30 Jobs For Model Makers (Precision Pioneers)
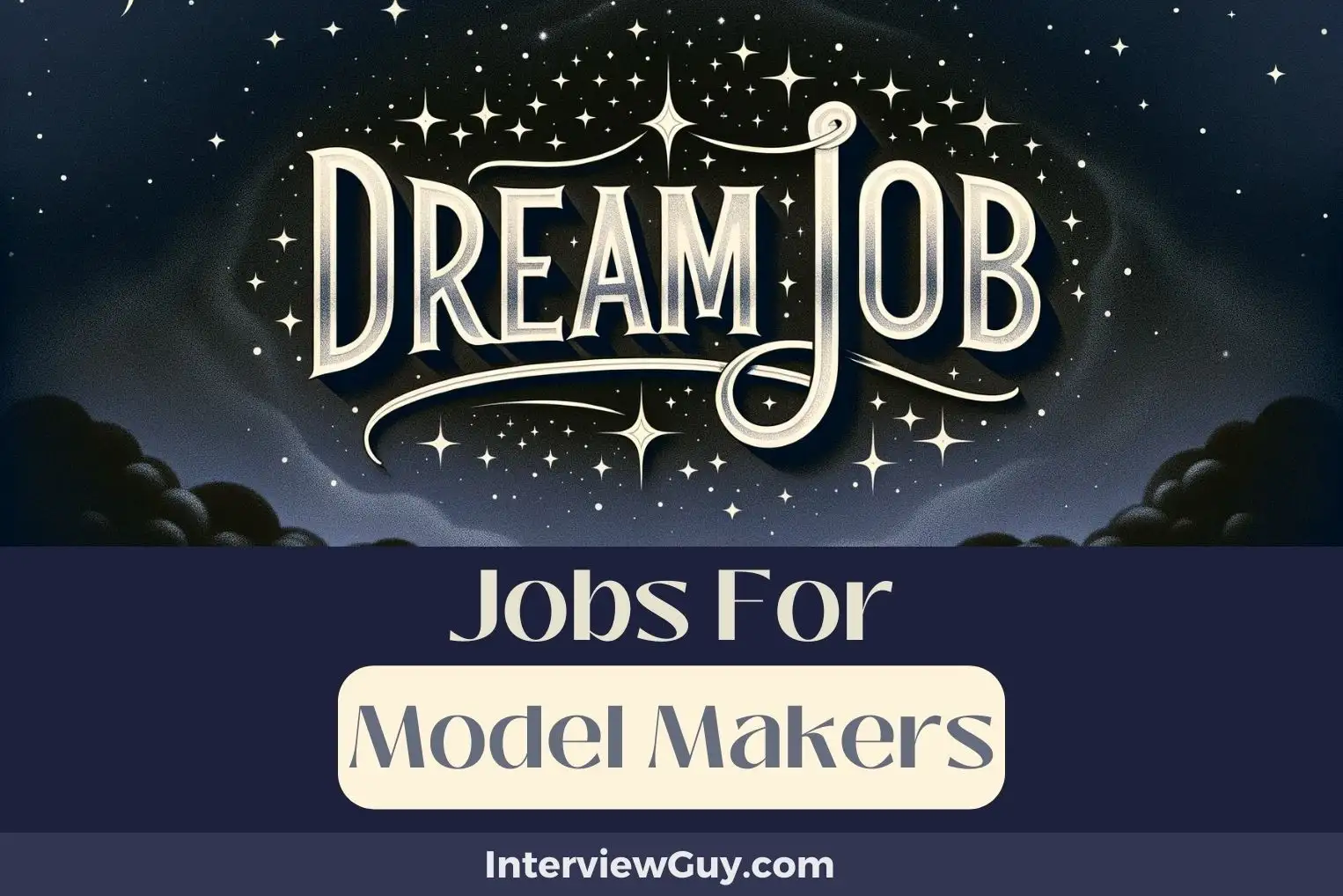
Are you a devoted model maker? Love immersing yourself in a world of miniature creations?
Then, you’re in for a treat!
Today, we’re pulling back the curtain on a list of dream jobs for model making enthusiasts.
From architectural model makers to movie prop designers. Each one is a perfect fit for those who cannot resist the allure of model making.
Imagine being surrounded by models. Day in, day out.
Sounds like paradise, right?
So, clear your workbench.
And prepare yourself to discover your dream profession in model making!
Industrial Model Maker
Average Salary: $45,000 – $65,000 per year
Industrial Model Makers create detailed scale models of products or parts, which are used for engineering, prototyping, or marketing purposes.
This role is ideal for individuals who have a knack for precision, craftsmanship, and enjoy bringing technical designs to life in a tangible form.
Job Duties:
- Crafting Detailed Models: Construct accurate scale models of products or components for visual and functional testing.
- Interpreting Blueprints: Translate technical drawings and specifications into physical models using a variety of materials and tools.
- Prototyping: Collaborate with engineers and designers in the prototyping process, providing feedback and modifications to improve the final product.
- Utilizing Technology: Employ advanced technologies such as 3D printing and CNC machining to create models and prototypes.
- Material Knowledge: Select appropriate materials based on model requirements for aesthetics, durability, and functionality.
- Quality Assurance: Ensure all models meet the necessary standards and specifications before they are used for testing or presentations.
Requirements:
- Educational Background: An Associate’s degree or certification in Model Making, Industrial Design, or a related field is often required.
- Technical Skills: Proficiency in using hand tools, machinery, and technology such as CAD software and 3D printers.
- Attention to Detail: Exceptional attention to detail to create accurate and functional models.
- Problem-Solving: Strong problem-solving skills to overcome design and fabrication challenges.
- Collaboration: Ability to work closely with engineers, designers, and other stakeholders to achieve desired outcomes.
Career Path and Growth:
Industrial Model Makers play a critical role in product development and can work in various industries, including automotive, aerospace, consumer electronics, and more.
With experience, Industrial Model Makers can advance to lead model maker positions, supervisory roles, or specialize in high-demand areas such as additive manufacturing or digital fabrication.
There is also potential to move into design or engineering positions with additional education and experience.
Architectural Model Maker
Average Salary: $40,000 – $60,000 per year
Architectural Model Makers create detailed scale models of buildings and structures, providing a tangible representation of architectural designs.
This role is ideal for model makers who have an interest in architecture and enjoy crafting physical representations of envisioned structures.
Job Duties:
- Constructing Scale Models: Build accurate and detailed physical models of architectural projects, using materials such as wood, plastic, metal, and cardboard.
- Interpreting Architectural Drawings: Read and comprehend detailed architectural plans to create precise models.
- Utilizing Tools and Technology: Employ a variety of hand tools, machinery, and technology such as laser cutters and 3D printers to construct models.
- Detailing and Finishing: Apply finishing touches to models, including painting, texturing, and landscaping to enhance realism.
- Collaborating with Architects: Work closely with architects and designers to understand their vision and ensure accuracy in the models.
- Time Management: Manage multiple projects and deadlines, often working on several models simultaneously.
Requirements:
- Educational Background: A degree or certification in model making, architecture, or a related field is highly beneficial.
- Attention to Detail: Exceptional precision and an eye for detail to create accurate and high-quality models.
- Technical Skills: Proficiency in reading architectural plans and using model-making tools and equipment.
- Creativity: An artistic sense and creativity to replicate architectural designs in miniature form.
- Problem-Solving: Ability to troubleshoot and solve issues that arise during the model-making process.
Career Path and Growth:
As an Architectural Model Maker, there is the potential to work on a variety of projects, from residential homes to landmark buildings, each offering unique challenges and learning opportunities.
With experience, model makers can become lead model makers, supervising teams, or specialize in certain types of models or materials.
Some may choose to start their own model-making studios or become consultants for architectural firms.
Prototype Developer
Average Salary: $50,000 – $80,000 per year
Prototype Developers are responsible for creating physical models and prototypes that help in the visualization and testing of products before they go into mass production.
This role is ideal for model makers who have a knack for transforming concepts into tangible models, ensuring that ideas can be effectively evaluated and improved upon.
Job Duties:
- Designing and Building Prototypes: Utilize a variety of materials and techniques to construct accurate and functional prototypes based on design specifications.
- Collaborating with Design Teams: Work closely with engineers and designers to understand the requirements and to provide feedback on the prototype’s feasibility and functionality.
- Testing Prototypes: Carry out tests on prototypes to assess design, durability, and functionality, and to identify potential improvements or issues.
- Utilizing Technology: Employ cutting-edge technology such as 3D printing, CNC machining, and CAD software to create high-fidelity prototypes.
- Refining Prototypes: Modify and refine prototypes based on test results and feedback from the design team to achieve the desired outcome.
- Documenting the Development Process: Keep detailed records of the prototyping process, including design changes and test results, for future reference.
Requirements:
- Educational Background: A degree or certificate in industrial design, mechanical engineering, or a related field is often required.
- Technical Skills: Proficiency with tools and techniques used in prototype development, including 3D printers, CNC machines, and relevant software.
- Attention to Detail: Strong attention to detail to ensure prototypes accurately reflect the intended design and functionality.
- Problem-Solving: Ability to troubleshoot issues and come up with creative solutions during the prototype development process.
- Collaboration: Excellent teamwork skills to work effectively with cross-functional teams and incorporate feedback into prototype iterations.
Career Path and Growth:
As a Prototype Developer, you have the opportunity to be at the forefront of product development, turning innovative ideas into realities.
With experience, Prototype Developers can progress to lead roles within the prototyping department, specialize in advanced prototyping technologies, or become consultants for firms looking to improve their product development processes.
Toy Model Designer
Average Salary: $40,000 – $70,000 per year
Toy Model Designers create and develop models for toys and collectibles, often focusing on characters, vehicles, and other elements from popular culture and films.
This role is perfect for model makers who have a flair for creativity and a passion for bringing joy to children and collectors.
Job Duties:
- Conceptualizing Designs: Develop original concepts or adapt existing characters and vehicles into toy models, ensuring playability and appeal.
- Sketching and Prototyping: Create detailed sketches and prototypes using a variety of materials and techniques, including 3D modeling software.
- Collaborating with Teams: Work with production, marketing, and design teams to ensure the successful creation and launch of toy models.
- Material Selection: Choose appropriate materials for toy production that are safe, durable, and cost-effective.
- Quality Control: Ensure the final product meets safety standards and company quality benchmarks.
- Keeping Current with Trends: Stay informed about popular culture, including movies, comics, and games, to inspire new toy designs.
Requirements:
- Educational Background: A Bachelor’s degree in Industrial Design, Toy Design, or a related field is often required.
- Creative Skills: Strong artistic abilities, with expertise in drawing, sculpting, and using design software.
- Understanding of Manufacturing: Knowledge of production processes, materials, and technology used in toy manufacturing.
- Attention to Detail: Ability to focus on intricate details to create accurate and engaging models.
- Problem-Solving: Skills in overcoming design challenges to create toys that are both fun and functional.
Career Path and Growth:
As a Toy Model Designer, you have the opportunity to influence and shape the play experiences of future generations.
With experience, you can take on lead design roles, specialize in a particular type of toy or model, or move into project management positions within the toy industry.
The role also allows for creative freedom and the chance to see your concepts come to life in the hands of children and collectors around the world.
Special Effects Model Maker
Average Salary: $45,000 – $75,000 per year
Special Effects Model Makers create physical models and miniature effects for use in film, television, and the entertainment industry, often simulating environments, vehicles, and characters.
This role is perfect for model makers who have a keen interest in bringing fantasy and science fiction to life, much like the captivating worlds seen in Star Wars.
Job Duties:
- Building Detailed Models: Craft accurate and detailed models and miniatures based on concept art and design specifications.
- Applying Special Effects: Implement various techniques to simulate weathering, battle damage, and other effects to create realism in models.
- Collaborating with Designers: Work closely with concept artists, designers, and directors to ensure models meet the creative vision of the project.
- Problem-Solving: Innovate to overcome design challenges and achieve the desired visual effects within practical and budgetary constraints.
- Using Technology: Utilize a range of tools and technologies, including traditional sculpting, 3D printing, and laser cutting, to create components.
- Maintaining Workshop Equipment: Oversee the care and maintenance of model-making tools and equipment.
Requirements:
- Educational Background: A degree or diploma in Model Making, Special Effects, or a related field is highly beneficial.
- Technical Skills: Proficiency in a variety of model-making techniques, including sculpting, casting, painting, and assembling complex miniatures.
- Creativity: An eye for detail and a creative mind to build intricate models that convincingly mimic real-life objects or fantasy elements.
- Collaborative Spirit: Ability to work effectively as part of a team to bring complex visual effects to life.
- Time Management: Strong organizational skills to manage multiple projects and meet tight production deadlines.
Career Path and Growth:
Special Effects Model Makers have the opportunity to work on a variety of projects, from small-scale independent films to major Hollywood blockbusters.
With experience, they can advance to lead model maker positions, special effects supervisors, or even transition into roles such as production design.
The skills developed in this field also open doors to opportunities in other areas of the entertainment industry, including theme park design and video game development.
Film and TV Prop Maker
Average Salary: $40,000 – $60,000 per year
Film and TV Prop Makers craft the items that actors handle directly on screen, which can range from everyday objects to fantastical creations that exist only in the scriptwriter’s imagination.
This role is perfect for Model Makers who enjoy bringing the tangible elements of a film or television show to life, often requiring a blend of artistic skills and practical engineering.
Job Duties:
- Creating Props: Design and construct a variety of props based on the needs of the production, ensuring they are believable and functional for on-screen use.
- Collaborating with Art Departments: Work closely with production designers and art directors to maintain the visual style and historical accuracy of the props.
- Material Selection: Choose appropriate materials and techniques to create durable and aesthetically appropriate props.
- Special Effects Integration: Occasionally work with the special effects team to incorporate mechanical or electronic elements into props.
- Repairs and Alterations: Perform on-set or on-location maintenance and modifications to props as needed during filming.
- Research and Development: Conduct research to ensure props are period-appropriate and meet the creative vision of the production.
Requirements:
- Technical Skills: Proficiency in a variety of construction and fabrication techniques, including woodworking, metalworking, sewing, painting, and sculpting.
- Creativity and Imagination: Ability to conceptualize and create props that fulfill the script’s requirements and add depth to the visual storytelling.
- Attention to Detail: Keen eye for detail to ensure props are consistent and realistic within the film’s universe.
- Time Management: Capacity to work within tight deadlines and adapt to last-minute changes in production schedules.
- Collaborative Nature: Strong teamwork skills to work effectively with different departments and contribute to the creative process.
Career Path and Growth:
As a Film and TV Prop Maker, you have the opportunity to work on a variety of productions, from small indie films to large blockbuster movies and popular TV series.
With experience, Prop Makers can become Head Prop Makers or Prop Masters, overseeing entire departments.
Some may specialize in particular types of props, such as weapons, vehicles, or historical items, or move into production design or art direction roles.
Exhibit Designer
Average Salary: $40,000 – $60,000 per year
Exhibit Designers create immersive and educational displays for museums, trade shows, and various events, often incorporating models and replicas to enhance the visitor experience.
This role is perfect for model makers who excel in creating detailed and accurate representations and wish to showcase their work in engaging environments.
Job Duties:
- Designing Exhibits: Develop concepts and designs for exhibits that effectively communicate themes and information to the public.
- Building Models: Craft detailed models and replicas that are integral to the storytelling and educational aspects of the exhibit.
- Collaborating with Teams: Work with curators, educators, and other professionals to ensure the exhibit’s content is accurate and engaging.
- Project Management: Oversee the production of exhibits from initial design to final installation, ensuring projects stay within budget and on schedule.
- Utilizing Technology: Incorporate interactive elements and multimedia into exhibits to create dynamic and modern visitor experiences.
- Research and Development: Stay updated on the latest techniques in model making, materials, and exhibit design trends to continually improve the quality of displays.
Requirements:
- Educational Background: A Bachelor’s degree in Industrial Design, Exhibit Design, or a related field is often required.
- Technical Skills: Proficiency in design software (such as CAD) and model-making skills, including the ability to work with a variety of materials.
- Creativity: A strong creative vision and the ability to conceptualize and bring to life engaging exhibits.
- Detail-Oriented: Attention to detail in the creation of models and design elements to ensure accuracy and impact.
- Collaboration: Ability to work effectively with multidisciplinary teams and communicate design concepts clearly.
Career Path and Growth:
Exhibit Designers have the opportunity to influence and educate the public by creating tangible and memorable experiences.
With experience, they can advance to lead designer roles, manage larger projects, or specialize in specific types of exhibits such as historical, scientific, or art installations.
Some may also choose to work as freelancers or start their own exhibit design firms to further expand their creative horizons.
Automotive Model Builder
Average Salary: $45,000 – $70,000 per year
Automotive Model Builders are skilled artisans who create full-scale models and prototypes of vehicles for the automotive industry.
This role is perfect for model makers who have a passion for cars, design, and precision craftsmanship.
Job Duties:
- Building Scale Models: Construct detailed scale models of vehicles, often using clay or other materials, to bring automotive designs to life.
- Collaborating with Designers: Work closely with automotive designers to understand and interpret design concepts into physical models.
- Prototyping: Fabricate prototypes for both exterior and interior vehicle components, which are used for aerodynamic testing and design evaluation.
- Utilizing Technology: Employ advanced technologies such as CAD software and 3D printing to create accurate models and parts.
- Detail-Oriented Finishing: Apply finishing touches to models, ensuring they meet the high-quality standards of the automotive industry.
- Staying Current: Keep abreast of the latest trends in automotive design, materials, and model-making techniques.
Requirements:
- Educational Background: A degree or certificate in Model Making, Industrial Design, or a related field is preferred.
- Technical Skills: Proficiency in model-making tools and techniques, including CAD software and traditional handcrafting methods.
- Attention to Detail: An acute eye for detail and precision is crucial for creating accurate and realistic automotive models.
- Collaboration: Ability to work effectively with design teams and take direction to achieve the desired outcome.
- Problem-Solving: Aptitude for troubleshooting and solving complex design and construction challenges.
Career Path and Growth:
As an Automotive Model Builder, you play a key role in the development and refinement of vehicle designs.
With experience, you can advance to lead model-making positions, specialize in high-demand niches such as luxury or concept vehicles, or progress into design roles within the automotive industry.
The skills and expertise developed in this field can also open opportunities for consultancy work or teaching positions in educational institutions that offer design and model-making courses.
Aerospace Model Maker
Average Salary: $45,000 – $70,000 per year
Aerospace Model Makers are skilled artisans who create detailed scale models of aircraft, spacecraft, and other aerospace-related vehicles and components.
These models are used for engineering studies, wind-tunnel testing, design evaluation, and as display pieces to showcase advancements in aerospace technology.
This role is ideal for model makers with a passion for aviation and space exploration, providing an opportunity to contribute to the development of cutting-edge aerospace products.
Job Duties:
- Creating Detailed Models: Construct precise and detailed scale models of aerospace vehicles and components using various materials and techniques.
- Collaborating with Engineers: Work closely with aerospace engineers to ensure models meet specific requirements for testing or presentation purposes.
- Applying Technical Specifications: Interpret blueprints, technical drawings, and CAD designs to accurately replicate the vehicles and parts in miniature form.
- Utilizing Specialized Equipment: Operate machinery and tools such as CNC machines, lathes, and 3D printers to fabricate model components.
- Finishing and Painting: Apply finishing touches, including painting and decaling, to create realistic and visually appealing models.
- Keeping Abreast of Industry Developments: Stay informed about the latest aerospace technologies, materials, and construction techniques to produce high-quality models.
Requirements:
- Educational Background: A degree or certificate in model making, industrial design, or a related field is beneficial.
- Technical Skills: Proficient in reading and interpreting technical drawings and proficient with various model-making tools and equipment.
- Attention to Detail: A keen eye for detail to create accurate and intricate models that reflect the true design of the aerospace products.
- Manual Dexterity: Excellent hand-eye coordination and the ability to perform precise and controlled movements.
- Problem-Solving: Ability to troubleshoot and solve issues that arise during the model-making process.
Career Path and Growth:
Aerospace Model Makers can advance their careers by taking on more complex projects, leading teams of model makers, or specializing in particular types of models, such as historical aircraft or futuristic spacecraft.
With experience, they may also move into design or engineering roles, or become consultants for aerospace companies, leveraging their deep understanding of scale and design.
3D Printing Technician
Average Salary: $40,000 – $60,000 per year
3D Printing Technicians operate and maintain 3D printing equipment, creating physical models from digital designs.
This role is perfect for model makers who enjoy bringing concepts to life through cutting-edge technology.
Job Duties:
- Operating 3D Printers: Set up and manage 3D printers to produce accurate and high-quality models based on digital designs.
- Maintaining Equipment: Perform regular maintenance and troubleshooting on 3D printers to ensure optimal performance.
- Preparing Digital Files: Convert or adjust digital models to be compatible with 3D printing processes, ensuring precision in the final product.
- Post-Processing: Clean, cure, and finish printed objects to meet quality standards and client specifications.
- Material Management: Select and manage appropriate printing materials, such as resins, plastics, or metals, depending on project needs.
- Staying Current: Keep up-to-date with the latest trends, materials, and advancements in 3D printing technology.
Requirements:
- Technical Knowledge: Proficiency in operating 3D printers and understanding of the principles of additive manufacturing.
- Attention to Detail: Ability to focus on fine details to ensure the accuracy and quality of 3D printed models.
- Problem-Solving Skills: Aptitude for identifying and resolving technical issues with 3D printers and print jobs.
- Software Skills: Familiarity with 3D modeling software and file preparation for 3D printing.
- Adaptability: Versatility in working with different 3D printing technologies and materials.
Career Path and Growth:
The role of a 3D Printing Technician offers a unique blend of creativity and technical skill.
With the rapid expansion of 3D printing applications across industries, technicians can look forward to diverse career opportunities.
Advancements may include specialized roles in engineering, product development, or even managing a 3D printing facility.
As expertise grows, there may also be opportunities to innovate within the field, contributing to the development of new printing materials and techniques.
Scale Model Builder for Museums
Average Salary: $40,000 – $60,000 per year
Scale Model Builders for Museums create detailed and accurate representations of historical, scientific, and cultural artifacts for educational and display purposes.
This role is perfect for model makers who have a keen interest in history, science, or art, and enjoy crafting intricate replicas for public education and appreciation.
Job Duties:
- Building Accurate Models: Construct detailed scale models of artifacts, buildings, historical scenes, or scientific concepts for museum exhibits.
- Research and Development: Conduct thorough research to ensure models are historically accurate and meet educational goals.
- Collaborating with Curators: Work closely with museum staff to design models that complement and enhance exhibits.
- Restoring Models: Maintain and repair existing models to preserve their appearance and educational value.
- Utilizing Technology: Employ various techniques and tools, including 3D printing and digital modeling software, to create precise and realistic models.
- Education and Demonstration: Occasionally provide demonstrations or workshops to museum visitors about the art and science of model making.
Requirements:
- Educational Background: A degree or certification in fine arts, design, engineering, or a related field is often beneficial.
- Attention to Detail: Exceptional skill in crafting detailed and accurate representations.
- Artistic Talent: Strong artistic abilities, including a good sense of scale, proportion, and color.
- Technical Proficiency: Experience with model-making tools, materials, and technology.
- Collaboration: Ability to work effectively with museum staff and other stakeholders to fulfill the vision for exhibits.
- Problem-Solving: Aptitude for overcoming challenges in design and construction to ensure models meet exhibit requirements.
Career Path and Growth:
This role offers the opportunity to contribute to the educational and cultural enrichment of the public through the creation of tangible, engaging exhibits.
With experience, Scale Model Builders for Museums can advance to lead designer positions, manage larger projects, or specialize in particular types of models or techniques.
There are also opportunities to freelance or start a business providing models for various clients in the museum and exhibition sectors.
Medical Model Maker
Average Salary: $45,000 – $70,000 per year
Medical Model Makers create detailed anatomical models, surgical simulation models, and custom prosthetics, often used for educational and surgical planning purposes.
This role is ideal for individuals who have a strong interest in the medical field and human anatomy, combined with a passion for precision model making.
Job Duties:
- Designing Anatomical Models: Craft accurate and detailed models of human organs and body parts for medical training and educational purposes.
- Creating Surgical Simulation Models: Produce models that simulate various medical conditions for pre-surgical planning and medical student training.
- Customizing Prosthetics: Work closely with patients and medical professionals to design and fabricate customized prosthetics and implants.
- Collaborating with Healthcare Professionals: Communicate with doctors, surgeons, and educators to ensure models meet specific requirements.
- Using Advanced Technology: Utilize 3D printing, CNC machining, and other technologies to create precise and functional medical models.
- Quality Control: Ensure that all models are anatomically accurate, durable, and meet the highest standards of medical education.
Requirements:
- Educational Background: A degree or certification in biomedical engineering, medical illustration, or a related field is highly beneficial.
- Technical Skills: Proficiency in CAD software, 3D printing, and traditional model-making techniques.
- Attention to Detail: Exceptional attention to detail for creating anatomically correct and functional models.
- Collaboration: Ability to work closely with medical professionals to understand their needs and specifications.
- Problem-Solving: Aptitude for troubleshooting and refining models to ensure they serve their intended educational or clinical purpose.
Career Path and Growth:
Medical Model Makers play a critical role in advancing medical education and improving patient outcomes.
With experience, Medical Model Makers can advance to lead designer positions, manage teams of model makers, or specialize in cutting-edge medical modeling technologies, contributing to innovation in medical practices and procedures.
Miniature Set Designer
Average Salary: $40,000 – $75,000 per year
Miniature Set Designers craft intricate and realistic models for use in film, television, and theater productions.
Their work is crucial for creating the immersive worlds and detailed environments that bring stories to life on screen and stage.
This role is perfect for model makers who delight in constructing detailed miniatures and have an interest in storytelling through visual design.
Job Duties:
- Creating Detailed Models: Design and build detailed miniature sets and props that accurately represent larger scenes or objects for visual effects or background shots.
- Collaborating with Directors and Cinematographers: Work closely with the creative team to ensure that the miniatures meet the visual requirements of the project.
- Scaling Down Realism: Apply techniques to scale down structures, landscapes, and objects while maintaining a high level of detail and realism.
- Special Effects Integration: Incorporate features that allow for the integration of special effects, such as lighting or mechanized components.
- Material Selection: Choose appropriate materials that will achieve the desired aesthetic and functional properties for each miniature set piece.
- Staying Current with Technology: Keep up-to-date with advancements in miniaturization techniques and materials, as well as digital effects that complement physical models.
Requirements:
- Educational Background: A degree in Fine Arts, Design, Film Production, or a related field, with a focus on model-making or scenic design.
- Attention to Detail: Exceptional skills in crafting minute details that make miniature sets come to life.
- Artistic Talent: Strong artistic ability, including an understanding of scale, proportion, texture, and color.
- Technical Skills: Familiarity with a variety of tools and materials used in model-making and an ability to use them with precision.
- Problem-Solving: Creative problem-solving skills to overcome the challenges of miniaturization and the illusion of scale.
- Collaboration: Ability to work effectively with a team, often under tight deadlines and with complex requirements.
Career Path and Growth:
Miniature Set Designers have the opportunity to work on a wide range of exciting projects, from blockbuster movies to intricate theater productions.
With experience, designers can advance to lead design roles, specialize in particular types of miniature work (such as historical or fantasy sets), or transition into supervisory positions within the art department.
There is also the potential to cross over into digital effects, combining traditional model-making skills with the latest in visual effects technology.
Jewelry Model Maker
Average Salary: $40,000 – $60,000 per year
Jewelry Model Makers craft detailed models of jewelry pieces, which are used to create molds for production or for showcasing new designs to clients.
This role is ideal for individuals who have an appreciation for fine detail, artistry, and the beauty of jewelry design.
Job Duties:
- Creating Detailed Models: Use various materials such as wax, metal, or resin to create precise and intricate models of jewelry based on design specifications.
- Collaborating with Designers: Work closely with jewelry designers to understand and interpret design concepts, ensuring the final model reflects the intended design.
- Engraving and Detailing: Employ engraving tools and techniques to add fine details and textures to the models, achieving a high level of craftsmanship.
- Prototype Development: Produce prototypes that can be used to assess the design’s functionality and aesthetic before mass production.
- Quality Control: Inspect models for accuracy, symmetry, and adherence to design, making adjustments as necessary.
- Staying Current: Keep up-to-date with the latest trends in jewelry design and model-making technology to enhance skills and efficiency.
Requirements:
- Educational Background: A degree or certificate in Jewelry Design, Fine Arts, or a related field is beneficial, though not always required.
- Artistic Skills: A strong artistic ability with an eye for design and a steady hand to create detailed models.
- Technical Proficiency: Familiarity with model-making tools and materials, as well as emerging technologies such as 3D printing.
- Attention to Detail: Exceptional attention to detail to accurately bring intricate jewelry designs to life.
- Patience and Precision: The patience to work meticulously on detailed models and the precision to ensure high-quality outcomes.
Career Path and Growth:
A career as a Jewelry Model Maker provides the opportunity to work with a variety of jewelry styles and to be part of creating beautiful, tangible pieces that can be cherished for generations.
With experience, Jewelry Model Makers can advance to supervisory positions, specialize in high-end custom jewelry, or establish their own model-making studios.
As the reputation for quality and craftsmanship grows, there may also be opportunities to collaborate with renowned jewelry designers and luxury brands.
Model Shop Manager
Average Salary: $55,000 – $75,000 per year
Model Shop Managers oversee the operations of a model-making workshop or facility, ensuring that the production of scale models meets quality and precision standards.
This role is ideal for model makers who enjoy leading a team and have a passion for creating detailed, accurate representations of objects.
Job Duties:
- Managing Team and Projects: Lead a team of model makers, assigning projects, and ensuring deadlines are met with the highest standard of craftsmanship.
- Quality Control: Oversee the production process to ensure that all models are constructed accurately and to scale, aligning with client specifications.
- Supply and Inventory Management: Maintain an organized inventory of materials and tools necessary for model making and procure supplies as needed.
- Client Interaction: Work directly with clients to understand their needs, provide project updates, and deliver finished models.
- Technical Expertise: Utilize advanced model-making techniques and machinery, such as 3D printing, laser cutting, and CNC machining.
- Training and Development: Train new hires in model-making techniques and safety protocols, and encourage the professional growth of team members.
Requirements:
- Educational Background: A degree in Industrial Design, Model Making, Fine Arts, or a related field is preferred.
- Leadership Skills: Proven ability to manage a team, delegate tasks effectively, and maintain a positive and productive work environment.
- Attention to Detail: Exceptional attention to detail is critical for creating accurate and high-quality models.
- Technical Proficiency: Familiarity with model-making tools, machinery, and software is essential.
- Problem-Solving: Ability to troubleshoot and solve issues that arise during the model-making process.
Career Path and Growth:
As a Model Shop Manager, there is potential for career advancement within the field of model making.
Managers can progress to higher leadership positions, oversee larger and more complex projects, or even start their own model-making businesses.
Additionally, there’s an opportunity to innovate within the field by incorporating new technologies and materials into model production.
Animation Modeler
Average Salary: $50,000 – $75,000 per year
Animation Modelers create 3D characters and environments for animation and visual effects in films, television, video games, and other media.
This role is ideal for model makers who are passionate about bringing imaginary worlds and characters to life through their artistic and technical skills.
Job Duties:
- Designing 3D Models: Use specialized software to sculpt detailed characters, creatures, and environments for animation projects.
- Texturing and Rigging: Apply textures and create rigs to give models realistic appearances and prepare them for animation.
- Collaboration with Animators: Work closely with animators to ensure models meet movement and functionality requirements.
- Revising Models: Refine models based on feedback from directors, clients, or animation leads to achieve the desired final product.
- Staying Current with Technology: Keep up to date with the latest modeling software, techniques, and industry trends.
- Project Management: Participate in the planning of projects, ensuring that models are created efficiently and meet deadlines.
Requirements:
- Educational Background: A Bachelor’s degree in Computer Animation, Graphic Design, Fine Arts, or a related field is often required.
- Technical Skills: Proficiency in 3D modeling software such as Maya, 3ds Max, ZBrush, or Blender is essential.
- Artistic Talent: A strong sense of anatomy, proportion, and visual storytelling, coupled with excellent drawing and sculpting skills.
- Attention to Detail: Keen attention to detail to create complex and nuanced models.
- Teamwork: Ability to work effectively as part of a larger creative team.
- Problem-Solving: Adept at overcoming technical challenges and finding creative solutions during the modeling process.
Career Path and Growth:
This role offers the opportunity to work on a diverse range of animation projects, from feature films to indie games.
With experience, Animation Modelers can progress to lead modeler positions, supervise a team of modelers, or specialize in areas such as character design or environmental modeling.
Some may choose to further their career as art directors or move into teaching roles, sharing their expertise with the next generation of animators.
CAD Technician
Average Salary: $40,000 – $60,000 per year
CAD Technicians, or Computer-Aided Design Technicians, are skilled professionals who use CAD software to create technical drawings and plans for use in a variety of industries, including manufacturing, engineering, and construction.
This role is ideal for model makers who excel in transforming concepts into precise and detailed technical drawings and enjoy contributing to the creation of tangible products or structures.
Job Duties:
- Creating Technical Drawings: Use CAD software to draft detailed 2D or 3D designs, plans, and layouts for projects.
- Collaborating with Engineers: Work closely with engineers and architects to convert their conceptual designs into technical plans and drawings.
- Revising Designs: Update and modify existing drawings based on feedback to reflect changes in specifications or to improve the overall design.
- Ensuring Accuracy: Check the dimensions and tolerances of materials and components to ensure they meet project requirements.
- Document Management: Maintain an organized database of technical drawings and project documentation.
- Staying Current with Software: Continuously learn and adapt to new CAD software updates and technologies to improve design accuracy and efficiency.
Requirements:
- Educational Background: An Associate’s degree or certificate in CAD technology, drafting, or a related field is often required.
- Technical Proficiency: Proficient in CAD software such as AutoCAD, SolidWorks, or similar programs.
- Attention to Detail: High level of precision and attention to detail to produce accurate and error-free technical drawings.
- Understanding of Manufacturing Processes: Knowledge of manufacturing processes and construction methods is beneficial.
- Problem-Solving Skills: Ability to identify and resolve design issues during the drafting process.
Career Path and Growth:
As a CAD Technician, you have the opportunity to specialize in a particular industry or type of CAD work, such as mechanical, electrical, or civil drafting.
With experience, CAD Technicians can advance to roles such as CAD Manager, Design Engineer, or Project Manager.
Continuous learning and adapting to new technologies can open up opportunities in 3D printing, virtual reality modeling, and advanced manufacturing techniques.
Mold and Pattern Maker
Average Salary: $35,000 – $55,000 per year
Mold and Pattern Makers are skilled artisans who create molds and patterns that are essential in the manufacturing of various products, from toys and automotive parts to intricate components for the aerospace industry.
This role is ideal for model makers who appreciate precision and enjoy the hands-on process of creating the initial templates from which multiple copies can be cast or molded.
Job Duties:
- Designing and Crafting Molds: Use various materials and techniques to construct molds that will shape liquid or malleable materials into specific forms.
- Creating Patterns: Develop patterns that serve as the original models for the casting process, ensuring they meet precise specifications.
- Reading Blueprints: Interpret technical drawings and blueprints to accurately replicate the designs in the molds and patterns.
- Quality Control: Inspect completed molds and patterns for accuracy and adherence to the original design, making adjustments as necessary.
- Collaborating with Designers and Engineers: Work closely with designers and engineers to understand the requirements and limitations of the product design.
- Material Knowledge: Stay informed about the properties of various materials used in mold and pattern making, such as plastics, metals, and composites.
Requirements:
- Educational Background: A high school diploma or equivalent; further education or certification in manufacturing technology, industrial design, or a related field is beneficial.
- Technical Skills: Proficiency in using hand tools and machinery, such as CNC machines, used in the creation of molds and patterns.
- Attention to Detail: A keen eye for detail is crucial for ensuring the accuracy and quality of the final product.
- Creativity: Ability to think creatively to solve complex problems and improve mold and pattern-making processes.
- Dexterity: Excellent hand-eye coordination and manual dexterity for working with intricate designs and small components.
Career Path and Growth:
As a Mold and Pattern Maker, you have the opportunity to work on a wide range of projects across various industries.
With experience, you may advance to supervisory roles, specialize in a particular type of mold or pattern making, or even start your own business.
The demand for precise and high-quality molds and patterns ensures that skilled makers have a steady career with opportunities for growth and innovation.
Product Designer
Average Salary: $60,000 – $100,000 per year
Product Designers create and innovate products for various industries, from consumer electronics to automotive and beyond, making this an ideal role for model makers who enjoy transforming concepts into tangible items.
This role is excellent for those who have a knack for design, an eye for detail, and a passion for creating products that enhance people’s lives.
Job Duties:
- Conceptualizing Designs: Generate original product ideas, sketching out designs and creating prototypes to bring concepts to life.
- User Research: Conduct research to understand user needs, behaviors, and preferences to inform design decisions.
- Prototyping and Modeling: Create detailed prototypes and models to test and refine product designs before mass production.
- Collaborating with Teams: Work closely with engineers, marketing specialists, and manufacturers to ensure design feasibility and market fit.
- Utilizing Design Software: Employ advanced computer-aided design (CAD) software to create precise and functional designs.
- Staying Current: Keep up-to-date with the latest design trends, materials, and technologies to innovate and improve product offerings.
Requirements:
- Educational Background: A Bachelor’s degree in Industrial Design, Product Design, or a related field is highly recommended.
- Creative Skills: Strong creative ability to envision innovative products and bring them to fruition.
- Technical Proficiency: Proficiency with design software, such as CAD programs, and an understanding of manufacturing processes.
- Problem-Solving: Excellent problem-solving skills to overcome design challenges and improve product functionality.
- Attention to Detail: Acute attention to detail for creating precise and user-friendly designs.
- Communication and Collaboration: Strong communication skills for working with cross-functional teams and presenting design concepts effectively.
Career Path and Growth:
As a Product Designer, there are numerous opportunities for career advancement.
With experience and a portfolio of successful product designs, you can move into senior design roles, design management, or specialize in areas such as user experience (UX) design.
Additionally, skilled Product Designers may choose to start their own design consultancies or move into related fields such as innovation strategy.
Model Painter and Finisher
Average Salary: $35,000 – $55,000 per year
Model Painters and Finishers apply intricate paint jobs and finishing touches to scale models, ensuring that they are accurately detailed and aesthetically pleasing.
This role is ideal for model makers who have an eye for color and detail and enjoy bringing miniature creations to life.
Job Duties:
- Applying Paint and Finishes: Utilize various techniques to apply paint and finishes to models, ensuring a high level of detail and realism.
- Color Matching: Accurately match colors to specified designs or real-life references to maintain consistency and authenticity.
- Detailing: Add fine details to models, such as weathering, decals, and textures, to enhance their realism and visual appeal.
- Mixing Paints: Prepare and mix paints to create the desired shades and effects for each model.
- Quality Control: Inspect finished models for any defects or discrepancies and perform touch-ups as necessary.
- Collaboration: Work closely with model designers and builders to understand the specifications and requirements of each project.
Requirements:
- Technical Skill: Proficiency in painting and finishing techniques, including airbrushing, hand painting, and the application of decals.
- Attention to Detail: Strong attention to detail to accurately recreate the intended design and achieve high-quality finishes.
- Creative Flair: An artistic eye for color, shading, and texturing to bring models to life.
- Steady Hand: A steady hand and patience to work on intricate details and small-scale models.
- Material Knowledge: Knowledge of different paint types, finishes, and materials used in model making.
Career Path and Growth:
As a Model Painter and Finisher, you have the opportunity to work on a variety of projects, from historical miniatures to prototypes for new products.
With experience, you could move into supervisory roles, lead painting departments, or start your own business specializing in custom model finishes.
Advanced skill sets might also open opportunities in industries such as film, television, and video game design, where model making and finishing skills are in demand for creating detailed props and set pieces.
Prototype Fabricator
Average Salary: $40,000 – $60,000 per year
Prototype Fabricators are skilled craftspeople who create physical models and prototypes for a wide range of industries, including automotive, aerospace, consumer products, and more.
This role is ideal for model makers who enjoy bringing designs and concepts to life through meticulous crafting and fabrication techniques.
Job Duties:
- Creating Physical Models: Construct accurate and detailed prototypes from a variety of materials, such as plastics, metals, and composite materials.
- Interpreting Blueprints: Read and understand engineering drawings and specifications to accurately fabricate models and components.
- Using Specialized Equipment: Operate machinery and tools, including 3D printers, CNC machines, lathes, and milling machines, to create prototypes.
- Collaborating with Design Teams: Work closely with designers and engineers to refine prototypes and make adjustments based on feedback.
- Testing and Evaluation: Assist in the testing of prototypes to assess their functionality, durability, and performance.
- Problem-Solving: Apply creative solutions to overcome challenges in the prototyping process and ensure the highest quality results.
Requirements:
- Technical Education: A degree or certificate in industrial design, mechanical engineering technology, or a related field is often required.
- Hands-On Skills: Proficiency in using hand tools, machinery, and technology for model making and prototype development.
- Attention to Detail: Ability to produce precise and accurate work that meets strict specifications and quality standards.
- Material Knowledge: Familiarity with a wide range of materials and the appropriate methods for their use in prototyping.
- Collaboration: Strong teamwork skills to work effectively with other professionals in a multidisciplinary environment.
Career Path and Growth:
As a Prototype Fabricator, you have the opportunity to work on innovative projects across various industries.
With experience, Prototype Fabricators can become lead fabricators, move into design or engineering roles, or specialize in advanced fabrication technologies.
The role is critical in the product development process and offers a rewarding career for those with a passion for creating and innovating.
Toy Model Creator
Average Salary: $40,000 – $60,000 per year
Toy Model Creators design and construct toy prototypes and models, often working for toy manufacturers or as freelancers.
This role is ideal for individuals who are passionate about bringing joy to children and adults alike through the art of model making.
Job Duties:
- Designing Prototypes: Create detailed prototypes of toys, ensuring they are both appealing and functional.
- Material Selection: Choose appropriate materials for the construction of durable and safe toy models.
- 3D Modeling: Use software to design toys and prepare models for production, including 3D printing processes.
- Collaborating with Teams: Work with design and marketing teams to ensure the toy’s concept meets brand standards and customer expectations.
- Testing Models: Conduct tests on prototypes to ensure they meet safety standards and playability requirements.
- Staying Informed: Keep up-to-date with the latest trends in the toy industry, including new materials, technologies, and consumer preferences.
Requirements:
- Educational Background: A degree or certificate in Industrial Design, Toy Design, Engineering, or a related field is beneficial.
- Creative Skills: Strong artistic and creative skills to envision and create engaging toy models.
- Technical Proficiency: Knowledge of 3D modeling software and other tools used in the design and creation of toy prototypes.
- Attention to Detail: Meticulous attention to detail to ensure the quality and safety of toy models.
- Problem-Solving: Ability to troubleshoot design issues and come up with innovative solutions.
Career Path and Growth:
As a Toy Model Creator, you have the opportunity to influence the play experiences of generations and bring innovative ideas to life.
With experience, one can move into senior design roles, specialize in particular types of toys (e.g., educational, electronic, collectibles), or start their own toy creation business.
This career also provides the satisfaction of seeing your creations enjoyed by consumers worldwide.
Props Master
Average Salary: $35,000 – $75,000 per year
Props Masters are essential in the film, television, and theater industries, responsible for sourcing, creating, and managing all the props that appear on screen or stage.
This role is ideal for model makers who have a keen eye for detail and a passion for storytelling through tangible objects.
Job Duties:
- Prop Acquisition: Source or craft the necessary props to fulfill the requirements of the script and the vision of the director and production designer.
- Prop Creation: Use various materials and techniques to create realistic or fantastical props that can withstand the rigors of production.
- Prop Management: Maintain an inventory of all props, ensuring they are in good condition and readily available for actors and scenes as needed.
- Collaboration with Production Team: Work closely with other departments to ensure props are consistent with the overall production design and contribute effectively to the story.
- On-Set Presence: Be available during filming or performances to manage props and address any issues that may arise.
- Prop Budgeting: Manage the props budget, ensuring the best use of resources to achieve the desired effect without overspending.
Requirements:
- Artistic Skills: Strong artistic abilities and familiarity with various construction and manufacturing techniques to create a wide range of props.
- Attention to Detail: Keen attention to detail to ensure props are period-accurate, functional, and visually coherent within the production.
- Resourcefulness: Ability to source or create props within tight deadlines and budgets, often requiring creative problem-solving skills.
- Organization: Excellent organizational skills to manage large inventories of props and track their use throughout production.
- Communication Skills: Strong verbal and written communication skills for effective collaboration with other departments and team members.
Career Path and Growth:
As a Props Master, there are opportunities to work on a variety of productions, ranging from small independent projects to large-scale blockbusters.
With experience, a Props Master can move on to larger, more complex productions, become a head of the props department, or specialize in a particular type of prop making.
Some may even transition into production design or art direction roles for further career development.
Fine Art Restorer
Average Salary: $30,000 – $60,000 per year
Fine Art Restorers specialize in the conservation and restoration of artworks, ensuring that the cultural and aesthetic value of each piece is preserved for future generations.
This role is perfect for model makers who have an appreciation for art history and possess meticulous handiwork skills.
Job Duties:
- Assessing Artwork Condition: Examine pieces to determine the extent of damage or deterioration and the necessary restoration work.
- Restoration Techniques: Apply various techniques to clean, repair, and conserve paintings, sculptures, and other artworks.
- Researching Art History: Investigate the historical context and original materials used to ensure accurate restoration.
- Documentation: Keep detailed records of the restoration process, materials used, and any changes made to the artwork.
- Preventative Conservation: Advise on and implement measures to protect art from future damage.
- Continual Learning: Stay abreast of the latest conservation methods and materials in the field of fine art restoration.
Requirements:
- Educational Background: A Bachelor’s or Master’s degree in Art Conservation, Fine Arts, Art History, or a related field is often required.
- Attention to Detail: Exceptional fine motor skills and attention to detail for precise restoration work.
- Knowledge of Art Techniques: A comprehensive understanding of art techniques and materials used throughout history.
- Patience and Perseverance: The restoration process can be lengthy and delicate, requiring a patient and steady hand.
- Problem-Solving Skills: Ability to address unexpected challenges that may arise during the restoration process.
Career Path and Growth:
As a Fine Art Restorer, you have the opportunity to work on a diverse array of artworks from different eras, potentially leading to specialization in a particular type of art or period.
With experience, restorers can advance to supervisory roles within conservation departments, lead major restoration projects, or open their own private practices.
There is also the potential to work with museums, galleries, and private collectors around the world.
Scale Model Builder for Film & Television
Average Salary: $40,000 – $60,000 per year
Scale Model Builders for Film & Television are skilled artisans who create detailed miniatures and models used in cinematic productions.
These models are often critical for achieving realistic visual effects and are used in place of full-sized sets or CGI.
This role is ideal for model makers who have a keen interest in the film and television industry and enjoy bringing miniature worlds to life.
Job Duties:
- Creating Detailed Miniatures: Construct accurate and detailed scale models of sets, landscapes, vehicles, and other props as required by the production.
- Interpreting Blueprints: Read and interpret blueprints, sketches, and concept art to build models to the correct scale and specification.
- Collaborating with Production Teams: Work closely with directors, production designers, and visual effects teams to ensure models meet the creative vision of the project.
- Applying Finishing Touches: Paint and finish models with textures and details that mimic real-life objects and environments.
- Problem-Solving: Develop innovative solutions for creating realistic effects using models and miniatures.
- Managing Time and Resources: Complete projects within deadlines and budget constraints, often working on multiple tasks simultaneously.
Requirements:
- Educational Background: A degree or diploma in Fine Arts, Model Making, Sculpture, or a related field is beneficial.
- Technical Skills: Proficiency in using a wide range of tools and materials, including plastics, resins, and digital fabrication technologies.
- Attention to Detail: Exceptional attention to detail to ensure the highest level of realism in models.
- Artistic Talent: Strong artistic skills, including sculpting, painting, and understanding of scale and proportion.
- Collaboration: Ability to work effectively with others in a high-pressure creative environment.
Career Path and Growth:
Starting as a Scale Model Builder for Film & Television provides a unique opportunity to contribute to the magic of movies and TV shows.
With experience, model makers can advance to lead positions, supervising teams or specializing in particular types of model making.
Some may even transition into production design or visual effects roles, expanding their influence in the filmmaking process.
Automotive Clay Modeler
Average Salary: $50,000 – $70,000 per year
Automotive Clay Modelers are skilled artisans who create full-scale clay models of vehicles for the automotive industry, providing a tangible representation of design concepts.
This role is ideal for model makers who have a passion for cars and a keen eye for design and aesthetics.
Job Duties:
- Creating Full-Scale Models: Craft detailed and accurate full-scale clay models of vehicles based on design specifications and sketches.
- Collaborating with Designers: Work closely with automotive designers to understand and interpret their visions into physical models.
- Refining Models: Continuously refine and adjust clay models to meet the exact design requirements and to incorporate feedback from design teams.
- Using Specialized Tools: Employ a range of hand tools and machinery to sculpt and perfect the model’s surface and details.
- Applying Finishes: Apply various finishes to the clay model to simulate different materials and textures as required by the design team.
- Staying Updated: Keep abreast of the latest automotive design trends, materials, and modeling techniques.
Requirements:
- Educational Background: A degree or certification in Industrial Design, Sculpture, Automotive Design, or a related field is often preferred.
- Technical Skills: Proficiency in using various hand tools, sculpting materials, and possibly CAD software for precision work.
- Attention to Detail: Exceptional attention to detail to accurately translate complex designs into 3D clay models.
- Artistic Ability: A strong sense of form, shape, and aesthetics to create visually appealing models.
- Teamwork: Ability to work effectively in a team and communicate with designers and engineers.
Career Path and Growth:
Starting as an Automotive Clay Modeler provides a unique opportunity to contribute to the design and development of new vehicles.
With experience, modelers can advance to lead modeler positions, supervise teams, or specialize in high-end concept modeling.
They may also progress into automotive design roles or consultancy work within the industry.
Medical Prosthetics Designer
Average Salary: $60,000 – $85,000 per year
Medical Prosthetics Designers are skilled professionals who specialize in creating artificial limbs and body parts for patients who have lost them due to injury, disease, or congenital conditions.
This role is ideal for those with a passion for model making and a desire to improve the quality of life for individuals through innovative design and technology.
Job Duties:
- Designing Custom Prosthetics: Create tailored prosthetic devices that meet the specific needs and anatomies of patients, ensuring comfort and functionality.
- Material Selection: Choose appropriate materials and components for prosthetics, considering durability, flexibility, weight, and compatibility with the human body.
- Collaborating with Healthcare Professionals: Work closely with doctors, surgeons, and therapists to develop prosthetic solutions that align with medical requirements.
- Prototyping and Testing: Develop prototypes of prosthetic devices and conduct rigorous testing to ensure safety and efficacy before final production.
- Utilizing 3D Modeling and Printing: Employ advanced techniques such as computer-aided design (CAD) and 3D printing to create precise and customized prosthetics.
- Staying Abreast of Technological Advances: Keep up-to-date with the latest advancements in medical technology, materials science, and biomechanics to enhance prosthetic design.
Requirements:
- Educational Background: A Bachelor’s degree in Biomedical Engineering, Prosthetics and Orthotics, or a related field is required. Master’s degree is often preferred.
- Technical Skills: Proficiency in CAD software, 3D modeling, and understanding of manufacturing processes for prosthetic devices.
- Analytical Thinking: Ability to analyze and interpret complex anatomical data and translate it into functional design requirements.
- Attention to Detail: Keen eye for detail to ensure prosthetic devices are crafted to precise specifications and meet high-quality standards.
- Empathy and Communication: Strong interpersonal skills to effectively communicate with patients and understand their needs and concerns.
Career Path and Growth:
Medical Prosthetics Designers have the opportunity to directly impact the lives of individuals by providing them with the means to regain mobility and function.
As they gain experience, designers can advance to lead design teams, specialize in cutting-edge prosthetic technologies, or engage in research and development to create the next generation of prosthetic devices.
Model Shop Supervisor
Average Salary: $45,000 – $70,000 per year
Model Shop Supervisors oversee the operations of model-making workshops, ensuring the timely production of high-quality models for various industries, such as architecture, product design, or entertainment.
This role is ideal for model makers who have a passion for leading teams, coordinating projects, and maintaining high standards in model fabrication.
Job Duties:
- Managing Workshop Operations: Oversee the daily activities of the model shop, ensuring that projects are completed on time and within budget.
- Quality Control: Implement and maintain high-quality standards for all models produced, ensuring they meet client specifications.
- Team Leadership: Lead and develop a team of model makers, providing guidance and support to ensure a collaborative and efficient work environment.
- Project Coordination: Work closely with clients and designers to understand project requirements and coordinate the workflow to meet deadlines.
- Resource Management: Manage materials, tools, and equipment, ensuring the model shop is well-stocked and that machinery is maintained.
- Process Improvement: Continuously seek ways to improve the efficiency and quality of model production through innovative techniques and technologies.
Requirements:
- Educational Background: A degree in Industrial Design, Model Making, or a related field is preferred, along with significant experience in model making.
- Leadership Skills: Proven ability to lead a team, with strong organizational and managerial skills.
- Technical Expertise: Proficient in model-making techniques, including traditional craftsmanship and digital fabrication methods.
- Problem-Solving: Ability to troubleshoot and resolve issues related to model design and fabrication.
- Attention to Detail: A keen eye for detail to ensure the highest quality of workmanship in model production.
Career Path and Growth:
As a Model Shop Supervisor, there is potential for career growth into higher management positions within the industry.
With experience, supervisors may take on more significant projects, establish their own model-making businesses, or become consultants for complex and large-scale model productions.
Stop Motion Animator
Average Salary: $40,000 – $60,000 per year
Stop Motion Animators create frame-by-frame animated sequences using physical models such as puppets, clay figures, or other tangible materials.
This role is ideal for model makers who have a knack for storytelling and bringing inanimate objects to life through meticulous manipulation and photography.
Job Duties:
- Crafting Animation Sequences: Carefully move and photograph models frame by frame to create the illusion of movement in stop motion animation projects.
- Model and Set Design: Collaborate in the design and creation of models, sets, and props required for stop motion animation.
- Editing Footage: Work with editing software to piece together frames, ensuring smooth and coherent animation sequences.
- Storyboarding: Translate scripts and ideas into visual storyboards, planning out each scene and sequence for the animation.
- Collaboration: Work closely with directors, cinematographers, and other animators to achieve the desired artistic vision.
- Technical Problem-Solving: Develop innovative solutions to animate challenging scenes and effects within the constraints of stop motion.
Requirements:
- Educational Background: A degree in Animation, Film, Fine Arts, or a related field is beneficial, although not always required if a strong portfolio is presented.
- Artistic Skills: Proficient in model making, sculpting, and a good eye for detail, composition, and color.
- Technical Proficiency: Familiarity with stop motion animation software, cameras, lighting, and editing tools.
- Patience and Precision: Ability to perform repetitive tasks with a high level of precision over long periods.
- Creativity: A strong sense of storytelling, timing, and character performance to create engaging animations.
Career Path and Growth:
Stop Motion Animators have the opportunity to work on a variety of projects, from commercials and television series to feature films and online content.
With experience, animators can advance to lead animator roles, direct their own projects, or specialize in particular aspects of stop motion, such as model making or cinematography, further refining their craft and reputation in the industry.
CAD Modeler
Average Salary: $45,000 – $65,000 per year
CAD Modelers, or Computer-Aided Design Modelers, create detailed 3D models and technical drawings for manufacturing, engineering, and design processes.
This role is ideal for model makers who have a keen interest in precision and enjoy transforming concepts into tangible, highly detailed models.
Job Duties:
- Creating Detailed Models: Produce accurate 3D models and 2D drawings using CAD software for various applications, including prototyping, manufacturing, and visualization.
- Interpreting Blueprints: Convert hand-drawn sketches or blueprints into precise digital models, ensuring all specifications are met.
- Collaborating with Engineers and Designers: Work closely with engineering and design teams to understand project requirements and provide technical input to enhance product designs.
- Revising Models: Make adjustments to CAD models according to feedback from testing, client input, or to improve manufacturability.
- Maintaining Documentation: Keep detailed records of design files, revisions, and project documentation for future reference and compliance with industry standards.
- Staying Current with Technology: Continuously learn and adapt to new CAD software and technologies to improve modeling efficiency and accuracy.
Requirements:
- Educational Background: An Associate’s degree in CAD drafting, a Bachelor’s degree in Engineering, Industrial Design, or a related field is often required.
- Technical Proficiency: Strong skills in CAD software, such as AutoCAD, SolidWorks, or similar programs.
- Attention to Detail: Exceptional attention to detail to create precise and accurate models that meet all specifications.
- Problem-Solving: Ability to identify issues in designs and propose practical solutions.
- Communication Skills: Good verbal and written communication abilities to interact effectively with team members and clients.
- Time Management: Capable of managing multiple projects and meeting tight deadlines.
Career Path and Growth:
CAD Modelers play a crucial role in the design and manufacturing process.
With experience, they can advance to senior modeler positions, specialize in industries such as aerospace or automotive, or pursue roles in CAD management or engineering.
There are also opportunities to contribute to innovative projects, like advanced robotics or renewable energy systems, as technology progresses.
Conclusion
There you have it.
A comprehensive list of the most exciting jobs for model makers.
With a vast array of possibilities, there’s sure to be a fantastic job for every passionate model maker.
Don’t hesitate, take the plunge and pursue your dreams of working with models on a daily basis.
Always bear in mind: Turning your passion into a career is never out of reach. Your ideal profession waits.
Joyful Jobs: Careers That Combine Fun and Finance
Career Gold: The Definitive List of Highest Paying Jobs in 2025!
Extraordinary Employment: The Strangest Jobs on the Planet
The Joy of Earning: Enjoyable Careers That Keep Smiles Coming