Quality and Safety Coordinator Job Description [Updated for 2025]
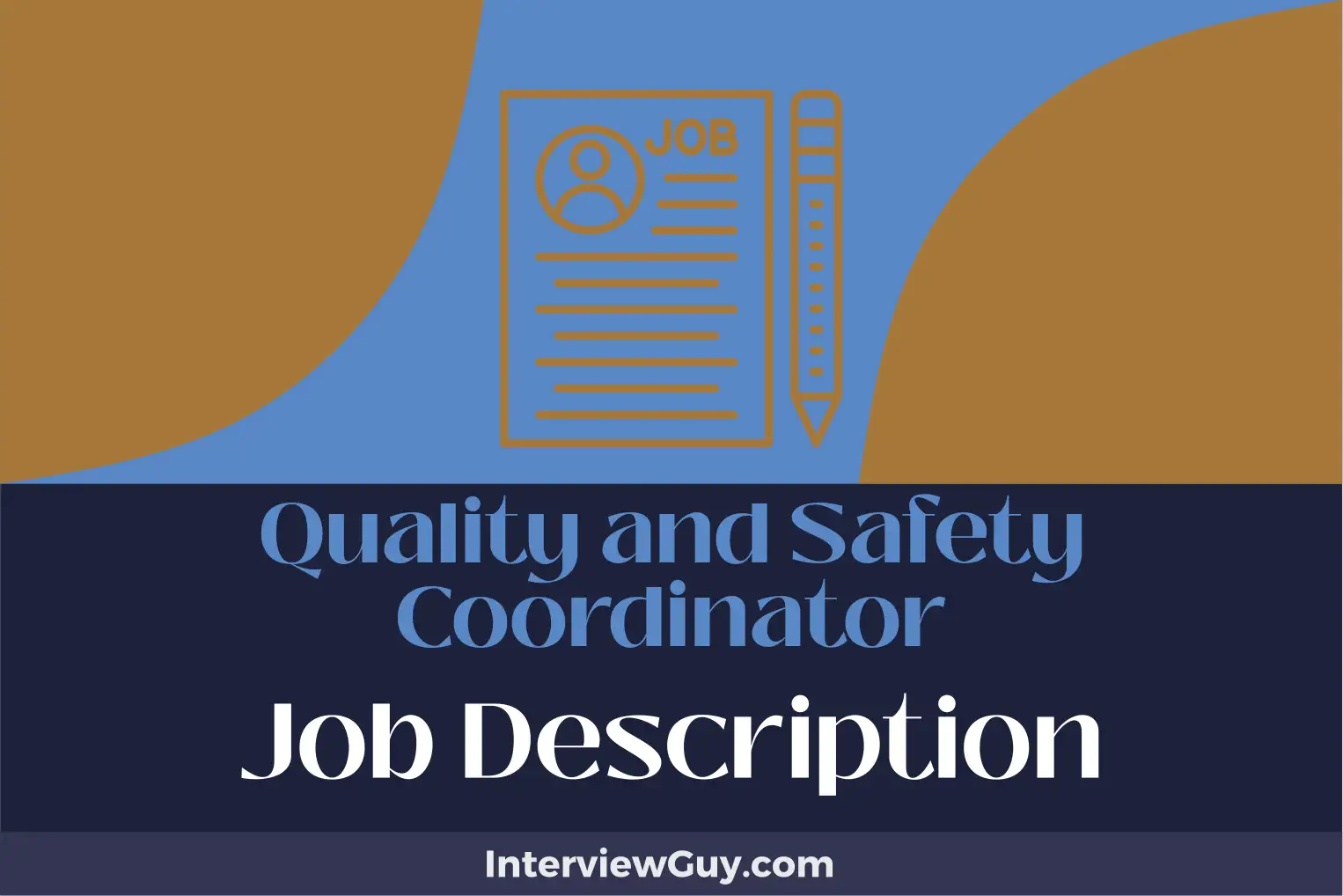
In the era of risk management, the role of Quality and Safety Coordinators has become critical.
As industries evolve, the demand for skilled professionals who can ensure, enhance, and uphold the quality and safety standards of an organization is on the rise.
But let’s delve deeper: What’s truly expected from a Quality and Safety Coordinator?
Whether you are:
- A job seeker wanting to understand the scope of this role,
- A hiring manager defining the perfect candidate,
- Or simply interested in the dynamics of quality and safety coordination,
You’re in the right place.
Today, we present a customizable Quality and Safety Coordinator job description template, designed for easy posting on job boards or career sites.
Let’s dive right into it.
Quality and Safety Coordinator Duties and Responsibilities
Quality and Safety Coordinators play a critical role in ensuring that an organization’s products or services meet established quality standards and safety regulations.
They manage and coordinate quality control programs, set up quality control systems, and implement safety initiatives to prevent accidents.
The duties and responsibilities of a Quality and Safety Coordinator include:
- Developing, implementing, and managing the organization’s quality control procedures
- Ensuring compliance with industry safety standards and regulations
- Conducting regular safety audits and inspections to identify potential hazards
- Developing and delivering training programs for employees about quality and safety policies
- Investigating any accidents, incidents, or non-compliance issues, and implementing corrective measures
- Monitoring and reviewing the performance of quality and safety systems to identify any areas for improvement
- Creating detailed reports on the results of quality control tests and safety inspections
- Participating in the development of new products or services to ensure they meet quality and safety standards
- Working with management to develop and implement strategic plans to improve quality and safety
- Maintaining a thorough understanding of all current local, state, and federal safety regulations
- Staying up to date with the latest developments and best practices in quality control and safety management
Quality and Safety Coordinator Job Description Template
Job Brief
We are seeking a dedicated Quality and Safety Coordinator to help us maintain the highest standards of safety and quality in our operations.
The successful candidate will be responsible for developing and implementing health, safety, and quality procedures, conducting regular inspections, identifying potential hazards, and ensuring compliance with local, state, and federal safety laws and regulations.
The ideal candidate will have a thorough understanding of quality assurance and safety regulations, excellent attention to detail, and strong leadership skills.
Responsibilities
- Develop, implement, and maintain health, safety, and quality procedures.
- Conduct regular inspections and risk assessments to identify potential hazards.
- Ensure compliance with local, state, and federal safety laws and regulations.
- Prepare and present reports on health, safety, and quality issues to management.
- Organize and conduct safety training programs for employees.
- Investigate accidents and incidents, identify root causes, and recommend corrective actions.
- Coordinate with management to implement changes and improvements in safety and quality procedures.
- Maintain records of safety-related incidents and responses.
- Monitor operations to ensure they meet quality standards.
Qualifications
- Proven experience as a Quality and Safety Coordinator or similar role.
- Knowledge of local, state, and federal safety laws and regulations.
- Excellent attention to detail and observation ability.
- Strong leadership and communication skills.
- Certification in occupational health and safety.
- Bachelor’s degree in safety management, engineering or relevant field is preferred.
- Proficiency in MS Office and data analysis software.
- Excellent problem-solving abilities.
Benefits
- 401(k) plan
- Health, vision, and dental insurance
- Life insurance
- Retirement plan
- Paid time off
- Professional development opportunities
Additional Information
- Job Title: Quality and Safety Coordinator
- Work Environment: This role typically works in an office setting but may require visits to various operation sites. Safety gear may be required during site visits.
- Reporting Structure: Reports to the Safety Manager or Director of Operations.
- Salary: Salary is dependent on experience and qualifications, as well as market and business considerations.
- Pay Range: $60,000 minimum to $85,000 maximum
- Location: [City, State] (specify the location or indicate if remote)
- Employment Type: Full-time
- Equal Opportunity Statement: We are an equal opportunity employer and value diversity at our company. We do not discriminate on the basis of race, religion, color, national origin, gender, sexual orientation, age, marital status, veteran status, or disability status.
- Application Instructions: Please submit your resume and a cover letter outlining your qualifications and experience to [email address or application portal].
What Does a Quality and Safety Coordinator Do?
Quality and Safety Coordinators work across various industries, ensuring that organizations comply with safety standards and deliver high-quality products or services.
They are responsible for creating and implementing safety procedures and protocols, ensuring the organization adheres to legal standards and in-house policies.
Their role involves conducting regular audits and inspections, identifying potential hazards, and implementing corrective actions to mitigate risks.
Quality and Safety Coordinators also provide training to staff regarding safety practices and quality control processes, creating a culture of awareness within the organization.
They are also expected to stay updated on the latest health and safety regulations and industry best practices.
In the case of accidents, they lead investigations to identify the cause and prevent future incidents.
They also play a crucial role in improving the quality of products or services by facilitating changes and improvements in production or service delivery processes.
These professionals play a significant role in ensuring the wellbeing of employees and the reputation of the organization in delivering quality products and services.
Quality and Safety Coordinator Qualifications and Skills
A competent Quality and Safety Coordinator should have the skills and qualifications that align with your job description, such as:
- Proficiency in implementing and managing quality control systems, ensuring adherence to company and legal standards.
- Strong knowledge of safety and health protocols, regulations and procedures to ensure a safe working environment.
- Exceptional organizational skills to manage multiple tasks and projects concurrently, ensuring the timely completion of all projects.
- Ability to analyze data and create comprehensive reports regarding quality and safety performance.
- Excellent communication skills to efficiently relay information to staff, management, and regulatory bodies concerning quality and safety measures.
- Problem-solving skills to identify potential safety hazards or quality issues and implement effective solutions promptly.
- Proficient in conducting safety training sessions and seminars, ensuring all staff members are aware of safety regulations and quality expectations.
- Strong leadership abilities to guide and motivate team members towards adherence to quality standards and safety regulations.
- Ability to stay updated with latest tools, technologies and trends in the field of quality and safety management.
Quality and Safety Coordinator Experience Requirements
To become a Quality and Safety Coordinator, candidates typically need to have at least 2 to 3 years of experience in a quality control, safety, or related field.
This experience can be acquired through full-time roles, internships, or part-time roles in industries such as manufacturing, construction, healthcare, or any other industry that prioritizes safety and quality standards.
Candidates with a background in engineering, occupational safety, or quality management are often well-suited for this role.
Having hands-on experience with safety equipment, quality control tools, and software related to safety management systems is also beneficial.
For more advanced positions, candidates may be required to have 5 or more years of experience in the field.
They should have strong knowledge of quality assurance systems, safety regulations, and industry-specific protocols.
Those with leadership experience may also be well-suited for higher level positions or roles that involve managing a team of quality and safety professionals.
In addition to this, professional certifications such as Certified Safety Professional (CSP) or Certified Quality Auditor (CQA) can add value to a candidate’s profile and might be required for some roles.
Quality and Safety Coordinator Education and Training Requirements
Quality and Safety Coordinators are typically required to have a bachelor’s degree in quality management, safety management, or a related field.
A solid understanding of quality assurance processes, safety protocols, and regulatory compliance is necessary for this role.
They should also have knowledge about relevant health and safety laws and regulations.
For entry-level positions, few years of experience in quality assurance or safety management is usually required.
In more senior roles, employers may prefer candidates with significant experience in managing quality and safety programs.
Candidates may also need to possess certain professional certifications, such as the Certified Safety Professional (CSP) or Certified Quality Auditor (CQA), which demonstrate proficiency in the field.
These certifications are usually obtained after graduation and involve rigorous training and examination processes.
In addition to these basic education and certification requirements, a Quality and Safety Coordinator should possess strong analytical, problem-solving, and communication skills.
They also need to be detail-oriented to identify any potential hazards and assess the quality of operations.
Continuing education is important in this role to stay updated with changes in laws and regulations as well as the latest best practices in safety and quality management.
Therefore, ongoing training and professional development are often required.
Quality and Safety Coordinator Salary Expectations
A Quality and Safety Coordinator earns an average salary of $60,000 (USD) per year.
However, the salary can vary depending on the individual’s level of experience, the size and sector of the employing company, and the location of employment.
Quality and Safety Coordinator Job Description FAQs
What skills does a Quality and Safety Coordinator need?
Quality and Safety Coordinators need a blend of analytical and interpersonal skills.
They should be able to interpret safety regulations and establish protocols to meet those regulations.
Additionally, they should have good problem-solving abilities to identify and rectify safety concerns in the workplace.
Strong communication skills are crucial in conveying safety procedures to employees and management.
Do Quality and Safety Coordinators need a degree?
Typically, a Quality and Safety Coordinator needs a bachelor’s degree in occupational safety, industrial hygiene, environmental science or a related field.
However, extensive experience in safety management can sometimes substitute for educational requirements.
Many employers also prefer candidates with professional certifications, such as the Certified Safety Professional (CSP) or Certified Industrial Hygienist (CIH).
What should you look for in a Quality and Safety Coordinator’s resume?
Firstly, ensure the candidate possesses the necessary educational qualifications or equivalent experience.
Check for professional certifications and experiences in implementing safety regulations in previous roles.
Proficiency in safety management software and knowledge of industry-specific safety standards can also be beneficial.
Additionally, look for evidence of strong communication and analytical skills.
What qualities make a good Quality and Safety Coordinator?
A good Quality and Safety Coordinator is proactive, detail-oriented, and has a strong understanding of safety regulations and procedures.
They should be able to maintain compliance, even when under pressure or facing tight deadlines.
Strong communication skills are vital for relaying information effectively to all levels of the organization.
They should also be committed to continuous learning to stay up-to-date with the latest safety standards and best practices.
How critical is the role of a Quality and Safety Coordinator in an organization?
Quality and Safety Coordinators play a vital role in maintaining a safe and healthy work environment.
They develop and implement safety protocols, ensure compliance with federal and state safety regulations, conduct safety training, and investigate accidents.
Their efforts directly impact the well-being of employees and can significantly influence the organization’s reputation and legal compliance.
Conclusion
There you have it.
Today, we have unveiled the true essence of what it means to be a Quality and Safety Coordinator.
Guess what?
It’s not just about ensuring compliance.
It’s about sculpting a safer and better future, one quality check at a time.
With our definitive Quality and Safety Coordinator job description template and concrete examples, you’re ready to make your next move.
But why limit yourself?
Dive further with our job description generator. It’s your key to creating precision-crafted job listings or polishing your resume to brilliance.
Remember:
Every quality check contributes to the larger objective.
Let’s forge that safer future. Together.
How to Become a Quality and Safety Coordinator (Complete Guide)
AI’s Employment Invasion: Which Jobs Are on the Line?
The Fun-Loving Work: Enjoyable Careers That Are Never Dull
Career Champions: The Most Prestigious Jobs in the Industry
No Suit, No Problem: Remote Jobs with Six-Figure Potentials!