Industrial Fabric Manager Job Description [Updated for 2025]
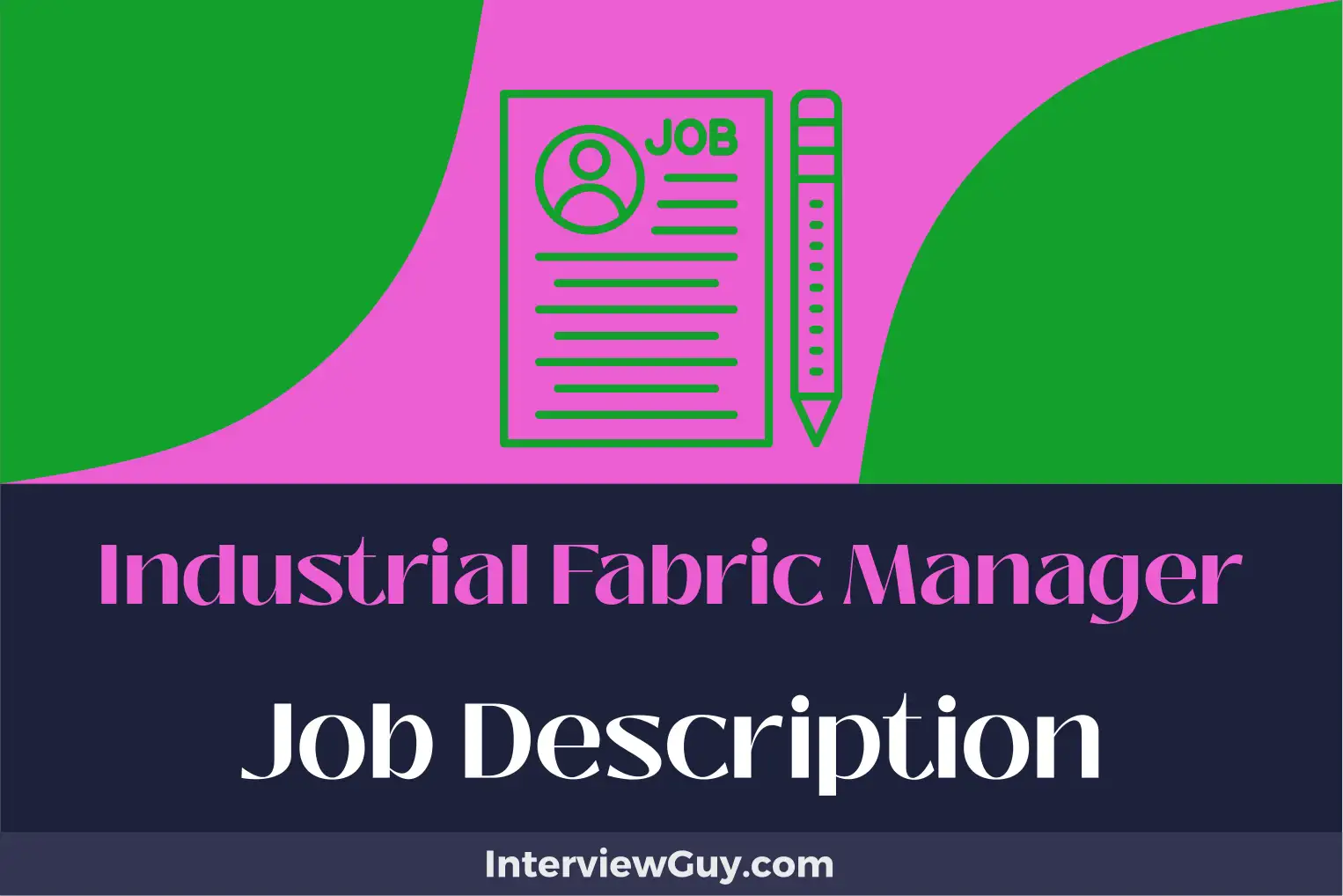
In the era of rapid industrial advancement, the spotlight on industrial fabric managers has never been brighter.
As industries continue to evolve, the demand for skilled professionals who can manage, develop, and ensure the quality of industrial fabrics becomes increasingly critical.
But let’s delve deeper: What’s truly expected from an industrial fabric manager?
Whether you are:
- A job seeker trying to understand the core responsibilities of this role,
- A hiring manager defining the perfect candidate,
- Or simply curious about the inner dynamics of industrial fabric management,
You’re in the right place.
Today, we present a customizable industrial fabric manager job description template, designed for effortless posting on job boards or career sites.
Let’s dive right into it.
Industrial Fabric Manager Duties and Responsibilities
Industrial Fabric Managers oversee the production process of various fabric materials in an industrial setting.
They are responsible for ensuring that the production is cost-effective, timely, and meets the quality standards.
The duties and responsibilities of an Industrial Fabric Manager include:
- Planning and organizing production schedules
- Assessing project and resource requirements
- Estimating, negotiating, and agreeing on budgets and timescales with clients and managers
- Ensuring that health and safety regulations are met
- Determining quality control standards
- Overseeing production processes
- Re-negotiating timescales or schedules as necessary
- Selecting, ordering, and purchasing materials
- Organizing the repair and routine maintenance of production equipment
- Liaising with buyers and marketing and sales staff
- Supervising the work of junior staff
- Organizing relevant training sessions
Industrial Fabric Manager Job Description Template
Job Brief
We are seeking a highly-skilled Industrial Fabric Manager to lead our fabric production team.
The Industrial Fabric Manager will oversee all aspects of fabric production, including planning, production scheduling, and quality control.
Our ideal candidate has a deep understanding of fabric production processes, excellent management skills, and a strong commitment to meeting company goals and objectives.
Ultimately, the role of the Industrial Fabric Manager is to ensure the production of high-quality industrial fabric that meets company standards and customer expectations.
Responsibilities
- Oversee all stages of fabric production, from raw material selection to finished product.
- Develop and implement production schedules to meet company objectives.
- Ensure quality control standards are met at all stages of production.
- Manage and supervise a team of fabric production workers.
- Coordinate with other departments to streamline production processes.
- Monitor equipment and ensure that it is properly maintained and serviced.
- Identify and implement cost-saving measures and production efficiencies.
- Stay updated with latest trends and advancements in fabric production technology.
- Ensure compliance with health and safety regulations.
Qualifications
- Proven experience as a Fabric Manager or similar role in the textile industry.
- Strong knowledge of fabric production processes and machinery.
- Excellent leadership and team management skills.
- Strong organizational and problem-solving skills.
- Proficiency in production planning software.
- Ability to work under pressure and meet production deadlines.
- BSc degree in Textile Technology, Manufacturing Engineering or relevant field.
Benefits
- 401(k)
- Health insurance
- Dental insurance
- Retirement plan
- Paid time off
- Training and development opportunities
Additional Information
- Job Title: Industrial Fabric Manager
- Work Environment: Factory setting. This role may require occasional travel to suppliers or clients.
- Reporting Structure: Reports to the Director of Manufacturing.
- Salary: Salary is based upon candidate experience and qualifications, as well as market and business considerations.
- Location: [City, State] (specify the location or indicate if remote)
- Employment Type: Full-time
- Equal Opportunity Statement: We are an equal opportunity employer and value diversity at our company. We do not discriminate on the basis of race, religion, color, national origin, gender, sexual orientation, age, marital status, veteran status, or disability status.
- Application Instructions: Please submit your resume and a cover letter outlining your qualifications and experience to [email address or application portal].
What Does an Industrial Fabric Manager Do?
Industrial Fabric Managers typically work in manufacturing industries that produce fabrics, such as textiles, clothing, carpets, or upholstery.
They can also work in technical industries that use fabrics, like automotive or aerospace production.
They are responsible for overseeing the production process, from sourcing raw materials to the final output of fabric.
This includes ensuring that the production process is efficient, cost-effective, and meets quality standards.
Industrial Fabric Managers work closely with other professionals, including designers, engineers, and production workers, to ensure that the fabric produced meets the specifications and requirements of the end product.
They are also responsible for ensuring that the production process complies with safety and environmental regulations.
This can involve implementing new production methods, technologies or materials to improve efficiency, reduce environmental impact, or improve safety.
In addition to overseeing production, Industrial Fabric Managers may also be involved in the development of new products or materials.
This can involve researching new fabric technologies, testing new materials, or working with designers to develop new products.
Ultimately, the role of an Industrial Fabric Manager is to ensure that the production process runs smoothly and efficiently, that the fabric produced is of high quality, and that the production process complies with all relevant regulations and standards.
Industrial Fabric Manager Qualifications and Skills
An Industrial Fabric Manager should possess a variety of technical and soft skills, along with industry-specific knowledge, such as:
- Management skills to efficiently coordinate and oversee the production activities and ensure optimal utilization of resources.
- Technical knowledge of fabrics, their properties, and manufacturing processes to ensure the production of high-quality products.
- Understanding of quality standards and health and safety regulations in the textile industry to maintain a safe and productive work environment.
- Strong problem-solving skills to troubleshoot production issues and implement appropriate solutions.
- Excellent communication and interpersonal skills to effectively liaise with staff, suppliers, and customers, and to facilitate a harmonious work environment.
- Attention to detail to maintain quality control, check for defects, and ensure that the finished products meet specifications.
- Leadership skills to motivate and guide the production team towards achieving set targets.
- Understanding of budgeting and performance evaluation, along with the ability to use industrial software and tools for production planning and inventory management.
Industrial Fabric Manager Experience Requirements
Entry-level candidates for the role of Industrial Fabric Manager may have 1 to 3 years of experience in the textile industry, possibly through roles such as Fabric Assistant, Product Development Assistant, or Quality Control Inspector.
This experience can be gained through internships, part-time roles, or full-time jobs after graduation from a relevant degree program.
Candidates with 3 to 5 years of experience often have a deeper understanding of fabric production processes, quality control, and supply chain management.
They may have held roles like Fabric Production Supervisor or Quality Control Manager, where they developed their technical and managerial skills.
Those with more than 5 years of experience are expected to have extensive knowledge of fabric types, manufacturing processes, industry standards, and quality assurance.
They may have held positions like Fabric Production Manager or Supply Chain Manager.
This level of experience and knowledge prepares them for the higher responsibilities associated with the role of Industrial Fabric Manager.
Candidates looking to excel as an Industrial Fabric Manager may also benefit from experience with industry-specific software for inventory management, production scheduling, and quality control.
They may also have proven experience leading teams, managing budgets, and liaising with suppliers and clients.
Industrial Fabric Manager Education and Training Requirements
Industrial Fabric Managers typically require a bachelor’s degree in textile engineering, textile management, or a related field.
They are trained to understand different types of fabrics, their creation processes, and their applications in various industries.
Knowledge about quality control, fabric testing, and production management is also necessary.
In addition to the degree, it is beneficial if the candidate has practical experience in a textile manufacturing environment.
It can be gained through internships or entry-level positions in textile companies.
Some positions might require Industrial Fabric Managers to have a master’s degree or specialization in areas like textile technology or industrial management.
Industry-specific certifications like Certified Textile Professional (CTP) or a similar designation can significantly enhance a candidate’s profile.
Lastly, they should be well versed with the latest technologies and software used in the fabric industry.
Therefore, any additional courses or certifications in these areas will be advantageous.
Continuing education through workshops, seminars, and courses is also essential to keep up with the evolving textile industry trends and technologies.
This education and training combination helps Industrial Fabric Managers to effectively oversee fabric production, manage teams, ensure quality control, and make strategic decisions.
Industrial Fabric Manager Salary Expectations
The average salary for an Industrial Fabric Manager is approximately $70,000 (USD) per year.
However, this can fluctuate based on factors such as the individual’s level of experience, the size and location of the company, and the complexity of the projects they handle.
Industrial Fabric Manager Job Description FAQs
What skills does an Industrial Fabric Manager need?
An Industrial Fabric Manager needs strong project management skills, including planning, organizing, and resource allocation.
They should also possess good knowledge of fabric materials and their properties.
Proficiency in using design software like CAD is a bonus.
They should also have excellent communication and negotiation skills as they often have to interact with suppliers and customers.
Do Industrial Fabric Managers need a degree?
Yes, typically, an Industrial Fabric Manager would need a bachelor’s degree in textile engineering, fashion technology, or a related field.
However, extensive experience in the textile industry, along with proven managerial skills, can sometimes compensate for the lack of formal education.
What should you look for in an Industrial Fabric Manager’s resume?
Look for experience in the textile or fashion industry, ideally in a managerial role.
They should have a solid understanding of fabric properties, production processes, and quality assurance methods.
Familiarity with fabric sourcing, cost analysis, and supply chain management is also valuable.
Additional qualifications like certifications in project management or textile technology can make a candidate stand out.
What qualities make a good Industrial Fabric Manager?
A good Industrial Fabric Manager should be detail-oriented to ensure the quality of fabrics and the efficiency of production processes.
They should have strong decision-making skills to manage resources and handle issues that arise during the production process.
Good negotiation skills are crucial for sourcing materials at the best prices.
They should also be good at building relationships with suppliers and customers.
Is it difficult to hire Industrial Fabric Managers?
Yes, hiring an Industrial Fabric Manager can be challenging as the role requires a unique combination of technical knowledge about fabrics and materials, managerial expertise, and industry-specific experience.
To attract the right candidates, you need to offer competitive remuneration, a positive work environment, and opportunities for professional growth.
Conclusion
And there you have it.
Today, we unraveled the intricacies of being an Industrial Fabric Manager.
And guess what?
It’s not just about managing materials.
It’s about weaving the future of the industrial fabric industry, one textile at a time.
With our indispensable Industrial Fabric Manager job description template and real-world examples, you’re ready to take the next step.
But why stop there?
Immerse yourself further with our job description generator. It’s your ultimate tool for creating precise listings or refining your resume to perfection.
Remember:
Every textile material managed is part of the bigger picture.
Let’s weave that future. Together.
How to Become an Industrial Fabric Manager (Complete Guide)
The Gleeful Gig: Enjoyable Jobs That Keep the Fun Alive
Not for the Weak: A Peek Into Careers That Challenge Mortality