30 Jobs For Fabricator Welder (Crafting Careers Here)
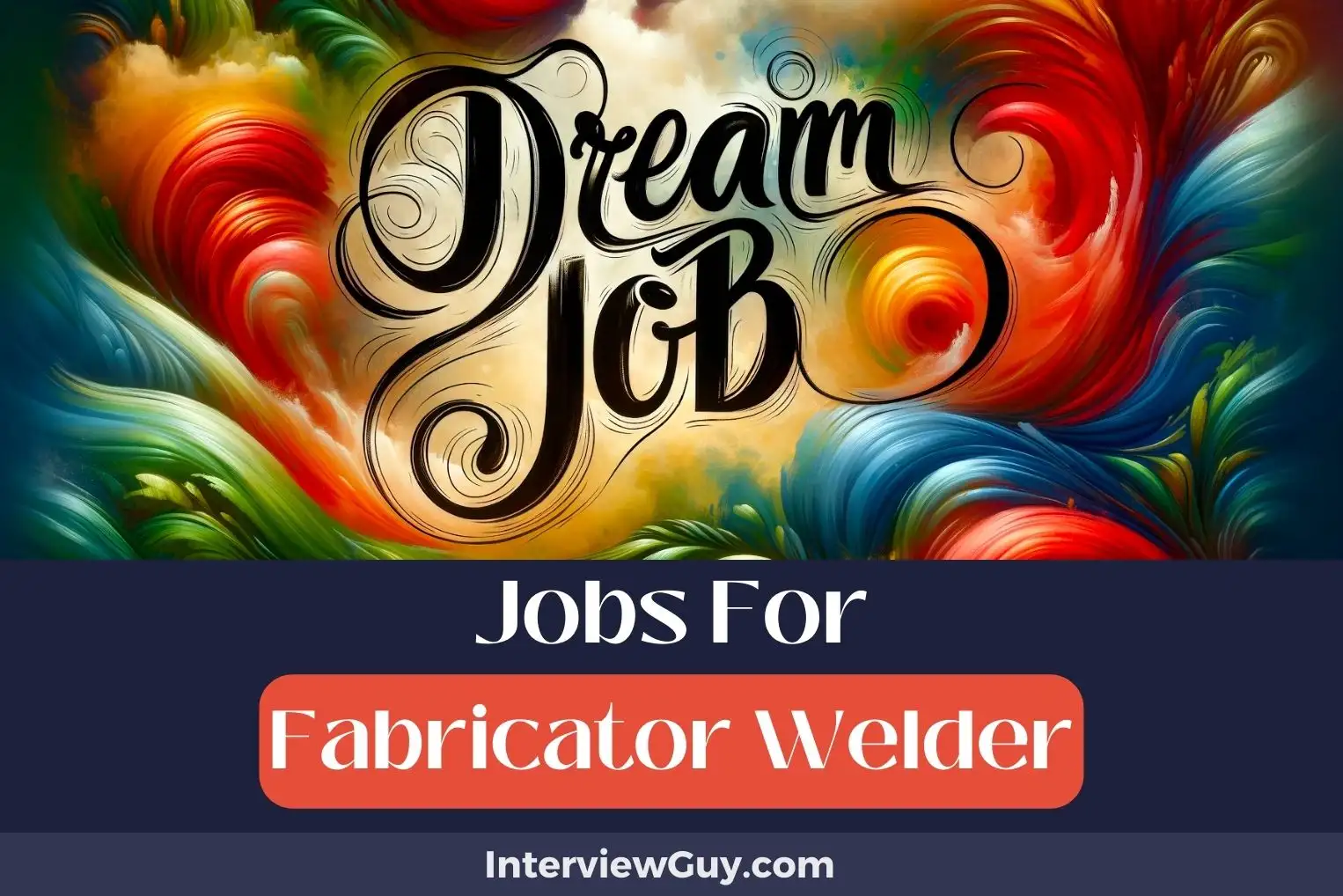
Are you a committed craftsman? Love spending your days working with steel?
Then, you’re in for a treat!
Today, we’re diving into a list of dream jobs for fabricator welders.
From pipe welders to structural metal fabricators. Each one, is a great fit for those who live and breathe this craft.
Imagine manipulating metal. Day in, day out.
Sounds like a dream, right?
So, prepare your workbench.
And get ready to discover your dream welding profession!
Welding Supervisor
Average Salary: $50,000 – $75,000 per year
Welding Supervisors oversee and coordinate the activities of welders, ensuring that all welding works meet quality standards and project specifications.
This role is ideal for Fabricator Welders who excel in leadership, have a keen eye for detail, and are passionate about maintaining high-quality craftsmanship.
Job Duties:
- Overseeing Welding Projects: Manage welding projects from start to finish, ensuring they are completed on time and within budget.
- Ensuring Quality Control: Inspect and verify the quality of welds, ensuring they meet industry standards and project requirements.
- Training and Development: Train new welders and provide ongoing development for existing staff to ensure high levels of technical skill and safety practices.
- Scheduling Work Shifts: Plan and schedule work shifts for welding teams to maximize productivity and meet project deadlines.
- Maintenance of Equipment: Ensure that all welding equipment is maintained in good working order and that safety protocols are followed.
- Implementing Safety Procedures: Enforce strict adherence to safety regulations to prevent accidents and injuries on the job.
Requirements:
- Educational Background: A high school diploma is required, with post-secondary training or an Associate’s degree in Welding Technology or a related field preferred.
- Experience: Several years of hands-on welding experience, as well as prior supervisory or management experience in a welding environment.
- Technical Skills: In-depth knowledge of welding techniques, materials, and equipment.
- Leadership: Strong leadership and team management skills are essential for coordinating and supervising the work of welding teams.
- Problem-Solving: Ability to quickly identify issues and implement practical solutions to keep projects on track.
- Certifications: Possession of relevant welding certifications, such as Certified Welding Supervisor (CWS) from the American Welding Society (AWS).
Career Path and Growth:
Welding Supervisors play a critical role in the fabrication and construction industries.
Their expertise ensures the structural integrity and safety of various projects.
With experience, Welding Supervisors can move up to higher management positions, such as Production Manager or Quality Control Manager, or specialize further in areas like underwater welding supervision or pipeline welding management.
Opportunities for career advancement also include roles in project management or starting their own welding contracting business.
Metal Fabrication Shop Manager
Average Salary: $50,000 – $75,000 per year
Metal Fabrication Shop Managers oversee operations in shops specializing in metalwork, where various metal parts are built and assembled.
This role is ideal for Fabricator Welders who are experienced in the industry and have a strong understanding of metalwork processes.
Job Duties:
- Managing Shop Operations: Supervise the daily activities of the fabrication shop, ensuring projects are completed on time and within budget.
- Quality Control: Oversee the quality of the work produced, ensuring it meets both internal standards and customer specifications.
- Team Leadership: Lead and motivate a team of fabricators and welders, providing guidance and technical expertise as needed.
- Project Planning: Coordinate with clients and other departments to plan and schedule projects, managing resources effectively.
- Health and Safety Compliance: Ensure that all shop activities comply with health and safety regulations to maintain a safe working environment.
- Continuous Improvement: Identify opportunities for process improvements and implement changes to increase efficiency and productivity.
Requirements:
- Educational Background: A degree or diploma in metal fabrication, welding technology, or a related field is often required.
- Experience in Metal Fabrication: Extensive experience in metal fabrication and welding, with a proven track record of managing a team.
- Leadership Skills: Strong leadership and people management skills, capable of directing and motivating a team.
- Technical Knowledge: In-depth knowledge of metal fabrication techniques, materials, and safety standards.
- Problem-solving Skills: Ability to quickly identify issues and develop effective solutions.
- Communication Skills: Excellent verbal and written communication skills for interacting with staff, clients, and suppliers.
Career Path and Growth:
This role offers the opportunity to lead and shape the operations of a metal fabrication shop.
With experience, Metal Fabrication Shop Managers can advance to higher management positions, open their own fabrication shops, or specialize in areas such as production management or process engineering.
Certified Welding Inspector (CWI)
Average Salary: $60,000 – $85,000 per year
Certified Welding Inspectors play a critical role in the construction and manufacturing industries by ensuring that welds are safe, compliant, and of high quality.
This role is ideal for fabricator welders who have a keen eye for detail and are passionate about upholding standards in welding practices.
Job Duties:
- Inspecting Welds: Examine welds to ensure they meet design requirements, codes, and standards.
- Reviewing Specifications and Drawings: Interpret blueprints and project specifications to determine weld requirements.
- Documentation and Reporting: Prepare inspection reports and maintain records of welding inspections and outcomes.
- Quality Assurance: Implement and monitor quality control procedures related to welding activities.
- Supervising Welding Processes: Oversee the welding process to ensure that all procedures are followed and that work is performed safely.
- Continuing Education: Stay updated on industry changes, new welding techniques, and advancements in inspection technologies.
Requirements:
- Educational Background: A high school diploma or equivalent; additional training or coursework in welding technology or metallurgy is beneficial.
- Certification: Certification as a CWI from a recognized body such as the American Welding Society (AWS).
- Technical Skills: Proficient in reading blueprints and a thorough understanding of welding processes and standards.
- Attention to Detail: Ability to detect flaws and inconsistencies in welds that could lead to structural failures.
- Communication Skills: Strong written and verbal communication skills for report writing and collaborating with welding and engineering teams.
- Physical Stamina: Capability to work in various environments and to stand, bend, or stoop for long periods.
Career Path and Growth:
As a CWI, you will be an essential part of ensuring safety and quality in projects ranging from infrastructure to aerospace.
With experience, a CWI can advance to senior inspector roles, specialize in specific welding methods or materials, become a welding educator, or move into management positions overseeing welding operations and quality assurance programs.
Underwater Welder
Average Salary: $54,000 – $93,000 per year
Underwater welders play a critical role in maintaining and repairing structures below the water’s surface, such as oil rigs, pipelines, and ship hulls.
This role is ideal for Fabricator Welders who love the challenge of combining their welding expertise with diving skills in underwater environments.
Job Duties:
- Performing Underwater Welding: Execute welding tasks underwater using specialized equipment and techniques to join or repair metal structures.
- Inspection and Repair: Conduct inspections of underwater structures to assess damage and perform necessary repairs or maintenance.
- Diving Operations: Prepare and operate diving equipment, ensuring adherence to safety protocols while submerged.
- Project Planning: Collaborate with engineers and other professionals to plan underwater welding projects, including risk assessments and method statements.
- Equipment Maintenance: Regularly inspect and maintain welding and diving gear to ensure optimal performance and safety.
- Staying Certified: Maintain up-to-date certification in underwater welding and commercial diving, including keeping abreast of industry standards and practices.
Requirements:
- Technical Skills: Proficiency in welding techniques and familiarity with diving equipment and underwater operations.
- Certifications: Certification in commercial diving and a recognized underwater welding credential are required.
- Physical Fitness: Excellent health and physical condition to manage the demanding nature of underwater work.
- Problem-solving Skills: Ability to think critically and solve complex problems while working in a challenging underwater environment.
- Adaptability: Comfortable working in various underwater conditions and able to adjust techniques accordingly.
Career Path and Growth:
Underwater welding is a specialized field that offers unique opportunities for personal and professional growth.
With experience, underwater welders can advance to supervisory or project management roles, specialize in hyperbaric welding technology, or transition into underwater welding instruction and training.
Pipeline Welder
Average Salary: $58,000 – $110,000 per year
Pipeline Welders are skilled tradespeople who specialize in welding metal pieces together for the construction and maintenance of pipeline systems.
This role is perfect for Fabricator Welders who excel in precision work and enjoy the challenge of constructing vital infrastructure.
Job Duties:
- Welding Pipeline Sections: Perform high-quality welding to join pipeline sections, ensuring the integrity and strength of the pipeline network.
- Following Safety Protocols: Adhere to strict safety guidelines to prevent accidents and ensure the safety of the welding team and the environment.
- Inspecting Welds: Conduct thorough inspections of welds to check for defects and to ensure compliance with industry standards.
- Using Specialized Equipment: Operate advanced welding equipment designed for pipeline construction, maintenance, and repair.
- Maintaining Equipment: Keep welding tools and machinery in good working order, performing regular maintenance and repairs as needed.
- Staying Updated: Continually update skills and knowledge regarding welding techniques, safety regulations, and new materials in the field.
Requirements:
- Technical Training: A certificate or diploma in welding from a vocational school or community college, with specific training in pipeline welding techniques.
- Physical Stamina: Ability to perform physically demanding tasks in various weather conditions and environments.
- Attention to Detail: Keen eye for detail to produce clean, strong welds and to identify any potential issues before they become problems.
- Certifications: Possession of relevant welding certifications, such as the American Welding Society (AWS) certification, is often required.
- Safety Consciousness: A strong commitment to safety practices to protect oneself and colleagues in potentially hazardous work situations.
Career Path and Growth:
Pipeline Welders play a crucial role in the construction and maintenance of energy infrastructure, making the position highly valuable.
With experience, welders can advance to supervisory roles, become welding inspectors, or specialize further in underwater and custom welding.
The demand for skilled Pipeline Welders is expected to remain strong, offering opportunities for stable employment and good earning potential.
Welding Instructor
Average Salary: $45,000 – $70,000 per year
Welding Instructors train and educate aspiring welders in a variety of settings, including vocational schools, community colleges, and private welding schools.
This role is perfect for Fabricator Welders who are passionate about their craft and eager to impart their knowledge and skills to the next generation of industry professionals.
Job Duties:
- Teaching Welding Techniques: Instruct students on various welding methods, safety protocols, and best practices in the trade.
- Curriculum Development: Develop and update course materials, including syllabi, lesson plans, and practical demonstrations to meet industry standards.
- Hands-On Training: Supervise and guide students through hands-on welding exercises, ensuring proper technique and adherence to safety regulations.
- Assessing Student Progress: Evaluate student performance through practical assessments, written exams, and project work.
- Industry Collaboration: Work with local businesses and industry leaders to align curriculum with current workforce needs and facilitate student job placements.
- Continuing Education: Stay abreast of the latest welding technologies, certifications, and industry trends to provide students with current knowledge and skills.
Requirements:
- Educational Background: A combination of formal education in Welding Technology or a related field and hands-on welding experience is essential.
- Certification: Holding professional welding certifications (such as AWS Certified Welding Instructor) is highly beneficial.
- Communication Skills: Strong verbal and written communication skills, with the ability to explain complex technical concepts in a clear and accessible manner.
- Passion for Teaching: A genuine interest in educating and training others, with a patient and encouraging approach to teaching.
- Technical Proficiency: Expert knowledge of welding processes, materials, and safety standards.
Career Path and Growth:
As a Welding Instructor, you have the opportunity to shape the future of the welding industry by training skilled professionals.
With experience, instructors can advance to lead educational programs, become department heads, or specialize in advanced welding technologies.
There is also the potential to author textbooks, develop online courses, and participate in industry conferences and workshops.
Structural Ironworker
Average Salary: $40,000 – $70,000 per year
Structural Ironworkers are the backbone of the construction industry, specializing in the installation and the welding of steel frameworks for buildings, bridges, and other structures.
This role is ideal for Fabricator Welders who have a keen interest in creating the skeletons of infrastructures and enjoy hands-on work at heights.
Job Duties:
- Erecting Steel Frameworks: Install and secure steel beams, girders, and columns to form the structural framework of various constructions.
- Welding and Fabrication: Perform welding tasks to join structural steel components, following safety protocols and blueprints accurately.
- Reading Blueprints: Interpret construction drawings and specifications to determine the layout and required materials for a project.
- Rigging and Hoisting: Set up cables, ropes, pulleys, and winches to lift and place structural components.
- Reinforcing Structures: Install and tie rebar and other reinforcing materials to strengthen concrete structures.
- Ensuring Safety: Adhere to strict safety guidelines to prevent accidents on construction sites, including the proper use of personal protective equipment.
Requirements:
- Technical Skills: Proficiency in welding and fabrication, with an understanding of metallurgy and construction techniques.
- Physical Fitness: Good physical condition to handle heavy materials and work at heights for extended periods.
- Attention to Detail: Ability to follow blueprints and instructions with precision to ensure the integrity of the structure.
- Teamwork: Willingness to work closely with other construction professionals, including engineers, crane operators, and other tradespeople.
- Problem-Solving: Aptitude for quickly addressing and resolving issues that may arise during the construction process.
Career Path and Growth:
Structural Ironworkers have the opportunity to take on more complex projects as they gain experience.
With additional training and certification, they can advance to supervisory roles, such as foreman or superintendent, or specialize further in areas like welding inspection or project management.
Some may even choose to run their own contracting businesses.
Boilermaker
Average Salary: $40,000 – $70,000 per year
Boilermakers are skilled tradespeople who fabricate, install, and maintain boilers, tanks, and other large vessels that hold liquids and gases.
This role is ideal for Fabricator Welders who enjoy hands-on work and have a keen interest in the construction and maintenance of high-pressure systems.
Job Duties:
- Constructing and Assembling Boiler Systems: Use blueprints and other technical documents to build or assemble boiler parts, ensuring proper installation and functionality.
- Performing Maintenance and Repairs: Conduct routine checks and maintenance on boiler systems, identifying issues and making necessary repairs to prevent breakdowns and ensure safety.
- Welding and Fabricating: Apply welding techniques to join or repair boiler components, using a variety of tools and equipment.
- Inspecting and Testing: Examine boilers and pressure vessels for defects or leaks, testing systems to ensure they meet safety standards and regulations.
- Following Safety Protocols: Adhere to strict safety guidelines and procedures to prevent accidents and ensure a safe working environment.
- Updating Skills: Stay current with welding techniques, safety protocols, and industry standards related to boiler making and fabrication.
Requirements:
- Educational Background: A high school diploma or equivalent, with technical training or an apprenticeship in boilermaking or a related field.
- Technical Skills: Proficient in welding and fabrication techniques, with knowledge of different types of metals and materials used in boiler construction.
- Attention to Detail: Ability to follow precise instructions and pay close attention to detail to ensure the safety and integrity of boiler systems.
- Physical Stamina: Comfortable with physically demanding tasks, including lifting heavy objects, climbing ladders, and working in confined spaces.
- Safety Consciousness: A strong commitment to safety protocols, understanding the importance of protective gear and safe work practices.
Career Path and Growth:
Boilermakers have the opportunity to work on a variety of projects across different industries, such as construction, manufacturing, and energy.
With experience, Boilermakers can advance to supervisory positions, become inspectors, or specialize in custom fabrication work.
Continuous learning and certification in advanced welding techniques can also lead to higher pay and greater job opportunities.
Aerospace Welder
Average Salary: $45,000 – $65,000 per year
Aerospace Welders play a crucial role in the fabrication and repair of aircraft and spacecraft components.
Using precision welding techniques, they ensure the structural integrity and safety of flight vehicles.
This role is ideal for fabricator welders with an interest in aeronautics and space exploration, as it provides an opportunity to contribute directly to the aerospace industry.
Job Duties:
- Performing Precision Welding: Execute detailed welding operations on aerospace components, adhering to strict industry standards and specifications.
- Inspection and Testing: Conduct thorough inspections and non-destructive testing of welds to guarantee that they meet quality and safety requirements.
- Reading Blueprints: Accurately interpret engineering drawings and blueprints to determine the precise specifications for welding projects.
- Maintenance and Repair: Carry out maintenance and repair work on existing aerospace structures, ensuring their longevity and reliability.
- Fabrication: Assist in the fabrication of new aerospace parts, employing advanced welding techniques suitable for high-stress environments.
- Staying Current with Technology: Keep up-to-date with the latest welding technologies and materials used in the aerospace industry.
Requirements:
- Educational Background: A high school diploma or equivalent; formal training through a vocational school, technical college, or apprenticeship is highly preferred.
- Certifications: Certification in welding, with specific endorsements for aerospace applications is often required.
- Technical Skills: Proficiency in a variety of welding techniques, including TIG (Tungsten Inert Gas), MIG (Metal Inert Gas), and arc welding, as applicable to aerospace materials like aluminum and titanium.
- Attention to Detail: Exceptional attention to detail to perform precise and clean welds that meet safety and quality standards.
- Physical Dexterity: Good hand-eye coordination and manual dexterity to handle complex welding tasks.
- Safety Consciousness: A strong commitment to safety protocols to ensure a safe work environment.
Career Path and Growth:
The role of an Aerospace Welder provides a pathway to specialized positions within the field, with potential for advancement to supervisory or inspection roles.
With experience and additional certifications, Aerospace Welders can become welding engineers, quality control inspectors, or move into managerial positions overseeing fabrication projects.
The growth in the aerospace industry, including commercial spaceflight, ensures a dynamic career with opportunities for continuous learning and contribution to cutting-edge aerospace technology.
Custom Metal Fabricator
Average Salary: $40,000 – $60,000 per year
Custom Metal Fabricators craft and construct metal parts and structures by cutting, bending, and assembling processes.
They work on a range of projects from custom automotive parts to bespoke architectural metalwork.
This role is ideal for Fabricator Welders who enjoy working with their hands, have an eye for detail, and take pride in creating unique metal pieces.
Job Duties:
- Interpreting Blueprints: Read and understand complex engineering drawings and specifications to craft metal structures and components accurately.
- Material Handling: Select and manage materials required for the project, ensuring compatibility and quality.
- Welding and Assembly: Utilize various welding techniques to join metal parts together, ensuring structural integrity and aesthetics.
- Custom Fabrication: Create bespoke metal products tailored to client specifications, which may include decorative pieces, custom machinery parts, or architectural elements.
- Finishing: Perform finishing operations such as grinding, polishing, and painting to achieve a professional and functional final product.
- Quality Control: Inspect completed items for quality and adherence to specifications, making adjustments as necessary to meet high standards.
Requirements:
- Technical Skills: Proficiency in welding and metal fabrication techniques, as well as the ability to operate relevant machinery and tools.
- Attention to Detail: Precision in measuring, cutting, and assembling to ensure that each product meets design requirements.
- Problem-Solving: Ability to troubleshoot issues that arise during the fabrication process and devise effective solutions.
- Physical Stamina: Capable of handling heavy materials and standing for long periods.
- Creativity: A creative mindset that can envision and execute unique custom fabrications.
Career Path and Growth:
As a Custom Metal Fabricator, there is the potential to specialize in areas such as artistic metalwork, precision machining, or aerospace fabrication.
With experience, one can move into supervisory roles, start their own custom fabrication business, or work as a consultant for complex projects requiring expert skill in metal fabrication.
Car Restoration Welder
Average Salary: $40,000 – $60,000 per year
Car Restoration Welders are skilled tradespeople who specialize in the art of restoring classic and vintage vehicles to their former glory through expert welding and metalwork.
This role is ideal for Fabricator Welders who have a passion for automobiles and take pride in bringing a piece of automotive history back to life.
Job Duties:
- Assessing Vehicle Condition: Examine the structural integrity of classic cars and determine the extent of metal repair or replacement needed.
- Performing Precision Welding: Carry out high-quality welding work to repair or replace damaged panels, frames, and other car parts.
- Fabricating Parts: Create custom parts and components that are no longer available, matching original specifications for a seamless restoration.
- Restoration Planning: Collaborate with restoration teams to plan the welding tasks in line with the restoration project’s timeline and goals.
- Quality Control: Ensure all welding work meets high standards of strength, durability, and appearance, adhering to safety and restoration guidelines.
- Staying Updated: Keep up-to-date with welding techniques, tools, and materials that can benefit car restoration projects.
Requirements:
- Technical Skills: Proficiency in various welding techniques, such as MIG, TIG, and gas welding, with a focus on thin-gauge metals often found in classic cars.
- Experience: Hands-on experience in automotive welding and a strong understanding of car bodywork and chassis structures.
- Attention to Detail: Exceptional attention to detail to ensure that restorations are accurate and aesthetically pleasing.
- Problem-Solving: Ability to troubleshoot and creatively solve problems that may arise during the restoration process.
- Passion for Cars: A strong interest in classic and vintage cars, with a dedication to preserving automotive heritage.
Career Path and Growth:
Car Restoration Welders have the opportunity to work on a variety of unique and rare vehicles, each presenting its own set of challenges and rewards.
With experience, Car Restoration Welders can advance to lead roles within a restoration team, open their own restoration workshops, or specialize in high-demand areas like custom fabrication or luxury vehicle restoration.
Welding Engineer
Average Salary: $65,000 – $100,000 per year
Welding Engineers specialize in designing, implementing, and improving welding methods and procedures in various industries such as automotive, aerospace, manufacturing, and construction.
This role is ideal for Fabricator Welders who are interested in advancing their technical skills and knowledge in welding processes and metallurgy.
Job Duties:
- Developing Welding Procedures: Create and standardize welding procedures to ensure quality and efficiency in fabrication and construction projects.
- Welding Process Optimization: Analyze current welding processes and recommend improvements to increase productivity and reduce costs.
- Quality Control: Oversee the quality of welds, ensuring they meet industry standards and project specifications.
- Material Selection: Advise on the selection of appropriate materials and welding methods for specific projects.
- Project Management: Coordinate with project managers, engineers, and fabricators to ensure welding work is completed on schedule and within budget.
- Staying Informed: Keep up-to-date with the latest welding technologies, materials, and safety regulations.
Requirements:
- Educational Background: A Bachelor’s degree in Welding Engineering, Materials Science, Mechanical Engineering, or a related field is required.
- Technical Skills: Strong understanding of welding techniques, metallurgy, and engineering principles.
- Problem-Solving: Ability to troubleshoot welding issues and develop innovative solutions.
- Communication Skills: Effective verbal and written communication skills to liaise with team members and document procedures.
- Attention to Detail: Keen eye for detail to ensure high-quality welds and adherence to specifications.
Career Path and Growth:
As a Welding Engineer, there is significant potential for career growth.
With experience, individuals can move into higher managerial or supervisory roles, overseeing larger projects or multiple teams.
There are also opportunities to specialize further in areas such as robotics, non-destructive testing (NDT), or to become a consultant offering expert advice on complex welding challenges.
Sheet Metal Worker
Average Salary: $40,000 – $60,000 per year
Sheet Metal Workers are skilled tradespeople who fabricate, install, and repair sheet metal products, such as ducts for heating and air conditioning systems, roofing, and siding.
This role is ideal for Fabricator Welders who take pride in precision and craftsmanship in working with metal materials.
Job Duties:
- Fabricating Metal Products: Use specialized tools and machinery to cut, bend, and shape sheet metal according to project specifications.
- Installing HVAC Systems: Assemble and install ductwork for heating, ventilation, and air conditioning systems in residential and commercial buildings.
- Repairing Metal Structures: Perform maintenance and repairs on existing metal structures, ensuring they meet safety and quality standards.
- Reading Blueprints: Interpret technical drawings and plans to understand project requirements and measurements.
- Welding and Joining Metal: Apply welding techniques to join metal parts together securely.
- Ensuring Safety Compliance: Adhere to all safety protocols and regulations to prevent accidents and injuries on the job site.
Requirements:
- Educational Background: A high school diploma or equivalent, with technical training in sheet metal work from a vocational school or apprenticeship program.
- Technical Skills: Proficiency in using hand tools, power tools, and metalworking equipment.
- Physical Fitness: Good physical condition to handle heavy materials and stand for long periods.
- Attention to Detail: Precision in measuring, cutting, and installing to ensure high-quality work and fit.
- Problem-Solving: Ability to troubleshoot and resolve issues that arise during fabrication or installation.
Career Path and Growth:
Sheet Metal Workers have the opportunity to advance to supervisory roles, such as foreman or project manager, with experience.
They may also specialize in a particular area of sheet metal work, such as fabrication, installation, or maintenance, or start their own contracting business.
Continuous learning and certification in new technologies and methods can further enhance career prospects.
Industrial Maintenance Welder
Average Salary: $40,000 – $60,000 per year
Industrial Maintenance Welders play a crucial role in maintaining and repairing a variety of industrial machinery and infrastructure.
This role is ideal for Fabricator Welders who take pride in ensuring that the foundation of our industrial world remains strong and functional.
Job Duties:
- Performing Welding Repairs: Execute a range of welding tasks to repair broken or worn-out industrial equipment and metal structures.
- Following Safety Protocols: Adhere strictly to safety guidelines and procedures to prevent accidents and ensure a safe working environment.
- Reading Blueprints: Interpret technical drawings and blueprints to understand repair requirements and specifications.
- Maintenance Checks: Conduct routine inspections of machinery and infrastructure to identify areas in need of maintenance or repair.
- Fabricating Parts: Use welding and fabricating skills to create replacement parts or enhance existing machinery for improved performance.
- Staying Updated with Techniques: Keep abreast of the latest welding techniques, materials, and equipment to ensure efficient and effective repairs.
Requirements:
- Educational Background: A high school diploma or equivalent, with a certification in welding from a reputable institution.
- Technical Skills: Proficiency in various welding techniques, including MIG, TIG, and stick welding, as well as a good understanding of metallurgy.
- Experience in Maintenance: Prior experience in industrial maintenance or a related field is highly valuable.
- Physical Stamina: Capable of performing physically demanding tasks and working in various environments, including confined spaces and heights.
- Problem-Solving: Ability to quickly identify issues and determine the best course of action for repairs.
Career Path and Growth:
Industrial Maintenance Welders are essential for the longevity and efficiency of industrial operations.
With experience, welders in this field can advance to supervisory roles, specialize in specific types of welding for high-demand industries, or become welding inspectors to ensure the quality and safety of welds across various projects.
Welder Fitter
Average Salary: $40,000 – $60,000 per year
Welder Fitters are skilled craftsmen who read blueprints and use a variety of welding techniques to join metal parts in the construction of structures, machinery, and equipment.
This role is ideal for individuals with a passion for hands-on fabrication and an interest in creating strong, durable structures.
Job Duties:
- Interpreting Blueprints: Understand and follow detailed instructions from blueprints and technical drawings to determine the materials required and the sequence of welding operations.
- Welding and Fabrication: Use various welding methods such as MIG, TIG, stick, and flux-cored welding to join metal parts together according to specifications.
- Assessing Materials and Equipment: Select appropriate materials and welding equipment for the task at hand, ensuring quality and efficiency in the welding process.
- Ensuring Precision: Carefully measure and align workpieces using straightedges, rulers, and calipers to ensure precise fitting and welding.
- Inspecting Welds: Examine welds for bead size and other specifications, making adjustments as necessary to meet quality standards.
- Maintenance and Safety: Perform regular maintenance on welding equipment and adhere to strict safety guidelines to prevent accidents.
Requirements:
- Educational Background: A high school diploma or equivalent; technical training or certification in welding is highly beneficial.
- Technical Skills: Proficiency in various welding techniques and the ability to read and interpret blueprints and technical drawings.
- Physical Stamina: Good physical condition to handle long hours of standing, bending, and lifting heavy materials.
- Attention to Detail: Precision and attention to detail to produce clean and high-quality welds.
- Problem-Solving: The ability to troubleshoot issues that arise during the welding process and to adapt techniques as necessary.
Career Path and Growth:
As a Welder Fitter, you have the opportunity to work on a diverse range of projects across different industries, such as construction, manufacturing, and automotive.
With experience, you can specialize in advanced welding techniques, take on supervisory roles, or start your own welding business.
Continuous learning and certification can lead to higher-paying positions and greater job security in this in-demand field.
Metal Artist Sculptor
Average Salary: $30,000 – $60,000 per year
Metal Artist Sculptors create intricate and expressive works of art using various metals and welding techniques.
This role is ideal for Fabricator Welders who have a passion for art and design and enjoy transforming raw materials into stunning sculptures.
Job Duties:
- Designing Sculptures: Conceptualize and sketch designs for metal sculptures, often combining artistic vision with the physical properties of metal.
- Fabricating Metal Art: Use welding and fabrication techniques to bring designs to life, paying close attention to detail and craftsmanship.
- Finishing Art Pieces: Employ various methods such as grinding, polishing, and patination to complete sculptures, achieving the desired aesthetic effect.
- Restoration Work: Repair and restore old or damaged metal artworks, maintaining or enhancing their historical and aesthetic value.
- Exhibiting Artwork: Prepare and present sculptures for exhibitions, galleries, or private collections, including installation and display considerations.
- Continual Learning: Stay current with trends in art and fabrication techniques to refine skills and expand artistic capabilities.
Requirements:
- Artistic Talent: A natural ability for art and creativity, with a portfolio that showcases original works and metal sculpture proficiency.
- Technical Skills: Proficiency in welding and metal fabrication techniques, as well as familiarity with various tools and equipment used in metal artistry.
- Attention to Detail: A meticulous approach to the creation and finishing of sculptures, ensuring high-quality and durable artworks.
- Physical Stamina: The capacity to undertake physical labor for extended periods, often involving heavy lifting and operating machinery.
- Problem-Solving: The ability to troubleshoot and resolve issues related to design execution and material limitations.
Career Path and Growth:
Metal Artist Sculptors have the opportunity to gain recognition and build a reputation through their unique creations.
With experience and a growing portfolio, artists can establish their own studios, receive commissions for public art installations, collaborate with architects and designers, or teach their craft to aspiring metal sculptors.
Motorsports Welding Technician
Average Salary: $40,000 – $65,000 per year
Motorsports Welding Technicians are specialized fabricators who apply their welding skills in the fast-paced world of auto racing.
They work with a variety of metals to create and repair race car components, ensuring peak performance and safety on the track.
This role is perfect for Fabricator Welders who are passionate about motorsports and excel in a high-octane environment.
Job Duties:
- Custom Fabrication: Design and construct bespoke parts for racing vehicles, including chassis, roll cages, and exhaust systems.
- Repair Work: Perform precise and durable repairs on damaged race car components, often under tight deadlines.
- Metalwork Proficiency: Demonstrate expertise in working with a range of metals and materials unique to motorsports applications.
- Technical Drawing Interpretation: Accurately read and understand engineering drawings and specifications to fabricate or modify parts as required.
- On-Site Support: Provide on-site welding support during race events, ensuring quick and effective solutions to any structural issues.
- Quality Assurance: Maintain high standards of craftsmanship to ensure safety and compliance with racing regulations.
Requirements:
- Technical Education: A vocational diploma or certificate in welding technology, with a focus on the specific materials used in motorsports.
- Welding Certifications: Industry-recognized certifications in welding processes commonly used in the racing industry, such as TIG and MIG welding.
- Experience in Fabrication: Hands-on experience in metal fabrication, preferably within the motorsports or high-performance automotive sectors.
- Precision and Attention to Detail: Ability to perform detailed and precise welds that meet the exacting standards of motorsports engineering.
- Adaptability: Willingness to work flexible hours, including weekends and travel to race events, as required.
Career Path and Growth:
For those with a love for racing and a talent for welding, a career as a Motorsports Welding Technician offers exciting opportunities.
Professionals in this field can advance to lead technician roles, supervise teams, or specialize in a particular type of racing vehicle.
With a strong reputation, some may even start their own fabrication shops catering to custom racing applications or progress into engineering roles within motorsports teams.
Welding Sales Representative
Average Salary: $40,000 – $60,000 per year
Welding Sales Representatives are experts in selling welding equipment, supplies, and services to businesses and individual clients.
This role is ideal for Fabricator Welders who are knowledgeable about welding processes and enjoy leveraging their expertise to drive sales and provide customer solutions.
Job Duties:
- Product Knowledge: Maintain in-depth understanding of welding equipment, materials, and accessories to recommend the best solutions for customer needs.
- Client Relationship Management: Build and nurture long-term relationships with clients, providing them with exceptional service and support.
- Developing Sales Strategies: Identify potential sales opportunities and develop strategies to engage new customers and markets.
- Conducting Demonstrations: Perform product demonstrations to showcase the benefits and features of various welding products.
- Technical Support: Assist customers with technical inquiries and provide guidance on the proper use and maintenance of welding equipment.
- Staying Updated: Keep abreast of the latest trends and advancements in welding technology to offer current and relevant solutions.
Requirements:
- Technical Background: A solid background in welding or a related technical field is highly beneficial.
- Sales Experience: Proven experience in sales, with the ability to close deals and meet sales targets.
- Communication Skills: Strong interpersonal and communication skills, capable of effectively articulating product benefits and features.
- Customer Service: A dedication to providing high-quality customer service and building lasting relationships with clients.
- Problem-Solving: Ability to assess customer needs and offer appropriate solutions, troubleshooting any issues that arise.
Career Path and Growth:
As a Welding Sales Representative, there is potential for career growth in various directions.
With successful sales performance and extensive industry knowledge, representatives can advance to higher-level sales management positions, become specialists in a particular welding technology, or transition into roles that influence product development and innovation within the welding industry.
Nuclear Welder
Average Salary: $60,000 – $90,000 per year
Nuclear Welders are highly skilled professionals who specialize in welding materials within nuclear power plants and other facilities dealing with radioactive materials.
This role is ideal for Fabricator Welders who are interested in a challenging and rewarding field that requires precision and a commitment to safety.
Job Duties:
- Performing Specialized Welding Tasks: Execute precise welding techniques to maintain and repair nuclear facility components, ensuring the integrity of critical structures.
- Maintaining Safety Standards: Adhere to stringent safety protocols to protect oneself and others from radiation exposure and to ensure the safe operation of the facility.
- Inspecting Welds: Use advanced non-destructive testing methods to inspect welds for faults that could lead to failures in a high-risk environment.
- Following Technical Plans: Interpret and follow detailed blueprints and technical plans specific to nuclear industry requirements.
- Emergency Response: Be prepared to respond to welding emergencies, which may involve quick decision-making and action to prevent or mitigate incidents.
- Continual Learning: Stay updated on the latest welding technologies, materials, and safety procedures in the nuclear industry.
Requirements:
- Educational Background: A high school diploma or equivalent, along with specialized training in welding. Additional certification in nuclear welding is highly beneficial.
- Technical Skills: Proficiency in various welding techniques, including TIG (Tungsten Inert Gas) and MIG (Metal Inert Gas) welding, with a strong understanding of metallurgy.
- Safety Consciousness: A deep understanding of and strict adherence to safety protocols, radiation protection standards, and emergency procedures.
- Attention to Detail: Ability to perform precise and high-quality welds that meet the demands of nuclear industry standards.
- Physical Stamina: Capable of performing physically demanding tasks, including working in confined spaces and wearing protective gear for extended periods.
Career Path and Growth:
Nuclear Welders play a critical role in maintaining the safety and efficiency of nuclear facilities.
With experience, they can advance to supervisory positions, become welding inspectors, or specialize further in advanced welding technologies.
Their skills are also transferable to other industries that require high precision welding, such as aerospace or military defense.
Robotic Welding Technician
Average Salary: $45,000 – $65,000 per year
Robotic Welding Technicians operate and maintain robotic welding systems used in manufacturing and fabrication settings.
This role is perfect for Fabricator Welders who have an interest in technology and automation and wish to advance their careers in the cutting-edge field of robotic welding.
Job Duties:
- Programming and Operating Robotic Systems: Set up and operate robotic welding machines, ensuring precision and adherence to specifications.
- Maintenance and Troubleshooting: Perform regular maintenance on welding robots and troubleshoot any technical issues that arise to minimize downtime.
- Quality Control: Inspect welded components to ensure they meet quality standards and make adjustments to robotic systems as necessary.
- Collaborating with Engineering Teams: Work closely with engineers and technicians to optimize welding procedures and implement new fabrication methods.
- Training and Supervision: Provide guidance and training to other technicians on robotic welding techniques and safety protocols.
- Staying Current with Technology: Keep up-to-date with advancements in robotic welding technology and apply new methods to improve production efficiency.
Requirements:
- Technical Qualifications: A degree or certificate in Welding Technology, Robotics, or a related technical field is often required.
- Hands-on Experience: Practical experience with welding equipment and robotic systems is highly beneficial.
- Technical Skills: Proficiency in reading blueprints, understanding welding symbols, and programming robotic welding machines.
- Attention to Detail: A keen eye for detail to ensure high-quality welds and adherence to safety standards.
- Problem-solving Abilities: Aptitude for identifying and solving mechanical and technical issues that may arise during the welding process.
Career Path and Growth:
As a Robotic Welding Technician, you’ll be at the forefront of manufacturing technology.
There are opportunities to advance into supervisory roles, specialize in programming and development of robotic systems, or move into engineering positions.
Continuous learning and certification in new technologies can further enhance career prospects and lead to higher-level positions within the industry.
Industrial Pipe Fitter
Average Salary: $45,000 – $65,000 per year
Industrial Pipe Fitters are skilled tradespeople who specialize in the installation, assembly, fabrication, maintenance, and repair of mechanical piping systems.
This role is ideal for Fabricator Welders who excel in precision and have an interest in contributing to the infrastructure of various industries such as oil and gas, manufacturing, and power generation.
Job Duties:
- Interpreting Blueprints: Read and understand complex blueprints and diagrams to determine the specifications for the piping systems.
- Fabricating Pipe Systems: Use a variety of tools and equipment to cut, thread, and weld pipes according to project specifications.
- Installing Piping: Assemble and secure pipes, tubes, fittings, and related equipment, according to plans and by applying knowledge of system operation.
- Maintenance and Repair: Perform routine maintenance and respond to emergency repairs on industrial piping systems.
- Ensuring Compliance: Ensure all installations and repairs meet code requirements and safety standards.
- Collaboration: Work closely with other tradespeople, such as steamfitters, plumbers, and project managers, to coordinate project completion.
Requirements:
- Technical Education: A high school diploma with technical training or an associate degree in a field such as welding technology or pipefitting.
- Trade Certification: Certification or apprenticeship in pipefitting or welding is highly regarded.
- Physical Dexterity: Good hand-eye coordination and physical fitness to handle heavy materials and stand for long periods.
- Detail-Oriented: Keen attention to detail to ensure precision in measurements and cuts.
- Safety Conscious: Knowledge of safety standards and a strong commitment to working safely.
- Problem-Solving Skills: Ability to troubleshoot and solve issues that may arise during the fitting process.
Career Path and Growth:
As an Industrial Pipe Fitter, you play a critical role in keeping vital systems operational across various industries.
With experience, you can advance to supervisory roles, specialize in a particular type of piping system, or become a project manager overseeing large-scale installations.
There are also opportunities for ongoing education and certification to stay current with technological advancements in the field.
Custom Auto Fabricator
Average Salary: $40,000 – $70,000 per year
Custom Auto Fabricators are skilled tradespeople who specialize in designing, fabricating, and customizing unique automotive parts and vehicles.
This role is perfect for individuals with a passion for cars, creativity, and hands-on craftsmanship, especially those who love to transform ordinary vehicles into extraordinary machines.
Job Duties:
- Designing Custom Parts: Create original designs for custom automotive parts or modifications, taking clients’ vision and vehicle specifications into account.
- Fabricating Automotive Components: Use various tools and techniques to fabricate and weld custom parts, ensuring they meet safety and quality standards.
- Modifying Vehicles: Perform structural modifications to vehicles, including bodywork, chassis alterations, and performance enhancements.
- Restoring Classic Cars: Revive and customize classic vehicles, often involving intricate metalwork and attention to historic details.
- Collaborating with Clients: Work closely with clients to understand their needs and provide expert advice on feasible customizations.
- Keeping Up with Trends: Stay informed about the latest trends in auto customization, materials, and techniques.
Requirements:
- Technical Skills: Proficient in welding, metal fabrication, and automotive repair. Formal training in automotive technology or a related field is highly beneficial.
- Creativity: Ability to conceptualize and design unique automotive features that align with clients’ requests and industry standards.
- Attention to Detail: Meticulous attention to detail to ensure the final product is of the highest quality and functionality.
- Problem-Solving: Strong problem-solving skills to address design and fabrication challenges that arise during customization projects.
- Customer Service: Good communication skills and customer service to understand client needs and ensure their satisfaction.
Career Path and Growth:
Custom Auto Fabricators have the opportunity to work on a variety of projects, from high-performance vehicles to personalized show cars.
With experience, they can become recognized experts in the field, start their own custom fabrication shops, or take on leadership roles within established automotive companies.
The satisfaction of creating one-of-a-kind vehicles provides a unique sense of accomplishment and recognition in the industry.
Structural Steel Fabricator
Average Salary: $40,000 – $60,000 per year
Structural Steel Fabricators are skilled professionals who work with steel to create components for buildings, bridges, and other infrastructures.
This role is ideal for Fabricator Welders who enjoy working with their hands and have a strong interest in the construction and manufacturing industries.
Job Duties:
- Interpreting Blueprints: Read and understand detailed construction drawings and specifications to determine the requirements for fabrication.
- Cutting and Shaping Steel: Use a variety of tools and machinery to cut, bend, and form steel into required shapes and sizes.
- Welding and Assembling Components: Utilize welding techniques to join steel parts together to form complete structures or components.
- Ensuring Quality and Precision: Check fabricated elements for quality and accuracy to ensure they meet design specifications and standards.
- Collaborating with Teams: Work closely with engineers, draftsmen, and construction teams to ensure that the fabricated steel fits the overall project needs.
- Maintenance of Equipment: Perform routine maintenance on fabrication machinery and tools to ensure operational efficiency and safety.
Requirements:
- Technical Skills: Proficiency in welding and fabrication techniques, as well as the ability to operate various machinery such as cutters, benders, and cranes.
- Attention to Detail: A keen eye for detail to ensure the accuracy of measurements and the quality of fabricated components.
- Physical Strength and Stamina: Ability to handle heavy materials and stand for extended periods.
- Problem-Solving: Aptitude for identifying issues during the fabrication process and developing practical solutions.
- Safety Consciousness: Knowledge of and adherence to all workplace safety guidelines and regulations.
Career Path and Growth:
As a Structural Steel Fabricator, there are numerous opportunities for career advancement.
With experience, one can become a lead fabricator, shop supervisor, or move into project management.
Professionals may also specialize in areas such as welding technology or quality control, or pursue further education to become structural engineers.
The demand for skilled fabricators is consistent as the need for infrastructure development and maintenance remains strong.
Manufacturing Welder
Average Salary: $40,000 – $60,000 per year
Manufacturing Welders play a critical role in the fabrication and construction of various metal products, from automotive parts to building structures.
This position is perfect for those who enjoy working with their hands and have a keen interest in manufacturing and production processes.
Job Duties:
- Reading Blueprints: Interpret technical drawings and specifications to determine the layout and dimensions of the welding project.
- Welding Components: Use various welding techniques to join metal parts together according to specifications.
- Inspecting Welds: Examine completed welds to ensure they meet quality standards and are free from defects.
- Maintaining Equipment: Perform regular maintenance on welding equipment and machinery to ensure operational efficiency.
- Adhering to Safety Protocols: Follow strict safety guidelines to prevent workplace accidents and injuries.
- Material Handling: Prepare and handle raw materials for the welding process, ensuring they are suitable for the task at hand.
Requirements:
- Technical Training: A high school diploma or equivalent, with further education or certification in welding from a technical school or apprenticeship program.
- Hands-on Experience: Proven experience with welding techniques such as MIG, TIG, stick welding, and others.
- Attention to Detail: Ability to produce precise and high-quality welds that meet design requirements and standards.
- Physical Stamina: Comfortable with standing for long periods, lifting heavy materials, and performing repetitive tasks.
- Safety Consciousness: Knowledge of and adherence to all occupational health and safety regulations.
Career Path and Growth:
Manufacturing Welders are essential in various industries, making this a stable career choice with numerous opportunities for advancement.
With experience, welders can become welding inspectors, shop foremen, or move into project management roles.
Continuous skill development can also lead to specialization in advanced welding techniques, which are highly sought after in the industry.
Pressure Vessel Welder
Average Salary: $40,000 – $70,000 per year
Pressure Vessel Welders specialize in the fabrication and welding of pressure vessels which are containers designed to hold gases or liquids at a pressure substantially different from the ambient pressure.
This role is ideal for fabricator welders who take pride in creating components that are critical for industries such as petrochemical, pharmaceutical, and energy sectors.
Job Duties:
- Fabricating Pressure Vessels: Use a variety of welding techniques to fabricate pressure vessels that meet industry standards and safety regulations.
- Interpreting Blueprints: Read and understand complex engineering blueprints and plans to accurately construct pressure vessels.
- Performing Quality Control: Conduct inspections and tests on welded surfaces, such as x-rays, ultrasonic testing, and hydrostatic testing, to ensure the integrity of the welds.
- Maintaining Equipment: Take care of welding machinery, ensuring that it is in good working order and calibrated correctly for precise work.
- Compliance with Safety Standards: Adhere to strict safety protocols to minimize risk when working with high-pressure systems.
- Continual Learning: Keep up-to-date with the latest welding techniques and safety standards in the pressure vessel industry.
Requirements:
- Technical Skills: Proficiency in welding techniques such as TIG, MIG, and stick welding, specifically for high-grade materials used in pressure vessels.
- Attention to Detail: Ability to produce precise and clean welds that are essential for the safety and functionality of pressure vessels.
- Physical Stamina: Must be capable of handling heavy materials and equipment and working in various positions for extended periods.
- Reading Blueprints: Skilled in interpreting technical drawings and specifications to ensure accurate construction.
- Safety Conscious: A strong understanding of and adherence to safety practices to prevent accidents and injuries.
Career Path and Growth:
Pressure Vessel Welders have the opportunity to work on a variety of projects and can specialize in different welding techniques and materials.
With experience, they can advance to supervisory roles, become welding inspectors, or move into more complex fabrication projects.
Continuous education and certification in advanced welding techniques can also open up opportunities for career advancement and specialization in high-demand industries.
Shipfitter
Average Salary: $40,000 – $60,000 per year
Shipfitters play a critical role in the shipbuilding industry, specializing in the layout, fabrication, assembly, and repair of metal structural parts in ships.
This role is ideal for Fabricator Welders who seek a challenging and rewarding career in marine construction and repair.
Job Duties:
- Interpreting Blueprints: Read and understand complex blueprints and technical drawings to determine the layout of ship sections and parts.
- Fabricating Metal Structures: Cut, shape, and assemble large metal components, ensuring they fit precisely according to specifications.
- Welding Components: Perform high-quality welding to join metal parts together, adhering to safety standards and project requirements.
- Inspecting Structures: Conduct regular inspections of metal structures for defects and ensure all parts meet quality control standards.
- Repairing Ships: Identify and repair damaged metal structures on ships, often working in challenging conditions.
- Working with a Team: Collaborate with other shipyard professionals, such as welders, pipefitters, and engineers, to complete projects efficiently.
Requirements:
- Educational Background: A high school diploma or equivalent, with technical training or apprenticeship in welding, metal fabrication, or a related field.
- Welding Certification: Possession of a welding certification, demonstrating proficiency in various welding techniques used in ship construction.
- Physical Stamina: Ability to perform physically demanding tasks, including lifting heavy materials and working in confined spaces.
- Precision and Attention to Detail: High level of accuracy in cutting, fitting, and welding metal parts to ensure the structural integrity of the ship.
- Problem-Solving Skills: Aptitude for identifying issues and coming up with practical solutions during the fabrication and assembly processes.
Career Path and Growth:
As a Shipfitter, you have the opportunity to advance your career within the shipbuilding industry.
With experience, you can become a lead fitter, supervisor, or project manager overseeing larger sections of ship construction.
There’s also potential for specialization in areas like naval architecture or marine engineering for those interested in further education and training.
Fabrication Shop Foreman
Average Salary: $50,000 – $75,000 per year
Fabrication Shop Foremen oversee operations and manage teams in metal fabrication shops, ensuring that projects are completed efficiently and to high-quality standards.
This role is ideal for experienced fabricator welders who have strong leadership skills and a desire to drive productivity in a hands-on industrial environment.
Job Duties:
- Supervising Fabrication Projects: Manage the workflow and ensure projects are completed on time, within budget, and to the required quality standards.
- Leading Teams: Direct and motivate a team of welders and fabricators, allocating tasks based on individual strengths and project requirements.
- Quality Control: Oversee the quality of workmanship in the shop, implementing standards and conducting inspections to maintain high-quality output.
- Training and Development: Identify skill gaps and arrange for appropriate training to enhance the capabilities of the fabrication team.
- Safety Management: Enforce strict safety protocols, conduct safety briefings, and ensure compliance with OSHA regulations and other safety standards.
- Resource Management: Manage the inventory of materials and tools, ensuring that resources are available and maintained for production needs.
Requirements:
- Technical Expertise: Proven experience in metal fabrication and welding, with a thorough understanding of industry practices and standards.
- Leadership Skills: Strong leadership and management abilities, with experience directing a team in a manufacturing or industrial setting.
- Problem-solving: Ability to troubleshoot issues that arise during the fabrication process and implement effective solutions.
- Communication Skills: Excellent verbal and written communication skills for coordinating with team members, management, and clients.
- Attention to Detail: A keen eye for detail to ensure high quality and precision in fabricated products.
- Time Management: Capability to manage multiple projects simultaneously and prioritize tasks to meet deadlines.
Career Path and Growth:
As a Fabrication Shop Foreman, there is potential for career growth within the manufacturing sector.
With experience, one may advance to positions such as Plant Manager, Operations Manager, or even open their own fabrication business.
Continuous improvement, adoption of new technologies, and leadership development can further enhance career prospects in this field.
Ornamental Metal Worker
Average Salary: $35,000 – $60,000 per year
Ornamental Metal Workers specialize in creating and installing decorative metalwork, such as gates, railings, and architectural details for buildings.
This role is ideal for Fabricator Welders with an eye for aesthetics and a passion for creating beautiful and enduring metalwork.
Job Duties:
- Fabricating Decorative Metalwork: Craft intricate designs and patterns for ornamental purposes in various settings, from residential to commercial.
- Installing Metal Structures: Securely install decorative metal features while ensuring they meet safety and quality standards.
- Interpreting Blueprints: Read and understand complex architectural drawings to create accurate and detailed works of art.
- Custom Designing: Work with clients to develop custom designs that align with their vision and the overall aesthetic of the project.
- Restoration: Repair and restore antique or damaged metalwork, preserving historical integrity while maintaining modern safety standards.
- Material Knowledge: Stay informed on various metals and finishing techniques to ensure the longevity and appeal of the ornamental pieces.
Requirements:
- Technical Skills: Proficiency in welding, forging, and metal fabrication techniques, with an emphasis on decorative work.
- Attention to Detail: A keen eye for detail to create intricate designs and ensure a high-quality finish on all projects.
- Artistic Ability: An inherent sense of design and artistry to craft visually appealing metal structures.
- Physical Stamina: Capable of handling heavy materials and standing for extended periods during the fabrication process.
- Problem-Solving: Aptitude for troubleshooting and resolving issues that may arise during the design or installation phases.
Career Path and Growth:
As an Ornamental Metal Worker, there are opportunities to work on high-profile projects, collaborate with designers and architects, and leave a lasting impact on the visual landscape.
With experience, workers can advance to lead roles, start their own ornamental metalwork business, or become recognized artists within the field.
Welding Educator or Instructor
Average Salary: $45,000 – $75,000 per year
Welding Educators or Instructors specialize in teaching and training the next generation of fabricator welders in various educational settings, from trade schools to community colleges.
This role is ideal for experienced welders who are passionate about their craft and eager to pass on their knowledge and skills to others.
Job Duties:
- Developing Curriculum: Create comprehensive welding programs that cover essential welding techniques, safety protocols, and blueprint reading.
- Teaching Practical Skills: Conduct hands-on welding classes where students learn and practice different welding processes such as MIG, TIG, and Stick welding.
- Evaluating Student Performance: Assess students’ proficiency in welding techniques and understanding of materials and equipment.
- Maintaining Safety Standards: Ensure all safety guidelines are followed within the workshop and educate students on proper safety practices.
- Staying Current: Keep up-to-date with the latest welding technologies, methods, and industry standards to provide relevant instruction.
- Professional Development: Participate in continuing education opportunities to enhance teaching methods and technical expertise.
Requirements:
- Educational Background: A combination of a high school diploma and extensive welding experience, or an Associate’s degree in Welding Technology or a similar field.
- Certifications: Professional certifications from recognized welding institutions such as the American Welding Society (AWS) are highly beneficial.
- Communication Skills: Strong verbal and written communication skills, with the ability to explain complex welding concepts clearly.
- Teaching Ability: A knack for teaching and the patience to instruct students of varying skill levels.
- Leadership: Confidence in leading a classroom and managing a workshop environment.
Career Path and Growth:
As a Welding Educator or Instructor, you have the opportunity to shape the future of the welding industry by training skilled professionals.
With experience, you may advance to senior educational roles such as a Program Director, develop specialized welding courses, or contribute to the advancement of welding technology through research and collaboration with the industry.
Artisan Metalworks Craftsperson
Average Salary: $32,000 – $48,000 per year
Artisan Metalworks Craftspeople create and restore intricate metal pieces, ranging from decorative art to functional items, using traditional and modern metalworking techniques.
This role is ideal for Fabricator Welders who appreciate the artistry in metalwork and enjoy crafting unique, high-quality items.
Job Duties:
- Forging and Shaping Metal: Use tools and techniques such as hammering, bending, and welding to create detailed metal pieces.
- Restoration Projects: Repair and restore antique metalworks, maintaining the integrity and style of the original pieces.
- Custom Design and Fabrication: Collaborate with clients to design and produce bespoke metal items tailored to their specifications.
- Quality Control: Inspect finished pieces for quality and durability, ensuring they meet both aesthetic and functional standards.
- Tool and Equipment Maintenance: Maintain and calibrate metalworking tools and equipment to ensure precision and safety in the workshop.
- Staying Current: Keep up with trends in metal artistry and advancements in metalworking techniques and materials.
Requirements:
- Technical Skillset: Proficiency in metalworking techniques such as welding, soldering, forging, and finishing.
- Creativity: A strong sense of design and creativity to envision and craft unique metalworks.
- Attention to Detail: Keen eye for detail to produce intricate and fine quality work.
- Physical Stamina: Ability to work for extended periods, often in a standing position and handling heavy materials.
- Problem-Solving: Aptitude for troubleshooting and solving design or fabrication challenges creatively.
Career Path and Growth:
Artisan Metalworks Craftspeople have the opportunity to establish a reputation for quality and creativity in their field.
With experience, they may open their own studios, become recognized artists, lead workshops, or contribute to high-profile restoration projects.
There is also potential for collaboration with designers and architects, expanding into larger-scale installations or innovative architectural metalwork.
Conclusion
In conclusion, those are some of the most remarkable jobs for a Fabricator Welder.
The range of opportunities is boundless, offering something for every Welder who has a passion for fabrication.
So go ahead, seize the day, and start your journey towards working with metal, in the way that’s best for you.
Just remember: it’s NEVER too late to mold your passion into a profession.
The Prosperity Parade: High-Paying Jobs That Are Taking the Lead!
Job Market Reality: The Careers With the Smallest Paychecks in 2025
Living Dangerously: The Magnetic Pull of Perilous Professions
The Automated Age: Professions Where AI is Taking Charge
From High-Stakes to High Stress: Careers That Constantly Test You!