tradespeople, such as carpenters and concrete workers, to coordinate construction efforts.
Requirements:
- Technical Training: Completion of a welding program or apprenticeship in ironworking is highly desirable.
- Physical Strength and Stamina: Ability to perform physically demanding tasks and work in high places or adverse weather conditions.
- Welding Skills: Proficiency in various welding techniques and the ability to read welding blueprints.
- Attention to Detail: Keen eye for detail to ensure the structural integrity and precision of steel frameworks.
- Safety-Minded: A commitment to maintaining a safe work environment and knowledge of construction safety standards.
Career Path and Growth:
As an Iron Worker, you will have the opportunity to work on a variety of construction projects, gaining expertise in the field of steelwork and construction.
With experience, Iron Workers can advance to supervisory positions, such as foreman or site superintendent, or specialize in areas like welding inspection, structural design, or project management.
Skilled Iron Workers may also become self-employed contractors or start their own construction firms.
Welding Inspector
Average Salary: $50,000 – $70,000 per year
Welding Inspectors play a critical role in the construction and manufacturing industries by ensuring that welding work meets specific standards and is both safe and effective.
This role is ideal for beginner welders who have a keen eye for detail and a commitment to upholding safety and quality in welding projects.
Job Duties:
- Inspecting Welds: Examine welds to ensure they meet industry standards, codes, and specifications.
- Documenting Inspection Results: Record findings and prepare reports on the inspected welds.
- Ensuring Safety: Check that all welding activities comply with safety regulations to prevent accidents.
- Advising on Welding Techniques: Provide feedback and recommendations to welding teams to improve quality and efficiency.
- Continuous Learning: Stay up-to-date with the latest welding technologies, standards, and inspection methods.
Requirements:
- Educational Background: A high school diploma or equivalent; additional certification in welding inspection, such as from the American Welding Society (AWS), is highly advantageous.
- Attention to Detail: Excellent observational skills to detect flaws or defects in welds.
- Technical Knowledge: Strong understanding of welding processes, metallurgy, and the properties of different materials.
- Communication Skills: Ability to clearly communicate inspection findings and provide constructive feedback to welding personnel.
- Problem-Solving: Aptitude for identifying issues and determining the best course of action to rectify them.
Career Path and Growth:
As a Welding Inspector, you have the opportunity to ensure the integrity and safety of critical structures and products.
With further experience and qualifications, you can advance to senior inspector roles, specialize in areas such as underwater or pipeline welding inspection, or move into quality control management positions in the welding industry.
Automotive Welder
Average Salary: $40,000 – $60,000 per year
Automotive Welders are skilled tradespeople specializing in welding metal parts for vehicles, including cars, trucks, and motorcycles.
This role is ideal for beginner welders who have a keen interest in the automotive industry and enjoy working with their hands to create and repair metal components.
Job Duties:
- Vehicle Part Fabrication: Use welding techniques to fabricate and repair metal parts for various types of vehicles.
- Quality Control: Inspect welded surfaces and structures to discover flaws and ensure that welding work meets industry standards.
- Equipment Maintenance: Maintain and troubleshoot welding equipment and tools to ensure optimal performance.
- Customization Projects: Work on custom vehicle projects that require unique welding solutions and creative metalwork.
- Collaboration with Automotive Teams: Collaborate with other automotive professionals to ensure cohesive vehicle assembly and repair.
- Adherence to Safety Standards: Follow strict safety guidelines to prevent accidents and ensure a safe working environment.
Requirements:
- Technical Training: A certificate or diploma in welding technology, with a focus on automotive applications.
- Hands-on Skills: Proficiency in various welding techniques, such as MIG, TIG, and arc welding, tailored to automotive needs.
- Attention to Detail: Precision and attention to detail are essential for producing strong, reliable welds and ensuring vehicle safety.
- Physical Stamina: The ability to work in various positions and environments, often under challenging conditions.
- Problem-Solving: Aptitude for troubleshooting and resolving issues that arise during the welding process.
Career Path and Growth:
As an Automotive Welder, you have the opportunity to work on a wide range of projects, from standard vehicle repairs to specialized custom fabrications.
With experience, Automotive Welders can advance to supervisory roles, open their own welding shops, or specialize further in high-performance or luxury vehicle welding, enhancing their expertise and earning potential.
Aerospace Welder
Average Salary: $40,000 – $60,000 per year
Aerospace Welders are skilled professionals who specialize in welding materials for aircraft, spacecraft, and related equipment.
This role is ideal for beginner welders who are fascinated with aviation and space exploration and desire to contribute to the construction and maintenance of vehicles that traverse the skies and beyond.
Job Duties:
- Fabricating Aerospace Components: Weld various metals and materials used in the construction of aircraft and spacecraft structures, engines, and other systems.
- Adhering to Precision Standards: Maintain high standards of precision to meet the stringent requirements of aerospace welding, following technical specifications and blueprints.
- Inspecting Welds: Conduct thorough inspections of welds to ensure they meet quality standards and are free of defects that could compromise safety.
- Applying Welding Techniques: Utilize specialized welding techniques such as TIG (Tungsten Inert Gas) and MIG (Metal Inert Gas), which are commonly required in aerospace applications.
- Collaborating with Engineering Teams: Work closely with engineers and other technicians to understand requirements and contribute to the design and modification of aerospace components.
- Continuous Learning: Keep abreast of the latest advancements in welding technology and techniques specific to the aerospace industry.
Requirements:
- Technical Training: A certificate or degree in welding technology, with a focus on or specialization in aerospace welding techniques.
- Attention to Detail: Ability to perform precise and accurate work, as aerospace components require a high level of precision.
- Certification: Possession of welding certifications, particularly those relevant to aerospace applications (e.g., AWS D17.1 certification).
- Physical Dexterity: Good hand-eye coordination and the ability to handle welding equipment skillfully in various positions.
- Safety Consciousness: Knowledge of and adherence to safety protocols to ensure a safe working environment.
Career Path and Growth:
Beginning as an Aerospace Welder offers a unique opportunity to enter a specialized field with substantial growth potential.
With experience and additional certifications, welders can advance to more complex projects, take on supervisory roles, or become welding inspectors.
There is also the potential to work on cutting-edge aerospace technology and contribute to missions that push the boundaries of human capability in space.
Shipyard Welder
Average Salary: $40,000 – $60,000 per year
Shipyard Welders are skilled tradespeople who specialize in welding metals used in shipbuilding and repair.
They work in shipyards, contributing to the construction and maintenance of various types of marine vessels.
This role is ideal for beginner welders interested in maritime construction and who enjoy working with their hands in a challenging, outdoor environment.
Job Duties:
- Welding Metal Components: Execute precise welding techniques to join or repair metal parts of ships and other maritime structures.
- Reading Blueprints: Interpret and follow complex blueprints and technical drawings to ensure accurate construction and assembly.
- Quality Control: Inspect welds to ensure they meet safety standards and are free from defects.
- Maintenance and Repair: Perform routine maintenance and emergency repairs on existing ships to prolong their service life.
- Using Specialized Equipment: Safely operate specialized welding equipment, including underwater welding gear if required.
- Following Safety Protocols: Adhere to strict safety guidelines to prevent accidents and injuries in the shipyard.
Requirements:
- Technical Training: A certificate or diploma in welding from a recognized trade school, or equivalent on-the-job training.
- Physical Stamina: Ability to work for extended periods in physically demanding conditions, including confined spaces and heights.
- Attention to Detail: Strong focus on precision and detail to ensure high-quality welds and adherence to specifications.
- Manual Dexterity: Skilled in using hands and tools to perform intricate welding tasks.
- Safety Consciousness: Commitment to maintaining a safe working environment and knowledge of occupational hazards and safety precautions.
Career Path and Growth:
As a Shipyard Welder, there are opportunities to advance to supervisory positions, quality control, or inspection roles.
With additional certifications, such as underwater welding, welders can increase their expertise and value in the field.
Experienced welders may also transition to teaching positions in trade schools or become welding inspectors, ensuring that industry standards are met across various projects.
Manufacturing Welder
Average Salary: $33,000 – $58,000 per year
Manufacturing Welders play a crucial role in the construction and repair of metal products by joining parts using various welding techniques.
This role is ideal for beginner welders who are looking to apply their skills in a hands-on, industrial environment and take pride in contributing to the creation of tangible goods.
Job Duties:
- Performing Welding Tasks: Use different welding methods such as MIG, TIG, or Stick welding to join metal parts according to blueprints and specifications.
- Inspecting Materials: Examine materials and structures before and after welding to ensure that they meet compliance standards.
- Maintaining Equipment: Oversee the proper maintenance of welding machinery and equipment to ensure optimal performance and safety.
- Reading Blueprints: Understand and follow detailed assembly instructions, processes, and blueprints to ensure product quality.
- Quality Control: Conduct tests and inspections of products to ensure the welds meet quality standards and are defect-free.
- Staying Informed: Keep up-to-date with the latest welding techniques, safety protocols, and industry advancements.
Requirements:
- Educational Background: A high school diploma or equivalent; completion of a vocational training program in welding is highly beneficial.
- Technical Skills: Proficiency in various welding techniques and the ability to read and interpret blueprints and technical drawings.
- Physical Stamina: Good physical condition to handle the demands of standing for long periods, lifting heavy materials, and working in various positions.
- Certification: Possession of a welding certification, such as AWS Certified Welder, can be advantageous and is often required by employers.
- Safety Consciousness: A strong understanding of and adherence to safety practices and regulations in the welding industry.
Career Path and Growth:
Manufacturing welders have numerous opportunities for career growth.
With experience, they can become welding inspectors, supervisors, or move into advanced specialized welding roles.
Consistent performance and additional certifications can lead to higher-paying positions and greater responsibility within the manufacturing industry.
Maintenance Welder
Average Salary: $40,000 – $60,000 per year
Maintenance Welders are responsible for performing welding repairs and ensuring the maintenance of various types of industrial equipment.
This role is ideal for beginner welders who have an interest in maintaining the structural integrity of machinery and infrastructure.
Job Duties:
- Performing Equipment Repairs: Use welding techniques to fix broken or worn parts on machinery and equipment, ensuring they are brought back to working condition.
- Inspecting Structures: Evaluate the condition of metal structures and determine the best method for repair or reinforcement.
- Fabricating Metal Parts: Create new metal components or replacement parts using welding equipment.
- Following Safety Protocols: Adhere to all safety guidelines and procedures to maintain a safe work environment.
- Reading Blueprints: Interpret and follow blueprints or welding diagrams for repair work.
- Continuous Learning: Stay up-to-date with welding techniques and technologies to improve efficiency and quality of work.
Requirements:
- Technical Training: A diploma from a vocational school, technical college, or an apprenticeship in welding is often required.
- Welding Certifications: Possession of relevant welding certifications, such as AWS (American Welding Society) certification.
- Hands-on Experience: Practical experience with different welding methods, such as MIG, TIG, or stick welding.
- Physical Stamina: Ability to perform physically demanding tasks and stand for long periods.
- Attention to Detail: Keen eye for detecting flaws in metal structures and ensuring high-quality welds.
- Problem-Solving Skills: Aptitude for identifying issues and determining the most effective repair solutions.
Career Path and Growth:
As a Maintenance Welder, you will play a crucial role in the upkeep and longevity of industrial machinery and infrastructure.
With experience, Maintenance Welders can advance to supervisory roles, become specialized welding inspectors, or move into higher-paying positions that involve complex and critical welding projects in various industries, such as aerospace or manufacturing.
Welding Instructor
Average Salary: $40,000 – $60,000 per year
Welding Instructors lead and educate groups or individuals in the art and science of various welding techniques and practices.
This role is ideal for experienced welders who enjoy sharing their knowledge and expertise with the next generation of welding professionals.
Job Duties:
- Conducting Practical Demonstrations: Teach students through hands-on demonstrations of welding techniques, ensuring safety and proper use of equipment.
- Presenting Theoretical Knowledge: Educate students on the principles of metallurgy, welding theory, and blueprint reading.
- Answering Questions: Provide clear and informative answers to students’ queries, covering everything from basic welding techniques to advanced industry practices.
- Developing Curriculum: Design course materials and lesson plans that cover both theoretical knowledge and practical skills in welding.
- Skills Assessment: Evaluate and provide constructive feedback on students’ welding projects and practical exams.
- Staying Informed: Continuously update your knowledge about advancements in welding technology, techniques, and safety protocols.
Requirements:
- Educational Background: A combination of a High School diploma with technical training in welding, or an Associate’s degree in Welding Technology is preferable. Certification from a recognized welding institution is often required.
- Communication Skills: Strong verbal and written communication skills, with the ability to convey technical information effectively.
- Enthusiasm for Welding: A passion for the welding trade and a commitment to the development of skilled welders.
- Public Speaking: Comfortable with speaking to groups and providing interactive, engaging learning experiences.
- Adaptability: Ability to modify teaching methods and materials to suit different learning styles and skill levels.
Career Path and Growth:
This role offers the chance to shape the skills and careers of aspiring welders, contributing to the industry by training competent professionals.
With experience, Welding Instructors can progress to senior educational roles, develop specialized training programs, or transition into industry roles such as Welding Inspectors or Project Managers, leveraging their extensive knowledge and teaching experience.
Welding Sales Representative
Average Salary: $40,000 – $60,000 per year
Welding Sales Representatives are responsible for selling welding equipment, tools, and supplies to various clients, including fabrication shops, construction companies, and educational institutions.
This role is ideal for beginner welders who enjoy networking and understanding client needs to provide the best welding solutions.
Job Duties:
- Client Relationship Management: Establish and maintain relationships with current and prospective clients in the welding industry.
- Product Knowledge: Become an expert on welding products and their applications to effectively recommend solutions to clients.
- Sales Presentations: Deliver persuasive presentations and demonstrations to showcase the benefits and features of welding equipment.
- Customer Service: Address customer inquiries and concerns, ensuring a high level of satisfaction with both products and services.
- Market Research: Stay informed about industry trends, new technologies, and competitor products to provide up-to-date information to clients.
- Contract Negotiation: Work with clients to negotiate sales contracts that meet both parties’ needs.
Requirements:
- Educational Background: A certificate or associate degree in Welding Technology or a related field, along with a solid understanding of welding processes and equipment.
- Communication Skills: Strong verbal and written communication skills, with the ability to build relationships and persuade potential clients.
- Sales Acumen: A keen interest in sales, coupled with the ability to understand and meet client needs.
- Customer Service: A commitment to providing exceptional customer service and after-sales support.
- Technical Aptitude: Ability to grasp technical details and specifications of welding equipment and effectively communicate these to a non-technical audience.
Career Path and Growth:
As a Welding Sales Representative, you have the opportunity to directly influence the success and growth of your company through increased sales and client satisfaction.
With experience, you may advance to senior sales positions, become a sales manager, or specialize in sales for a particular type of welding technology or industry sector.
Career growth may also involve opportunities for international travel and sales if working for larger corporations with a global presence.
Pipe Welder
Average Salary: $40,000 – $70,000 per year
Pipe Welders are skilled tradespeople who specialize in welding pipes for various industries, including construction, manufacturing, and energy sectors.
This role is perfect for beginner welders who are seeking a challenging and rewarding career path that demands precision and safety.
Job Duties:
- Welding Pipes: Use various welding techniques to join metal pipes for plumbing, heating, and cooling systems or industrial projects.
- Reading Blueprints: Interpret technical drawings and plans to understand welding specifications and requirements.
- Ensuring Safety: Follow strict safety protocols to prevent accidents and ensure the structural integrity of the welded pipes.
- Maintaining Equipment: Keep welding tools and machinery in good working condition through regular maintenance.
- Quality Control: Inspect welds to ensure they meet relevant codes, standards, and specifications.
- Continued Learning: Stay up-to-date with advancements in welding techniques and materials.
Requirements:
- Educational Background: A high school diploma or GED, along with technical training or a welding certificate from a vocational school or community college.
- Technical Skills: Proficiency in various welding techniques, such as Shielded Metal Arc Welding (SMAW), Gas Tungsten Arc Welding (GTAW/TIG), and Gas Metal Arc Welding (GMAW/MIG).
- Physical Fitness: Good physical condition to handle heavy materials and work in different positions, sometimes in confined spaces.
- Attention to Detail: Precision and attention to detail to produce high-quality welds and prevent leaks or structural failures.
- Safety Awareness: Knowledge of and adherence to occupational safety and health regulations.
Career Path and Growth:
Starting as a Pipe Welder, there are numerous opportunities for advancement.
With experience and additional certification, welders can become welding inspectors, supervisors, or move into higher-paying specialty welding fields.
There is also the potential for self-employment or contract work, providing greater autonomy and the possibility of higher earnings.
Welder Fabricator
Average Salary: $35,000 – $60,000 per year
Welder Fabricators are skilled tradespeople who specialize in joining metal parts together through welding and fabricating metal structures and components.
This role is ideal for beginner welders who enjoy hands-on work and have a keen interest in metalwork and construction.
Job Duties:
- Reading Blueprints: Interpret technical drawings and blueprints to understand project specifications and requirements.
- Welding: Use various welding techniques to join metal parts together, ensuring strong and durable bonds.
- Fabricating Components: Cut, shape, and combine materials to fabricate metal structures or parts as per project needs.
- Finishing: Grind, polish, and finish welded surfaces to meet aesthetic and technical standards.
- Quality Control: Inspect completed welds and fabrications to ensure they meet safety standards and project specifications.
- Equipment Maintenance: Perform routine maintenance on welding equipment and machinery to ensure optimal performance.
Requirements:
- Educational Background: A high school diploma is required, with further education or certification in welding technology preferred.
- Technical Skills: Proficient in various welding techniques, including MIG, TIG, and stick welding, as well as knowledge of metallurgy.
- Attention to Detail: Ability to produce precise and accurate work that meets structural integrity and aesthetic standards.
- Physical Stamina: Comfortable with physically demanding tasks and able to work in various positions, such as kneeling or standing for extended periods.
- Safety Consciousness: Strict adherence to safety protocols and the use of personal protective equipment to prevent injuries and accidents.
Career Path and Growth:
Starting as a Welder Fabricator opens up numerous opportunities for career advancement.
With experience, individuals can specialize in complex welding techniques, become welding inspectors, or move into supervisory or project management roles.
Continuous learning and certification can lead to higher-paying positions and greater responsibility within the industry.
CNC Operator
Average Salary: $40,000 – $55,000 per year
CNC Operators handle the operation of computer numerical control (CNC) machines that cut, shape, and finish metal parts, often used in various engineering and manufacturing processes.
This role is ideal for beginner welders who possess a technical mindset and are interested in precision machining and the production side of the metalworking industry.
Job Duties:
- Setting Up CNC Machines: Prepare and operate CNC machinery for performing tasks such as drilling, grinding, milling, etc.
- Reading Blueprints: Understand and interpret technical blueprints and drawings to produce accurate work.
- Quality Control: Perform regular inspections of machined parts for quality and adherence to specifications.
- Maintenance: Conduct routine machine maintenance to ensure optimal functionality and performance.
- Troubleshooting: Diagnose and rectify issues with CNC machines to minimize downtime and maintain production schedules.
- Material Handling: Prepare, load, and unload materials and finished components, ensuring safe handling procedures.
Requirements:
- Educational Background: A high school diploma or equivalent is required; additional certification or training in CNC operation is highly beneficial.
- Technical Skills: Proficiency in operating CNC machinery and understanding G-code programming.
- Attention to Detail: Ability to focus on precise measurements and specifications for high-quality production.
- Mathematical Aptitude: Good understanding of basic math and geometry to interpret job requirements and blueprints.
- Physical Stamina: Capable of standing for long periods and managing heavy materials.
Career Path and Growth:
CNC Operators play a crucial role in modern manufacturing processes, providing a blend of technical knowledge and practical skills.
With experience, CNC Operators can advance to supervisory roles, become CNC programmers, or specialize in more complex machinery and production techniques.
The demand for skilled CNC Operators is expected to remain strong, with opportunities for career growth in various sectors of manufacturing and engineering.
Custom Motorcycle Welder
Average Salary: $40,000 – $60,000 per year
Custom Motorcycle Welders are skilled tradespeople who specialize in fabricating and repairing motorcycle frames, customizing bike components, and creating unique metal features for motorcycles.
This role is perfect for beginner welders who have a passion for motorbikes and a creative flair for metalwork.
Job Duties:
- Fabricating Motorcycle Frames: Design and construct durable and aesthetically pleasing motorcycle frames and components tailored to client specifications.
- Customizing Bike Components: Modify existing parts or create custom features that enhance the performance and style of the motorcycle.
- Repairing Metal Structures: Assess and repair damaged motorcycle frames and parts, ensuring structural integrity and safety.
- Collaborating with Designers: Work closely with motorcycle designers to bring conceptual drawings and ideas to life through expert welding and metalworking.
- Quality Control: Inspect and test welds and custom components to ensure they meet safety standards and client expectations.
- Staying Current with Trends: Keep up with the latest trends in motorcycle design and welding technology to offer cutting-edge services to customers.
Requirements:
- Technical Training: A diploma or certificate in welding technology, with a focus on techniques relevant to motorcycle fabrication.
- Hands-on Experience: Practical welding experience, preferably with a focus on automotive or motorcycle applications.
- Creative Skills: An artistic eye and the ability to translate creative ideas into functional and visually appealing motorcycle features.
- Attention to Detail: Precision and attention to detail are crucial for creating high-quality welds and custom components.
- Physical Stamina: Capable of handling the physical demands of welding, including working in various positions and handling heavy materials.
Career Path and Growth:
Starting as a Custom Motorcycle Welder opens up a specialized niche in the welding industry, with opportunities to develop a strong reputation for quality craftsmanship.
With experience, welders in this field can advance to lead welder positions, start their own custom welding shops, or become recognized artists within the motorcycle community.
Conclusion
And there you have it.
A comprehensive guide to the most exciting jobs for beginner welders.
With a wide array of options available, there’s indeed something for every fledgling welder out there.
So why wait? Begin your journey towards welding regularly today.
Remember: It’s NEVER too late to transform your budding interest in welding into a skilled profession.
The Prosperity Path: Exclusive Insights into 2025’s Highest Paying Jobs!
Unlock the List: Easy Yet Lucrative Careers You Can Start Now
Skyrocket Your Income from Home: Remote Jobs That Are Pure Gold!
Is Your Career on This List? Top Jobs with the Lowest Paychecks in 2025