26 Disadvantages of Being a Supplier Quality Engineer (Audit Aggravations Abound)
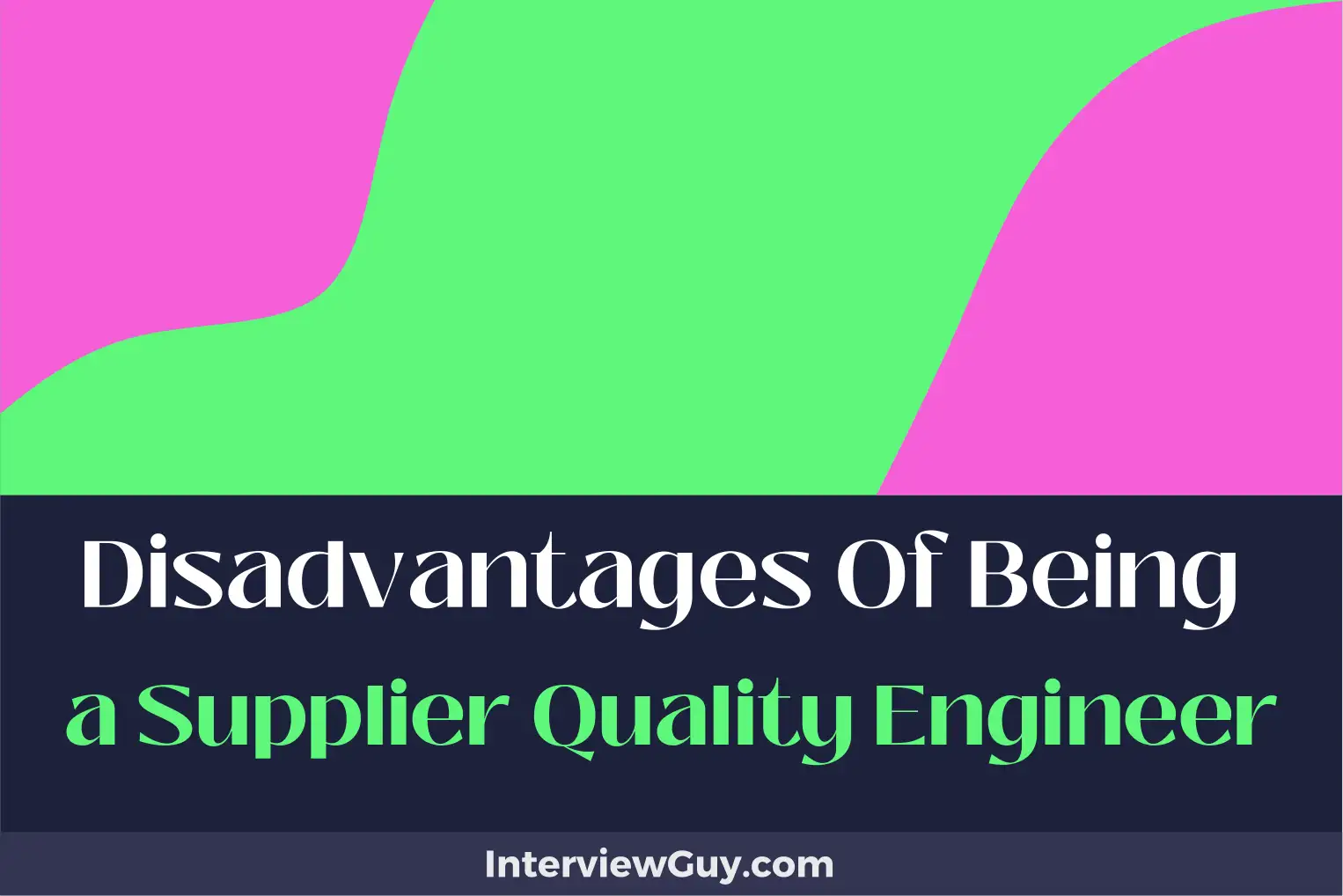
Considering a career as a Supplier Quality Engineer?
It’s easy to be attracted by the prospects:
- Opportunities for career advancement.
- Attractive salary prospects.
- The satisfaction of ensuring high-quality supplies for production.
However, there are other facets to consider.
Today, we’re diving deep. Really deep.
Into the challenging, the demanding, and the downright difficult aspects of being a Supplier Quality Engineer.
Complex technical knowledge requirements? Check.
Significant responsibilities and stress? Definitely.
Dealing with supplier issues and discrepancies? Absolutely.
And let’s not forget the constant pressure to maintain quality standards.
So, if you’re contemplating a career in Supplier Quality Engineering, or just interested in the less glamorous side of this profession…
Keep reading.
You’re about to get a comprehensive look at the disadvantages of being a Supplier Quality Engineer.
Frequent Travel for Supplier Audits and Assessments
Supplier Quality Engineers often need to travel extensively to conduct supplier audits and assessments.
This means they may need to spend a significant amount of time away from home, which can be physically and emotionally draining.
The requirement of frequent travel can lead to a disrupted work-life balance as they may need to travel over weekends, holidays or on short notice.
While travel can be exciting and provide opportunities to see new places, it can also be tiring, stressful and time-consuming.
This is especially challenging for those with families or other personal commitments.
Moreover, Supplier Quality Engineers are often required to prepare extensive reports after each visit, which can add to their workload.
This can make it challenging to maintain a regular schedule and can lead to job burnout over time.
High Pressure to Ensure Supplier Compliance with Quality Standards
Supplier Quality Engineers are often under immense pressure to ensure suppliers’ compliance with rigorous quality standards.
This role requires constant scrutiny of supplier processes, materials, and outputs to make sure they meet all necessary regulations and quality benchmarks.
This can involve complex audits, assessments, and frequent interaction with suppliers, making it a high-stress job.
The repercussions of a supplier not meeting required standards can be significant, including halting production lines or even legal issues.
Thus, the weight of responsibility and the continuous need for attention to detail can lead to a stressful and demanding work environment for a Supplier Quality Engineer.
Managing Complex Relationships with Multiple Suppliers
Supplier Quality Engineers often face the challenge of managing complex relationships with multiple suppliers.
They have to ensure the quality of products or components received from various suppliers, which can be difficult when dealing with multiple vendors across different locations.
This includes constant communication, coordination, and negotiation, which can be a time-consuming and demanding task.
In addition, Supplier Quality Engineers also have to handle any issues or conflicts that may arise with suppliers, including delivery delays, quality issues, or disputes over contracts.
This can sometimes lead to stressful situations and require strong problem-solving and negotiation skills.
The ability to maintain good relationships with suppliers while ensuring the highest quality is a challenging part of the job.
Constantly Adapting to New Regulatory Requirements
Supplier Quality Engineers are required to constantly keep up with and adapt to new regulatory requirements in the industry.
Regulatory bodies often update their standards and regulations to ensure maximum safety and quality, and staying informed about these changes is crucial for a Supplier Quality Engineer.
This means they need to continuously learn and understand new regulations, and then apply them in their work, which can be challenging and time-consuming.
Failure to comply with the latest regulations can lead to penalties, product recalls, and a damaged reputation for the company.
This constant need for adaptation can make the role stressful and demanding.
Difficulty in Enforcing Corrective Actions with Suppliers
Supplier Quality Engineers often face challenges when it comes to enforcing corrective actions with suppliers.
They are responsible for ensuring that suppliers meet the quality standards set by their company.
However, getting suppliers to make necessary changes or improvements can be a daunting task.
Suppliers may resist making these changes due to the cost or time required to implement them.
This can lead to tension and strained relationships between the supplier quality engineer and the suppliers.
The Supplier Quality Engineer also needs to manage these relationships carefully to ensure ongoing supply of goods, whilst maintaining the quality standards of their company.
This requires skillful negotiation and diplomacy, and can be a significant source of stress in the role.
Potential Language and Cultural Barriers in Global Supply Chain
Supplier Quality Engineers often have to deal with suppliers from various parts of the world, making language and cultural differences a potential challenge.
With increasing globalization, it’s not uncommon for a Supplier Quality Engineer to manage suppliers from different countries.
This necessitates effective communication in different languages, understanding of various cultural norms and business practices, and the ability to adapt quickly to these differences.
Miscommunication or misunderstanding due to language or cultural barriers can lead to crucial errors, affecting the quality of the product or delaying the supply chain process.
These challenges require Supplier Quality Engineers to be well-versed in international business practices and possibly even have language skills.
The constant need to navigate these barriers could add stress and complexity to the role.
Strain from Coordinating Across Different Time Zones
Supplier Quality Engineers often have to work with suppliers from all over the world.
This means coordinating across different time zones, which can be a significant strain.
It can lead to irregular working hours, as they may need to have meetings or conference calls outside of normal business hours to accommodate suppliers in different geographical locations.
This can disrupt work-life balance and may cause fatigue and stress.
Furthermore, it can also lead to delays in decision-making and communication issues due to the time difference.
This constant need for flexibility can make the job challenging and demanding.
Risks of Supply Chain Disruptions Affecting Quality Assurance
As a Supplier Quality Engineer, you are always at the mercy of potential disruptions in the supply chain.
These disruptions can have a significant impact on your ability to ensure quality.
For instance, a delay in the delivery of raw materials can slow down the production process, causing a domino effect that could ultimately lead to the production of substandard products.
Furthermore, if a supplier’s quality standards decline, it may take time to find a new supplier who can meet the necessary standards.
This constant variability can make the job stressful and demanding.
It also requires a high level of adaptability and problem-solving skills, as it often involves dealing with unforeseen challenges and making quick decisions to mitigate quality risks.
The Need for Meticulous Record Keeping and Documentation
Supplier Quality Engineers are required to maintain thorough and accurate records at all times.
They must document every aspect of the supplier quality process, including supplier performance, audit results, and any issues or non-conformances that arise.
This meticulous record-keeping can be time-consuming and requires a high level of detail and accuracy.
It’s not just about keeping track of data, but also being able to analyze and interpret it to identify trends and issues.
This rigorous documentation is essential to ensuring product quality and compliance with industry standards, but it can also add to the workload and stress of the role.
Mistakes or oversights in documentation can potentially lead to serious quality issues, regulatory non-compliance, and financial losses, making this aspect of the role particularly challenging.
Balancing Cost Management with Quality Control Objectives
Supplier Quality Engineers face a constant challenge of balancing cost management with quality control objectives.
On one hand, they are tasked with ensuring that the products or services provided by suppliers meet the necessary quality standards.
This often involves implementing and maintaining rigorous quality control systems, conducting audits, and ensuring compliance with industry regulations.
On the other hand, they also have to keep in mind the costs involved in these processes.
Ensuring high-quality supplies often means higher costs, which can impact the overall budget of the organization.
Therefore, Supplier Quality Engineers are often in a position where they have to make tough decisions, balancing the need for high quality with the need to control costs.
This constant juggling of roles can often lead to stress and job fatigue.
Stress From Rapidly Changing Industry Standards and Technologies
Supplier Quality Engineers are constantly facing the stress that comes with the rapidly evolving industry standards and technologies.
The manufacturing and supply chain industry is ever-evolving, with new processes, materials, and technologies being introduced regularly.
As a Supplier Quality Engineer, one must stay updated with these changes to ensure the suppliers are adhering to the latest quality standards.
This involves constant learning and adapting, which can be stressful.
Furthermore, they are also responsible for implementing these changes in their suppliers’ processes which often involves overcoming resistance and managing change.
This constant adaptation can lead to job burnout and stress, affecting their work-life balance.
Challenges in Aligning Supplier Processes with Company Quality Goals
A Supplier Quality Engineer often faces the challenge of aligning supplier processes with the company’s quality goals.
Suppliers may have different standards, processes, or methods that do not necessarily align with your company’s requirements for quality.
It’s the engineer’s responsibility to ensure the supplier meets these standards, which may involve frequent audits, detailed inspections, and constant communication.
This process can be time-consuming, stressful, and may lead to conflicts if the supplier is resistant to changes.
Furthermore, the engineer often has to manage multiple suppliers, adding to the complexity and the potential for discrepancies.
Despite these challenges, this role is crucial in maintaining the quality of the products and ensuring customer satisfaction.
Limited Control Over Supplier Internal Processes and Procedures
Supplier Quality Engineers often face the challenge of having limited control over the internal processes and procedures of suppliers.
They are responsible for ensuring that the products supplied by these businesses meet the quality standards of their own organization.
However, they may not have the authority or ability to make changes to the supplier’s manufacturing or quality control processes, even if they identify areas of concern.
This can be frustrating, as it may impact the consistency and reliability of the products they receive.
In some cases, they may need to rely on their negotiation skills and the strength of their relationship with the supplier to influence changes, but success is not always guaranteed.
This lack of control can lead to increased risk of product failures, delays, or even recalls, all of which can negatively affect the organization’s bottom line and reputation.
Requirement to Stay Current with Continuous Industry Training
Just like many other engineering fields, the role of a Supplier Quality Engineer requires continuous education and training in order to stay current with industry standards and practices.
This might include learning about new quality control methods, advanced statistical techniques, or the latest manufacturing technologies.
As the industry evolves, so too must the knowledge and skills of the Supplier Quality Engineer.
This continuous learning requires a significant time commitment and can be stressful, particularly when balancing it with the day-to-day demands of the job.
On the other hand, it does provide an opportunity for continuous professional growth and the ability to stay ahead in the competitive field.
Managing Liability and Accountability for Supplier Shortcomings
Supplier Quality Engineers have the challenging task of managing the liability and accountability for any shortcomings from the supplier side.
This may include product defects, late deliveries, or non-compliance with regulatory standards.
They are expected to mitigate these risks and ensure that the supplied goods are of high quality and delivered on time.
Despite their best efforts, there can be situations where suppliers fail to meet the standards or deadlines due to unforeseen circumstances.
In such cases, the Supplier Quality Engineer may face criticism or even penalties.
This role demands a high level of stress management, problem-solving skills and the ability to handle pressure from both the organization and the suppliers.
Supplier Quality Engineers often face the challenge of meeting varied expectations and quality standards across different departments in an organization.
Each department may have its own unique requirements and quality standards for the supplier’s products, which the engineer must understand and incorporate into the supplier quality management plan.
This could lead to conflicting expectations and the need to strike a balance between different departments’ needs, which can be a complex and time-consuming task.
Additionally, this role requires constant updating of knowledge about different quality standards and regulatory requirements, which might require additional training and could lead to increased job stress.
Time Constraints for Implementing and Verifying Improvements
Supplier Quality Engineers often face strict time constraints when it comes to implementing and verifying improvements in the supply chain.
Since their role involves ensuring that the quality of materials from suppliers meets the company’s standards, any proposed improvements or changes need to be implemented swiftly to avoid disrupting the production process.
This means they often have to work under pressure to ensure that changes are not only effective but also implemented in a timely manner.
Furthermore, verifying these improvements can be a time-consuming process that involves rigorous testing and analysis.
Thus, Supplier Quality Engineers may often find themselves working long hours to meet these time constraints, which can lead to work-life imbalance.
Working with Complex Technical Specifications and Standards
As a Supplier Quality Engineer, one must handle complex technical specifications and standards.
This requires a solid understanding of engineering principles and concepts, along with the ability to interpret and apply these standards effectively.
The work often involves dealing with intricate and complex blueprints, technical guidelines, and design specifications.
This can be challenging and time-consuming, with the risk of making mistakes if the specifications are not understood correctly.
Additionally, staying updated with ever-changing technical standards and industry regulations requires continuous learning and adaptation.
It also demands a high level of attention to detail and problem-solving skills, which can be stressful and demanding.
Ensuring Consistent Quality Across Diverse Supplier Products
One of the main challenges that a Supplier Quality Engineer may face is the assurance of consistent quality across a wide variety of supplier products.
They are tasked with ensuring that all products received from different suppliers meet the company’s quality standards.
This can be particularly challenging when dealing with suppliers from various parts of the world, each with their own manufacturing processes and quality control measures.
Moreover, it requires a deep understanding of diverse product types, materials, and manufacturing processes, which can be overwhelming.
The engineer also needs to effectively communicate the company’s quality standards to suppliers who may have different cultural or language barriers.
Dealing with non-compliant suppliers and resolving quality issues can also be stressful and time-consuming.
Dealing with Resistance to Changes in Supplier Management
A significant disadvantage of being a Supplier Quality Engineer is the constant need to deal with resistance to changes in supplier management.
Changes may be necessary to improve product quality, reduce costs or enhance supply chain efficiency.
However, suppliers, and sometimes even internal stakeholders, may resist these changes due to inconvenience, fear of unknown results, or lack of understanding of the benefits.
This resistance can slow down the implementation of necessary improvements and cause additional stress and frustration for the Supplier Quality Engineer.
The role often requires a great deal of diplomacy, persuasive skills, and patience to communicate the need for change effectively and to manage the transition smoothly.
Pressure to Qualify New Suppliers Quickly to Meet Demand
Supplier Quality Engineers often face the challenge of qualifying new suppliers rapidly to meet the high demand.
Due to the need for constant production and the potential for existing suppliers to fall short, there is a high pressure to find and validate new suppliers swiftly.
This can lead to long hours, increased stress, and the risk of overlooking crucial details in the qualification process, which may impact the quality of the products or services.
Moreover, the need to meet tight deadlines may also affect the negotiation process, potentially leading to less advantageous terms for the company.
This pressure can lead to burnout, decreased job satisfaction, and potentially costly mistakes if the qualification process is not properly managed.
Risk of Reputational Damage from Supplier Quality Failures
Supplier Quality Engineers are often tasked with ensuring that the quality of the goods and services supplied by external vendors are up to the standards of the company.
However, if a supplier fails to meet quality standards, the repercussions can be damaging for the company’s reputation.
The Supplier Quality Engineer is often the one held responsible for such failures, even though they might not have direct control over the supplier’s operations.
This can lead to a significant amount of stress and pressure on the engineer, as their professional reputation is closely tied to the performance of their suppliers.
Additionally, repeated supplier quality failures can negatively impact the engineer’s career progression, as it may reflect poorly on their ability to effectively manage and control their supplier portfolio.
Potential for Conflict of Interest in Supplier Selection
Supplier Quality Engineers play a crucial role in the selection and management of suppliers.
However, this responsibility can sometimes lead to a potential conflict of interest.
They may be pressured by management or other parties to select certain suppliers, not based on their quality, reliability, or value, but due to personal relationships, financial incentives, or other non-professional reasons.
This not only compromises the integrity of the role but can also negatively impact the overall product quality and company reputation.
It is important for Supplier Quality Engineers to maintain a high level of ethical conduct and impartiality in their role, but the pressure to do otherwise can be a significant disadvantage in this profession.
Difficulty in Achieving Lean Manufacturing Goals With Supplier Limitations
Supplier Quality Engineers often face challenges in achieving lean manufacturing goals due to supplier limitations.
Lean manufacturing is a practice that emphasizes the minimization of waste within a manufacturing system without sacrificing productivity.
However, not all suppliers may have the same understanding or ability to implement lean manufacturing principles.
This can lead to inefficiencies such as excess inventory, overproduction, and unnecessary transportation, all of which can increase costs and production time.
Supplier Quality Engineers may need to spend considerable time and effort in training suppliers, optimizing production processes, and continuously monitoring for compliance to maintain quality standards.
This can add to the complexity and stress of the role, particularly in industries where margins are tight and efficiency is key.
Transparency Challenges in the Supply Chain
As a supplier quality engineer, you are responsible for assessing and improving the quality systems of vendors to ensure that the products received meet the company’s standards.
However, a major challenge associated with this role is transparency in the supply chain.
Suppliers may have complex networks and processes that they do not fully disclose.
This lack of transparency can make it difficult to identify and address quality issues.
Furthermore, if there are multiple suppliers involved, tracing the origin of a quality problem can be an arduous task.
This may result in delays and increased costs for the company.
In addition, the lack of transparency can also lead to strained relationships with suppliers, as issues may be wrongly attributed due to inadequate information.
Handling Unpredictable Costs Due to Fluctuations in Quality Levels
Supplier Quality Engineers often face the challenge of handling unpredictable costs due to fluctuations in quality levels.
This role requires working with suppliers to ensure that all products meet the required standards.
However, the quality of materials or components supplied can vary, leading to additional costs.
For instance, if a batch of components is found to be substandard during quality testing, it may need to be discarded or reworked, resulting in additional costs.
Furthermore, fluctuations in quality levels can also lead to delays in production, which can have financial implications.
These unpredictable costs can make budgeting difficult and increase financial stress.
Additionally, these issues can also affect the overall timeline of a project, increasing the pressure on the Supplier Quality Engineer.
Conclusion
And there you have it.
A candid exploration of the disadvantages of being a supplier quality engineer.
It’s not just about inspecting, testing, and validating.
It’s challenging. It’s commitment. It’s traversing a labyrinth of technical and operational complexities.
But it’s also about the fulfillment of delivering quality.
The satisfaction of being the guardian of the supply chain.
The excitement of knowing you played a role in maintaining the integrity of a product.
Yes, the journey is demanding. But the rewards? They can be remarkable.
If you’re nodding along, thinking, “Yes, this is the challenge I’ve been seeking,” we’ve got something more for you.
Check out our detailed guide on the reasons to be a supplier quality engineer.
If you’re ready to embrace both the ups and the downs…
To learn, to evolve, and to excel in this multifaceted field…
Then maybe, just maybe, a career as a supplier quality engineer is for you.
So, take the leap.
Investigate, immerse, and innovate.
The world of supplier quality engineering awaits.
The Job Jokers: The Most Hated Jobs in the Career Arena
AI’s Limitations: Professions Where Humans Are Irreplaceable
Weirdly Working: The Most Unusual Jobs You Can Get