Lean Manufacturing Manager Job Description [Updated for 2025]
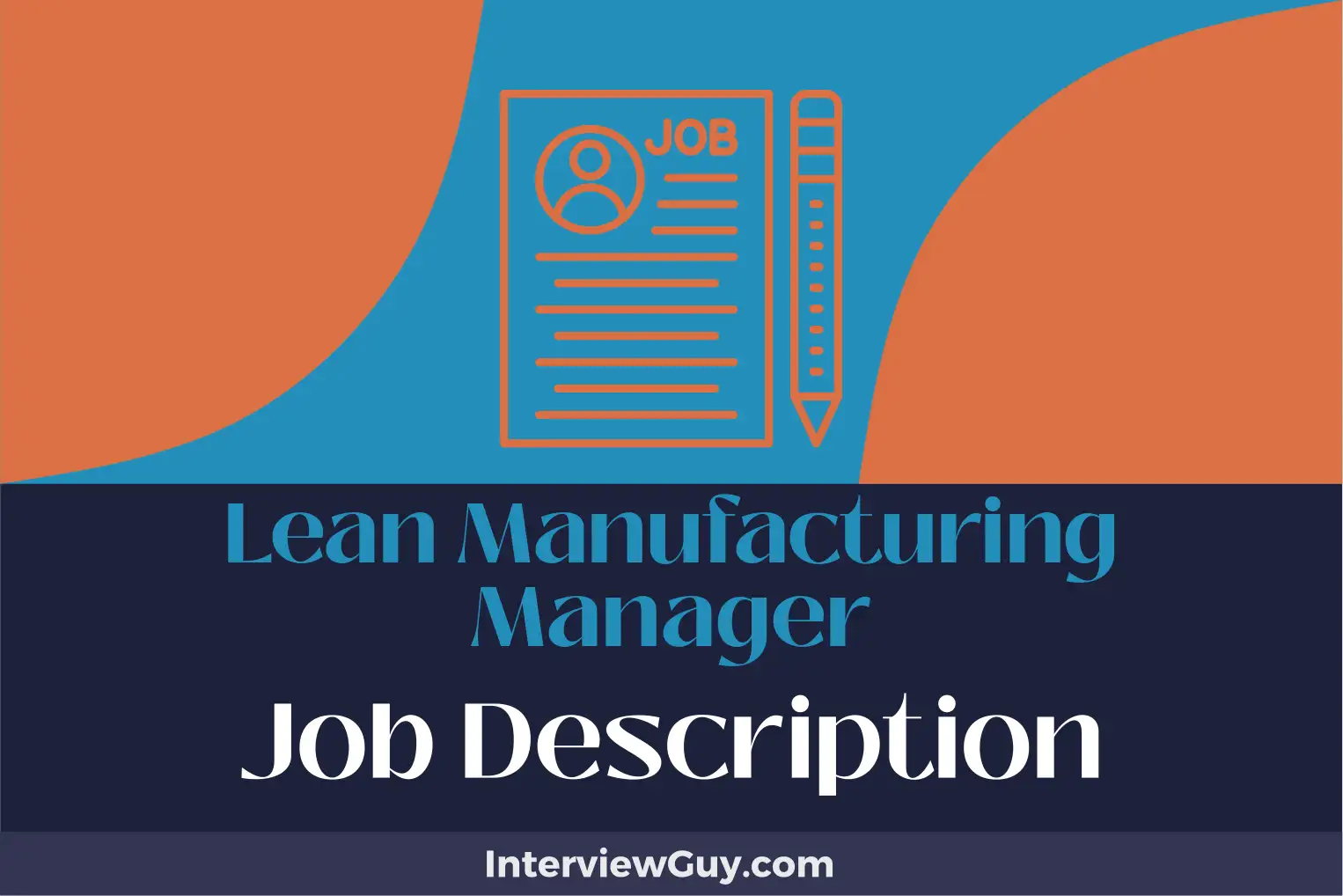
In the era of streamlined production, the role of a Lean Manufacturing Manager has become increasingly crucial.
As industries evolve towards more efficiency, the demand for savvy individuals who can implement, manage, and optimize lean manufacturing principles grows exponentially.
But let’s delve deeper: What’s actually expected from a Lean Manufacturing Manager?
Whether you are:
- A job seeker trying to understand the nuances of this role,
- A hiring manager formulating the perfect candidate profile,
- Or simply fascinated by the intricacies of lean manufacturing,
You’re in the right place.
Today, we are presenting a customizable Lean Manufacturing Manager job description template, designed for easy posting on job boards or career sites.
Let’s dive right in.
Lean Manufacturing Manager Duties and Responsibilities
Lean Manufacturing Managers are primarily responsible for improving the efficiency of manufacturing processes and making them as waste-free as possible.
They use lean principles to maximize productivity while minimizing costs.
Their daily duties and responsibilities include:
- Identify and implement opportunities for process improvement and cost reduction
- Lead lean manufacturing initiatives and projects within the manufacturing facility
- Conduct regular lean audits and monitor the progress of lean initiatives
- Develop and maintain standard work procedures and lean manufacturing tools such as value stream maps and process flow diagrams
- Train and mentor employees in lean manufacturing principles and practices
- Collaborate with production teams to identify bottlenecks and balance product flow
- Ensure compliance with health and safety regulations
- Monitor the quality of products and work to reduce defects and waste
- Coordinate with supply chain and logistics to optimize inventory and delivery
Lean Manufacturing Manager Job Description Template
Job Brief
We are seeking a highly skilled Lean Manufacturing Manager to implement, manage, and optimize lean manufacturing processes in our organization.
You will be responsible for reducing waste, increasing productivity, and promoting the efficient use of resources.
The successful candidate will have strong leadership capabilities, analytical skills, and a comprehensive understanding of lean manufacturing principles and methodologies.
Responsibilities
- Implement and drive lean manufacturing strategies to optimize efficiency and reduce waste
- Develop and monitor key performance indicators to track progress
- Train and mentor employees on lean manufacturing principles
- Collaborate with other departments to integrate lean methodologies across the organization
- Conduct regular audits to ensure compliance with lean principles
- Identify opportunities for continuous improvement and lead associated initiatives
- Develop standard operating procedures to support lean manufacturing goals
- Coordinate with quality and production teams to address and mitigate any quality issues
Qualifications
- Proven experience as a Lean Manufacturing Manager or similar role
- Strong understanding of lean manufacturing principles and methodologies
- Excellent analytical and problem-solving abilities
- Strong leadership and team management skills
- Exceptional communication and interpersonal skills
- BSc/BA in Business Administration, Engineering, or relevant field; MSc/MA will be a plus
- Lean Six Sigma certification is preferred
Benefits
- 401(k)
- Health insurance
- Dental insurance
- Retirement plan
- Paid time off
- Professional development opportunities
Additional Information
- Job Title: Lean Manufacturing Manager
- Work Environment: This role generally operates in a manufacturing setting and may require some travel for training or conferences.
- Reporting Structure: The Lean Manufacturing Manager reports directly to the Director of Operations or similar.
- Salary: Salary is based upon candidate experience and qualifications, as well as market and business considerations.
- Pay Range: $80,000 minimum to $120,000 maximum
- Location: [City, State] (specify the location or indicate if remote)
- Employment Type: Full-time
- Equal Opportunity Statement: We are an equal opportunity employer and value diversity at our company. We do not discriminate on the basis of race, religion, color, national origin, gender, sexual orientation, age, marital status, veteran status, or disability status.
- Application Instructions: Please submit your resume and a cover letter outlining your qualifications and experience to [email address or application portal].
What Does a Lean Manufacturing Manager Do?
A Lean Manufacturing Manager is a professional who works in manufacturing industries and is responsible for overseeing and implementing lean manufacturing strategies.
These strategies are intended to minimize waste, increase productivity, and improve overall efficiency and quality in a manufacturing setting.
The Lean Manufacturing Manager’s role is to lead the team towards the goal of continuous improvement.
They are responsible for identifying areas of waste or inefficiency in the manufacturing process and finding solutions to address these issues.
This involves conducting routine reviews and assessments of the manufacturing process, using lean tools and methodologies such as Value Stream Mapping, Kaizen, 5S, and Six Sigma.
Lean Manufacturing Managers also play a crucial role in training team members on lean principles and practices, ensuring everyone is aligned towards the same efficiency goals.
They work closely with various departments including production, engineering, quality, and logistics to ensure seamless integration of lean manufacturing strategies across the organization.
They also typically lead or participate in cross-functional teams to implement process improvements, often driving the change management process to ensure new procedures are adopted successfully.
In some cases, Lean Manufacturing Managers may be responsible for setting production targets, measuring performance against these targets, and analyzing any variances to understand the root cause and implement corrective actions.
The ultimate goal of a Lean Manufacturing Manager is to create a culture of continuous improvement within the organization, leading to more efficient processes, higher product quality, and increased customer satisfaction.
Lean Manufacturing Manager Qualifications and Skills
A Lean Manufacturing Manager should possess a range of technical and soft skills, along with specific industry knowledge to effectively manage operations, such as:
- Strong understanding and experience in Lean Manufacturing principles and methodologies to identify waste and improve efficiency.
- Exceptional leadership skills to guide and motivate the team towards achieving operational goals.
- Outstanding problem-solving abilities to address operational issues, reduce waste and optimize production processes.
- Excellent communication and interpersonal skills to liaise with different departments, stakeholders and employees at all levels.
- Strong analytical skills to evaluate production metrics, identify trends and make data-driven decisions.
- Ability to multitask and manage multiple projects at once, maintaining a high level of organization and attention to detail.
- Knowledge of safety regulations and standards in the manufacturing industry to ensure the wellbeing of staff and compliance with legal requirements.
- Experience with process improvement tools and software to effectively implement lean strategies and monitor their impact.
Lean Manufacturing Manager Experience Requirements
For the role of a Lean Manufacturing Manager, candidates generally need significant experience in manufacturing and process improvement methods.
Often, this starts with a bachelor’s degree in business, engineering, or a related field, followed by several years of experience in a manufacturing setting.
Entry-level candidates may have 1 to 3 years of experience in manufacturing roles, often gained through internships or part-time roles in manufacturing processes or operations.
They may have hands-on experience in understanding lean principles, managing waste, and implementing process improvements.
Candidates with 4 to 6 years of experience often have been employed in roles like Manufacturing Engineer, Quality Assurance Analyst or Process Improvement Specialist.
This allows them to gain an in-depth understanding of lean methodologies, Six Sigma, and other process improvement strategies.
Those with more than 7 years of experience generally possess extensive knowledge and expertise in lean manufacturing practices.
They should have a proven track record of success in leading and implementing lean transformation initiatives.
These candidates may also have leadership experience, having managed teams or departments, making them suitable for the managerial role.
In addition to practical experience, certifications like Certified Lean Six Sigma Black Belt or Lean Management certification can also be beneficial and may be required by some employers.
Lean Manufacturing Manager Education and Training Requirements
A Lean Manufacturing Manager typically holds a bachelor’s degree in industrial engineering, business, manufacturing, or a related field.
Some organizations prefer candidates with a master’s degree in business administration or industrial engineering.
Candidates should have a solid background in lean manufacturing principles, with proven experience in implementing these principles in a production environment.
Knowledge in quality assurance and productivity improvement strategies, like Six Sigma, is highly desirable.
Certification from a recognized lean manufacturing institution such as the Lean Manufacturing Institute, can provide an edge for candidates.
This certification validates the individual’s understanding of lean principles and ability to apply them in the real world.
Additional skills required for this role often include proficiency in statistical analysis and project management, experience with manufacturing software systems, and strong leadership abilities.
Furthermore, some companies may require Lean Manufacturing Managers to engage in ongoing education and training to stay updated with the latest lean manufacturing methodologies and technologies.
This continuous learning also emphasizes a candidate’s commitment to maintaining efficiency and productivity in the manufacturing process.
Lean Manufacturing Manager Salary Expectations
A Lean Manufacturing Manager can expect to earn an average salary of $105,000 (USD) per year.
However, this figure can fluctuate based on factors such as years of experience in the field, educational background, and the geographical location of the job.
Additionally, the size and industry of the employing company may also affect the salary.
Lean Manufacturing Manager Job Description FAQs
What skills does a Lean Manufacturing Manager need?
A Lean Manufacturing Manager should have strong leadership skills to manage the workforce efficiently.
They should possess problem-solving skills to identify issues in the production process and implement effective solutions.
Having a good understanding of lean manufacturing principles and methodologies is crucial.
The ability to communicate and implement these principles to the team is also essential.
Do Lean Manufacturing Managers need a degree?
Yes, most Lean Manufacturing Managers have a bachelor’s degree in industrial engineering, manufacturing engineering, or a related field.
Some companies may prefer candidates with a Master’s degree in Business Administration or Engineering.
Industry-specific certifications related to lean manufacturing or Six Sigma can also be beneficial.
What should you look for in a Lean Manufacturing Manager’s resume?
A Lean Manufacturing Manager’s resume should highlight their education, relevant experience in manufacturing, and any certifications related to lean manufacturing or process improvement.
Look for demonstrated skills in implementing lean principles, leading teams, and improving manufacturing processes.
Results of their previous lean initiatives, like reduced waste, improved productivity, or increased efficiency, can be strong indicators of their capabilities.
What qualities make a good Lean Manufacturing Manager?
A good Lean Manufacturing Manager should be a strategic thinker and a strong leader.
They must have a thorough understanding of lean principles and the ability to apply them to improve production processes.
They should be skilled at problem-solving, decision-making, and communication to effectively lead their teams and implement improvements.
A passion for continuous learning and staying up-to-date with the latest industry trends can also be beneficial.
Is it challenging to hire a Lean Manufacturing Manager?
The challenge of hiring a Lean Manufacturing Manager can depend on various factors, including the specific skill set required, the competitiveness of the job market, and the attractiveness of the compensation package offered.
It can be particularly challenging to find candidates with the right mix of leadership skills, technical expertise, and practical experience in lean manufacturing.
It is beneficial to have a well-defined job description and a solid recruitment strategy to attract the right candidates.
Conclusion
And there you have it.
Today, we unveiled the true essence of being a lean manufacturing manager.
Guess what?
It’s not just about reducing waste.
It’s about optimizing productivity and efficiency, one process at a time.
With our indispensable lean manufacturing manager job description template and real-world examples, you’re ready to take the next step.
But why stop there?
Delve further with our job description generator. It’s your pathway to precision-crafted job listings or refining your resume to perfection.
Remember:
Every process improvement is part of a larger efficiency strategy.
Let’s shape that future. Together.
How to Become a Lean Manufacturing Manager (Complete Guide)
Elite Employment: The Most Prestigious Jobs to Elevate Your Life
The Modern Workforce: Trending Jobs That Are Changing the Game
Work That Doesn’t Feel Like Work: Enjoyable Jobs with Great Pay
Tech-Proof Professions: The Jobs That Keep Humanity in Control