Maintenance and Reliability Manager Job Description [Updated for 2025]
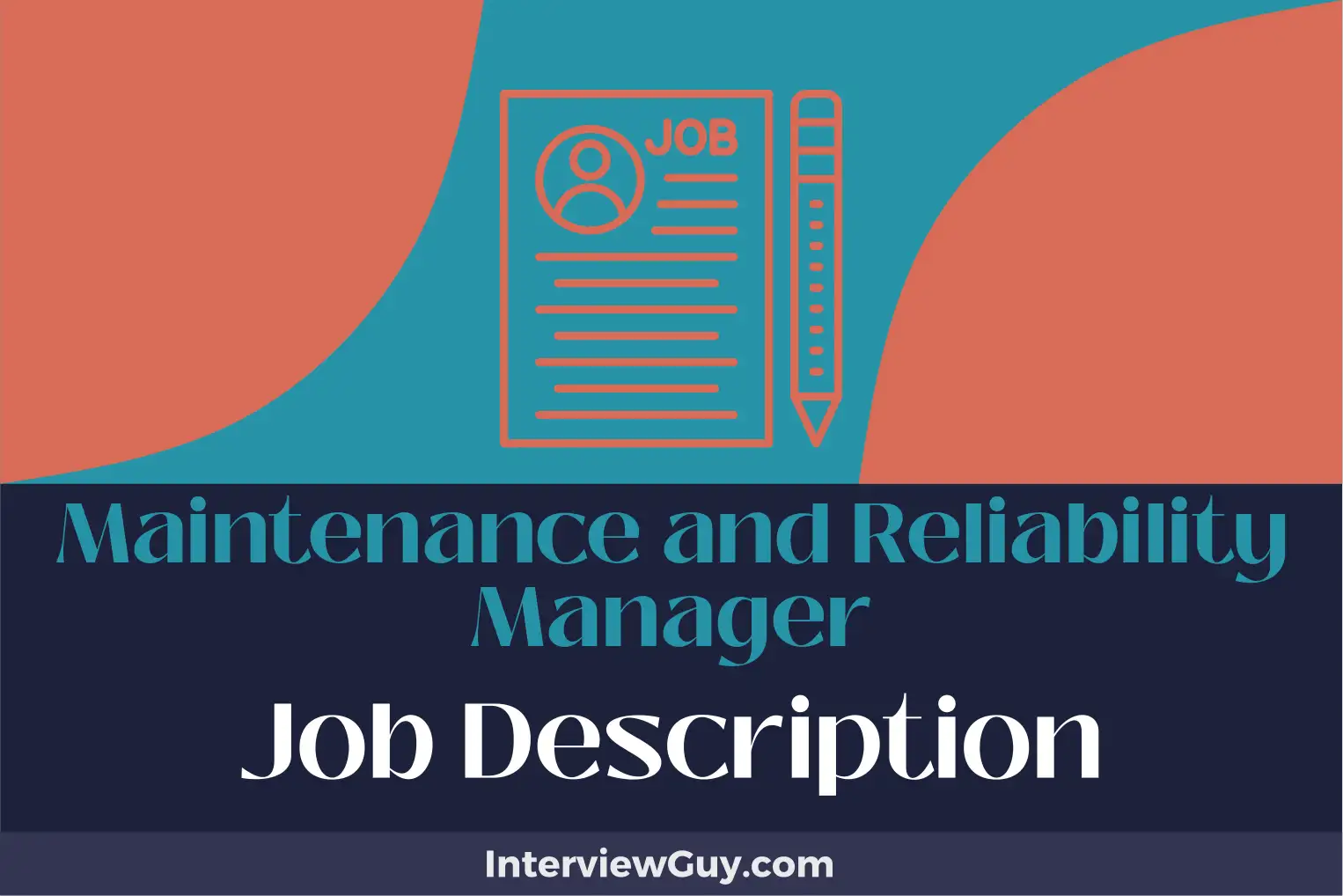
In the modern industrial landscape, the demand for Maintenance and Reliability Managers is growing steadily.
With the advancements in technology, the call for skilled professionals who can maintain, optimize, and ensure the reliability of machinery and equipment is escalating.
But let’s delve into the specifics: What’s truly expected from a Maintenance and Reliability Manager?
Whether you are:
- A job seeker trying to understand the core of this role,
- A hiring manager drafting the perfect candidate profile,
- Or simply fascinated by the operational side of industrial maintenance,
You’ve come to the right place.
Today, we present a customizable Maintenance and Reliability Manager job description template, designed for effortless posting on job boards or career sites.
Let’s delve right into it.
Maintenance and Reliability Manager Duties and Responsibilities
Maintenance and Reliability Managers play a significant role in the management and execution of maintenance tasks, reliability of equipment and systems, and overall operational efficiency in a variety of industries.
Their primary responsibilities include:
- Overseeing the maintenance of all equipment and systems in the facility to ensure optimal operation and performance
- Developing and implementing maintenance strategies, procedures, and methods
- Conducting routine inspections of equipment and systems to identify and resolve issues
- Coordinating and directing all maintenance personnel and vendors
- Creating and managing preventive and predictive maintenance programs
- Leading and managing reliability improvement initiatives and programs
- Monitoring equipment inventory and placing orders when necessary
- Ensuring compliance with health and safety regulations
- Developing and managing the maintenance budget
- Conducting performance evaluations and providing training and development opportunities for maintenance staff
- Working closely with other departments to coordinate maintenance activities
Maintenance and Reliability Manager Job Description Template
Job Brief
We are seeking a diligent Maintenance and Reliability Manager to oversee and coordinate the successful maintenance and repair initiatives within our company.
Your responsibilities will include scheduling and supervising maintenance tasks, implementing safety protocols, and ensuring the reliability and efficiency of our machinery and systems.
Our ideal candidate has a strong understanding of maintenance procedures, equipment operations, and team management.
Ultimately, the role of the Maintenance and Reliability Manager is to ensure that our machinery and equipment run smoothly and reliably to support our business operations.
Responsibilities
- Oversee all maintenance and repair tasks within the organization
- Develop and implement maintenance strategies, procedures and methods
- Monitor and control maintenance costs
- Carry out routine inspections to assess the condition of facilities and equipment
- Manage and lead a team of maintenance technicians
- Ensure safety standards and compliance with regulations
- Diagnose breakdown problems and implement solutions
- Arrange specialist procurement of fixtures, fittings or components
- Control maintenance tools, stores and equipment
Qualifications
- Proven work experience as a Maintenance Manager or similar role
- Experience in planning maintenance operations
- Solid understanding of technical aspects of plumbing, carpentry, electrical systems etc.
- Working knowledge of facilities machines and equipment
- Ability to keep track of and report on activity
- Excellent communication and interpersonal skills
- Outstanding organizational and leadership abilities
- BSc/Ba in business administration or facility management will be a plus
Benefits
- 401(k)
- Health insurance
- Dental insurance
- Retirement plan
- Paid time off
- Professional development opportunities
Additional Information
- Job Title: Maintenance and Reliability Manager
- Work Environment: This role requires work in both office and industrial settings. Some travel may be required for facility inspections or vendor meetings.
- Reporting Structure: Reports to the General Manager or Operations Director.
- Salary: Salary is based upon candidate experience and qualifications, as well as market and business considerations.
- Pay Range: $70,000 minimum to $110,000 maximum
- Location: [City, State] (specify the location or indicate if remote)
- Employment Type: Full-time
- Equal Opportunity Statement: We are an equal opportunity employer and value diversity at our company. We do not discriminate on the basis of race, religion, color, national origin, gender, sexual orientation, age, marital status, veteran status, or disability status.
- Application Instructions: Please submit your resume and a cover letter outlining your qualifications and experience to [email address or application portal].
What Does a Maintenance and Reliability Manager Do?
Maintenance and Reliability Managers typically work for manufacturing or industrial companies, although they may also find employment in various other sectors such as transportation, construction, and energy.
Their primary role is to oversee and ensure the smooth and efficient maintenance and operation of machinery, equipment, and facilities in the organization.
They are responsible for planning, directing, and coordinating the activities of the maintenance team.
Their job is to develop and implement maintenance procedures, strategies, and policies to increase reliability and manageability of machinery and equipment.
They also conduct routine inspections, identify and rectify faults, and manage shutdowns and start-ups of equipment to minimize disruption to production.
Maintenance and Reliability Managers also have a crucial role in setting and controlling maintenance budgets, inventory management of spare parts, and liaising with external suppliers and contractors.
They use data analysis tools to monitor machine performance and effectiveness of maintenance works, ensuring that all machinery complies with safety and environmental regulations.
In some cases, they may also be involved in training staff on equipment use and safety procedures.
They must be proactive in identifying potential issues and implementing preventative measures to avoid costly and unsafe equipment failures.
Maintenance and Reliability Manager Qualifications and Skills
A Maintenance and Reliability Manager should have the following skills and qualifications to ensure the smooth operation and prolonged lifespan of company machinery and equipment:
- Technical knowledge and expertise to understand and manage complex machinery and equipment, and make necessary repairs or modifications.
- Excellent leadership and team management skills to supervise and guide the maintenance team effectively.
- Strong communication skills to coordinate with other departments, explain complex technical issues, and give clear instructions to team members.
- Detail-oriented to keep track of all maintenance work, identify potential issues before they become larger problems, and ensure all work meets high quality standards.
- Problem-solving skills to identify and resolve issues that arise during maintenance processes and implement preventive measures to avoid recurrence.
- Analytical skills to assess the efficiency of current systems and recommend improvements or replacements when necessary.
- Knowledge of safety regulations and procedures to ensure a safe working environment for all employees.
- Ability to manage budgets, prepare cost estimates, and ensure all maintenance activities stay within budget.
- Organizational skills to manage and prioritize multiple tasks and projects simultaneously.
Maintenance and Reliability Manager Experience Requirements
Entry-level candidates for the Maintenance and Reliability Manager role typically have 1 to 2 years of experience.
This experience is often acquired through roles such as Maintenance Technician, Reliability Engineer, or other similar roles within an industrial or manufacturing setting.
These professionals can also gain valuable experience through internships or apprenticeships in maintenance and reliability management.
Candidates with more than 3 years of experience often build their technical skills and deepen their understanding of maintenance and reliability management in roles such as Maintenance Supervisor or Reliability Analyst.
Individuals with more than 5 years of experience are generally seen as seasoned professionals in the field of maintenance and reliability management.
They might have managed small teams or projects and have experience with strategic planning, budgeting, and implementing preventive and predictive maintenance programs.
Those with over 10 years of experience are usually considered for senior leadership roles.
They often have a strong background in managing large teams and extensive projects, developing and implementing maintenance strategies, and making critical business decisions.
They may also have a track record of improving asset reliability and operational efficiency, alongside reducing maintenance costs.
Maintenance and Reliability Manager Education and Training Requirements
Maintenance and Reliability Managers typically hold a bachelor’s degree in engineering, business, or a related technical field.
Some employers may prefer candidates with a master’s degree, especially in business administration or industrial technology management.
In-depth knowledge of maintenance procedures, quality control, safety regulations, and project management are crucial for this role.
Familiarity with computerized maintenance management systems (CMMS) and predictive maintenance techniques is also desirable.
Several years of experience in a maintenance-related field is usually required, often including some management experience.
Certifications, though not always required, can prove advantageous.
These may include Certified Maintenance and Reliability Professional (CMRP), Certified Plant Engineer (CPE), or Certified Reliability Engineer (CRE) among others.
Continuous education and training to keep up with the latest industry standards and equipment are vital in this role.
This might be achieved through seminars, workshops, or additional courses.
Additionally, soft skills such as leadership, decision-making, and problem-solving abilities are highly valued.
Maintenance and Reliability Manager Salary Expectations
The average salary for a Maintenance and Reliability Manager is $92,000 (USD) per year.
However, the actual salary can greatly vary depending on the individual’s experience, educational qualifications, the size of the organization, and the geographical location.
Maintenance and Reliability Manager Job Description FAQs
What skills does a Maintenance and Reliability Manager need?
Maintenance and Reliability Managers should have strong analytical and problem-solving skills as they need to identify and resolve issues related to maintenance and reliability of equipment.
They should also have project management skills to manage maintenance projects efficiently.
Technical skills are necessary to understand the functioning of various equipment.
Additionally, they should possess leadership and interpersonal skills to manage and lead a team effectively.
Do Maintenance and Reliability Managers need a degree?
Most employers require a bachelor’s degree in engineering, business management, or a related field.
Some may prefer candidates with a master’s degree in business administration (MBA) or engineering.
Professional certifications in maintenance and reliability, such as Certified Maintenance and Reliability Professional (CMRP), can be beneficial.
What should you look for in a Maintenance and Reliability Manager’s resume?
When hiring a Maintenance and Reliability Manager, look for a degree in a relevant field and experience in managing maintenance tasks.
Check for their technical knowledge and experience with the type of machinery or equipment your company uses.
If they have certifications in maintenance and reliability, that’s a plus.
Their resume should demonstrate strong leadership skills and a track record of improving operational efficiency.
What qualities make a good Maintenance and Reliability Manager?
A good Maintenance and Reliability Manager is someone who can handle pressure, manage time effectively, and has excellent problem-solving skills.
They should have a thorough understanding of maintenance processes and be able to implement strategies to improve efficiency and reliability.
Good managers are proactive, can foresee potential issues, and act on them before they become problems.
They should also have strong leadership and communication skills to lead the maintenance team and convey complex technical information in a way that everyone can understand.
Is it difficult to hire Maintenance and Reliability Managers?
Hiring a Maintenance and Reliability Manager can be challenging as it requires someone with a unique blend of technical and managerial skills.
It may take some time to find a candidate who has the necessary education, experience, and certifications, as well as the soft skills needed to lead a team and manage complex maintenance projects.
Therefore, it’s crucial to have a well-planned recruiting strategy to attract qualified candidates.
Conclusion
And there you have it.
Today, we’ve delved into the intricate world of a Maintenance and Reliability Manager.
Surprise?
It’s not just about fixing machinery.
It’s about ensuring the smooth operation of business, one maintenance check at a time.
With our comprehensive Maintenance and Reliability Manager job description template and real-world examples, you’re well equipped to take the next step.
But why limit yourself?
Dig deeper with our job description generator. It’s your indispensable tool for crafting laser-precise job listings or optimizing your resume to perfection.
Remember:
Each maintenance task contributes to the overall business efficiency.
Let’s ensure that smooth operation. Together.
How to Become a Maintenance and Reliability Manager (Complete Guide)
On the Rise: The Latest Trending Jobs Taking Over
Big Opportunity Alert: Careers That Are in Serious Demand