Safety Engineer Job Description [Updated for 2025]
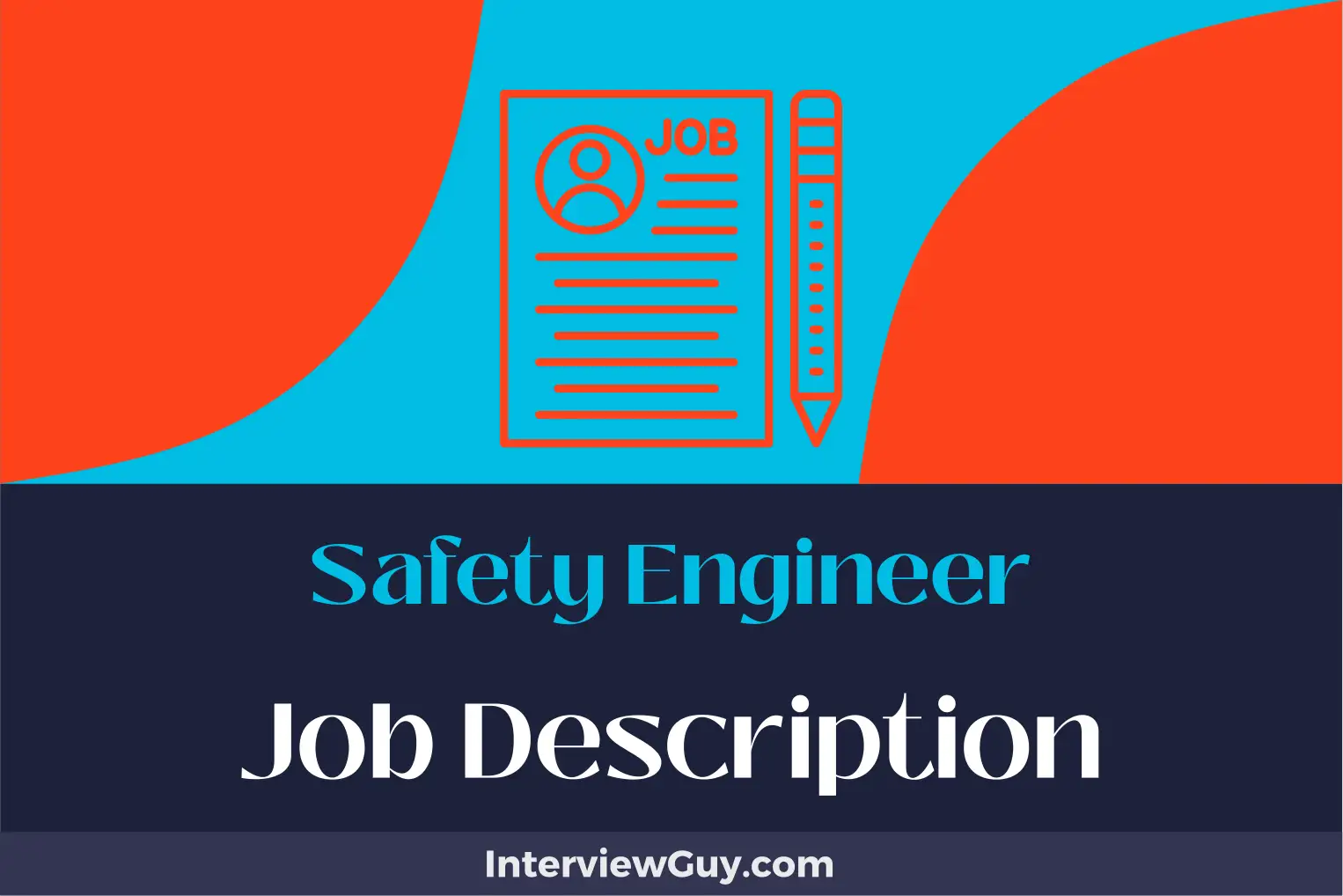
In this era of unprecedented safety concerns, the role of safety engineers has become more crucial than ever before.
As the complexity of our environments and technologies increases, so does the demand for proficient individuals who can design, implement, and ensure the robustness of our safety systems.
But what exactly is expected from a safety engineer?
Whether you are:
- A job seeker attempting to understand the core responsibilities of this role,
- A hiring manager delineating the perfect candidate,
- Or simply curious about the intricacies of safety engineering,
You’ve come to the right place.
Today, we present a comprehensive safety engineer job description template, designed for effortless posting on job boards or career websites.
Let’s dive right into it.
Safety Engineer Duties and Responsibilities
Safety Engineers work to ensure all safety protocols are followed within a company, identifying potential risks and implementing preventive measures.
They combine knowledge of engineering and health and safety to make sure the work environment is as safe as possible.
The duties and responsibilities of a Safety Engineer include:
- Inspect facilities, machinery, and safety equipment to identify and correct potential hazards, and to ensure safety regulation compliance.
- Conduct or coordinate worker training in areas such as safety laws and regulations, hazardous condition monitoring, and use of safety equipment.
- Investigate industrial accidents, near-miss incidents, and occupational injuries to determine causes, install preventive measures, and manage return-to-work activities.
- Recommend process and product safety features that will reduce employees’ exposure to chemical, physical, and biological work hazards.
- Compile, analyze, and interpret statistical data related to occupational illnesses and accidents.
- Prepare reports on occurrence of accidents, causes and hazard control, for equipment and machinery.
- Develop, implement, and manage health and safety plans and data for the employer’s facilities.
- Conduct safety audits to evaluate the effectiveness of Health and Safety programs.
Safety Engineer Job Description Template
Job Brief
We are seeking a dedicated Safety Engineer to ensure our operations comply with health and safety standards.
The Safety Engineer will be responsible for developing and implementing health and safety programs, conducting safety audits, and providing training to staff on safety practices.
The ideal candidate should have a solid understanding of occupational hazards, safety precautions, and industry regulations.
Ultimately, the Safety Engineer’s role is to ensure that our workplace is safe and conducive to optimal productivity.
Responsibilities
- Develop and execute health and safety plans in the workplace according to legal guidelines.
- Conduct regular safety audits to identify potential hazards and implement preventative measures.
- Develop policies to ensure safety of an environment, its customers and employees.
- Inspect equipment and machinery to observe possible unsafe conditions.
- Investigate accidents or incidents to discover causes and handle worker’s compensation claims.
- Recommend solutions to issues that need improvement.
- Prepare reports on occurrences and provide statistical information to upper management.
Qualifications
- Proven experience as a Safety Engineer or similar role in the safety management field.
- Thorough knowledge of health and safety regulations and industry practices.
- Experience in writing policies and procedures for health and safety.
- Excellent analytical and problem-solving abilities.
- Outstanding organizational and motivational skills.
- In-depth knowledge of potentially hazardous materials or practices.
- BSc/BA in safety management or relevant field is preferred.
Benefits
- 401(k)
- Health insurance
- Dental insurance
- Retirement plan
- Paid time off
- Professional development opportunities
Additional Information
- Job Title: Safety Engineer
- Work Environment: This role primarily operates in a professional office environment and involves frequent use of computer systems, telephones, and other office equipment. Field visits may also be required.
- Reporting Structure: Reports to the Safety Manager or Director of Safety.
- Salary: Salary is based upon candidate experience and qualifications, as well as market and business considerations.
- Pay Range: $70,000 minimum to $120,000 maximum
- Location: [City, State] (specify the location or indicate if remote)
- Employment Type: Full-time
- Equal Opportunity Statement: We are an equal opportunity employer and value diversity at our company. We do not discriminate on the basis of race, religion, color, national origin, gender, sexual orientation, age, marital status, veteran status, or disability status.
- Application Instructions: Please submit your resume and a cover letter outlining your qualifications and experience to [email address or application portal].
What Does a Safety Engineer Do?
Safety Engineers work primarily in industrial and manufacturing environments where they identify and eliminate potential safety hazards.
They can also find employment in construction, healthcare, and other industries where safety is a priority.
They work closely with management, employees, and often regulatory bodies to create and implement safety procedures and policies that align with state and federal safety standards.
They also conduct regular safety inspections and audits to ensure the adherence to these policies.
Their job includes the identification, evaluation, and control of various hazards in the workplace.
This involves evaluating equipment, materials, and processes to identify potential risk factors, and then implementing appropriate control measures.
Safety Engineers are also responsible for preparing reports that detail their findings during inspections and audits.
These reports can be used by the company to make informed decisions about improving safety measures.
In case of accidents or incidents, Safety Engineers analyze the causes and effects, and recommend changes to prevent future occurrences.
In addition, they may also conduct safety training programs for employees to raise awareness about workplace safety and ensure everyone is knowledgeable about the company’s safety policies.
They may also be involved in designing safety features and systems for new facilities or products.
Safety Engineer Qualifications and Skills
Safety Engineers must have a diverse set of technical skills, industry knowledge and soft skills to ensure the safety and wellbeing of people in a variety of settings, including:
- Understanding of safety laws, regulations, and industry standards, as well as the ability to apply them in practical scenarios.
- Technical knowledge and skills to identify and understand potential hazards, risks or dangerous conditions in various environments and work processes.
- Problem-solving skills to effectively and efficiently devise strategies and measures to mitigate or eliminate safety risks.
- Strong communication skills to effectively convey safety protocols and procedures to teams, as well as to report to management about safety compliance and issues.
- Interpersonal skills to build rapport and work effectively with various teams and individuals across all levels of the organization.
- Attention to detail and organizational skills to maintain and manage safety documentation, inspections records and incident reports.
- Ability to conduct safety training and drills, and ensure the implementation of safety procedures and protocols.
Safety Engineer Experience Requirements
Safety Engineers are typically required to have a bachelor’s degree in safety engineering, industrial engineering or a related field, which provides them with a foundational understanding of safety procedures and laws.
Entry-level Safety Engineers may have 1 to 2 years of experience, often acquired through internships or part-time roles in industries such as manufacturing, construction, or oil and gas where safety procedures are a priority.
This early experience helps them understand practical aspects of safety protocols, hazard prevention, and risk management.
Candidates with 3 to 5 years of experience usually have more advanced skills, such as ability to develop and implement safety programs, conduct safety audits, and utilize advanced tools and technologies for hazard detection and risk assessment.
They may also have experience with regulatory compliance and may have worked on cross-functional teams to ensure workplace safety.
Those with more than 5 years of experience are typically considered senior Safety Engineers.
They often have experience managing safety initiatives across multiple departments or large-scale projects, presenting safety trainings, and serving as the key liaison with occupational health and safety regulatory bodies.
Some may be ready for leadership roles where they oversee a team of safety professionals.
Certification, such as Certified Safety Professional (CSP) or Certified Industrial Hygienist (CIH), is often preferred and demonstrates a high level of competency and commitment to the field.
Safety Engineer Education and Training Requirements
Safety Engineers are typically required to have a bachelor’s degree in occupational health and safety, engineering, or a related field.
Courses within these programs may include industrial hygiene, toxicology, fire prevention and protection, and system safety.
Students might also learn about laws and regulations regarding safety in their respective fields.
Many employers prefer to hire safety engineers who have professional certification.
The most common certification is the Certified Safety Professional (CSP) designation, which can be earned through the Board of Certified Safety Professionals.
For some more complex roles, a master’s degree in safety engineering or a related discipline may be required.
These advanced degree programs usually cover more specialized areas, such as risk management and assessment, accident investigation, safety culture, and advanced safety management.
In addition to education and certification, safety engineers should also have good problem-solving and communication skills.
They often work in a team setting and must be able to identify and solve safety issues effectively.
Continuing education is critical in this field, to stay updated with new safety laws and regulations, and the latest best practices in safety management.
This could involve attending training workshops, webinars or industry conferences, or pursuing additional certifications.
Safety Engineer Salary Expectations
A Safety Engineer can expect to earn an average salary of $89,000 (USD) per year.
The actual salary can differ based on factors such as years of experience, specialization in the field, and the location of the job.
Safety Engineer Job Description FAQs
What skills does a safety engineer need?
A safety engineer needs to have excellent problem-solving skills to identify potential hazards and find ways to prevent them.
They should possess thorough knowledge of safety protocols and regulations in their field.
They should also have good communication skills to provide safety training and advice to others, as well as technical skills to use safety equipment and software.
Do safety engineers need a degree?
Yes, safety engineers need at least a bachelor’s degree in safety engineering, industrial engineering, or a related field.
Some roles may require a master’s degree or professional certifications like Certified Safety Professional (CSP) or Certified Industrial Hygienist (CIH).
In many places, safety engineers also need to be licensed.
What should you look for in a safety engineer resume?
When reviewing a safety engineer’s resume, it is critical to look for a degree in safety or industrial engineering or a related field.
Industry-specific experience is valuable, so look for experience in your particular field.
Certifications like CSP or CIH are also worth noting.
Additionally, look for evidence of skills like problem-solving, communication, and attention to detail.
What qualities make a good safety engineer?
A good safety engineer is diligent and detail-oriented, able to notice small details that could lead to safety hazards.
They are excellent communicators, able to effectively provide safety training and explain complex safety concepts to a non-technical audience.
They are also proactive, consistently staying updated on the latest safety regulations and best practices.
Is it difficult to hire safety engineers?
Hiring safety engineers can be challenging due to the specificity of the role and the need for industry-specific experience.
Furthermore, there is a high demand for qualified safety engineers as more companies prioritize safety regulations.
Offering competitive salaries, clear career advancement opportunities, and a positive work environment can help attract quality candidates.
Conclusion
And there you have it.
Today, we’ve shed light on the true essence of being a safety engineer.
And guess what?
It’s not just about enforcing safety regulations.
It’s about creating a safe and secure future, one safety protocol at a time.
With our comprehensive safety engineer job description template and real-world examples, you’re ready to step into action.
But why limit yourself?
Delve further with our job description generator. It’s your key to crafting precise job listings or honing your resume to perfection.
Remember:
Every safety measure contributes to a more secure environment.
Let’s create that future. Together.
How to Become a Safety Engineer (Complete Guide)
Quirky Quests: The Strangest Jobs You Could Pursue
The Crème de la Crème: Most Prestigious Jobs in the Corporate World
The Financial Forts: Jobs That Stand Strong Against Recessions
Lifestyle-Friendly Careers: The Most Flexible Jobs for Personal Balance